KROHNE OPTISWITCH 3x00C 2wire SIL EN User Manual
Page 5
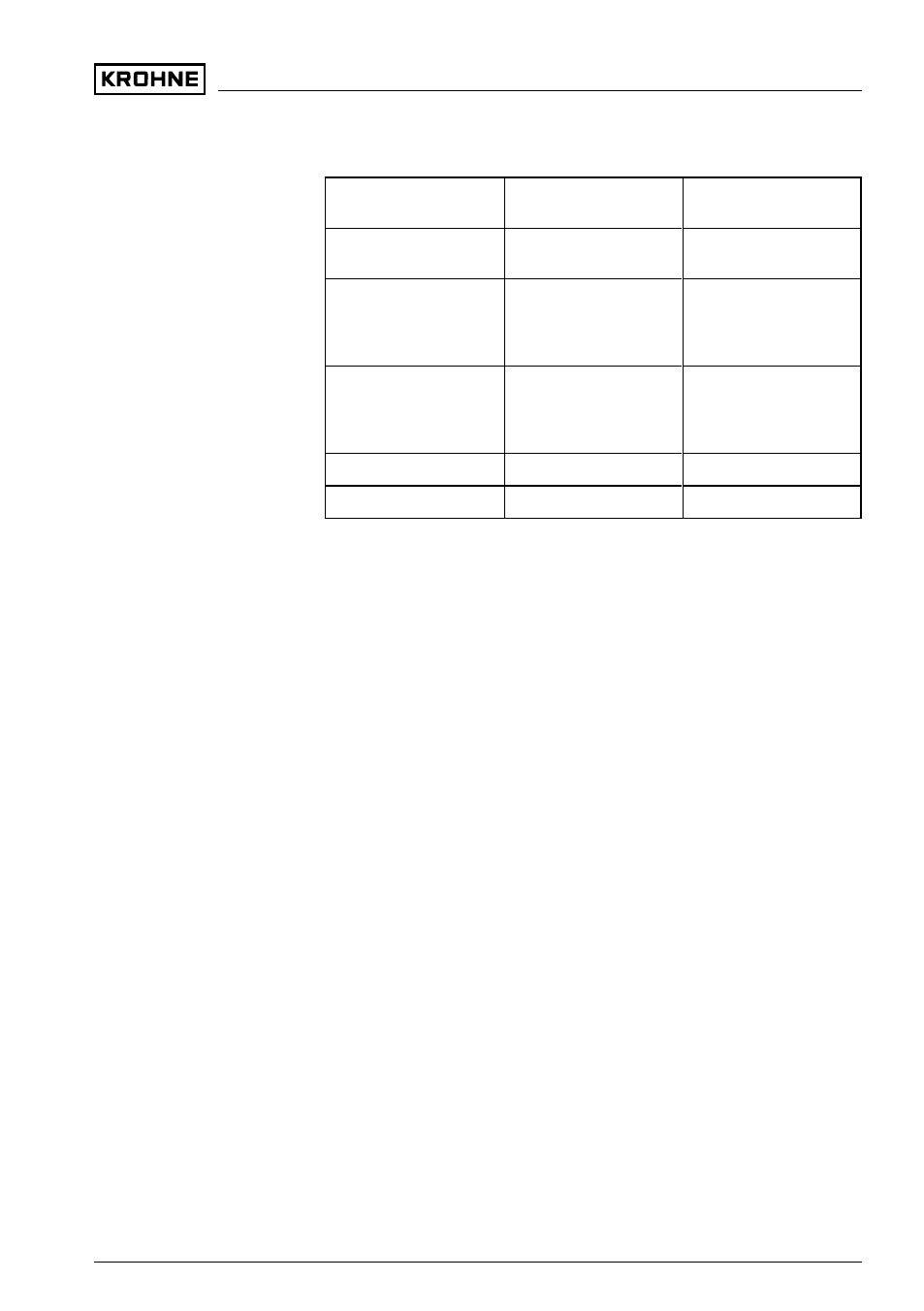
The safe state depends on the mode:
Overflow protection
(max. operation)
Dry run protection
(min. operation)
Vibrating element in safe
state
covered
uncovered
Output current in safe
condition if mode switch
on the sensor is set to
"
max."
12.5 … 23.5 mA
2.3 … 11.5 mA
Output current in safe
condition if mode switch
on the sensor is set to
"
min."
2.3 … 11.5 mA
12.5 … 23.5 mA
Failure current "fail low"
<
2.3 mA
<
2.3 mA
Failure current "fail high"
>
23.5 mA
>
23.5 mA
A safe failure is present when the measuring system switches
to the defined safe state or the fault mode without the process
demanding it.
If the internal diagnosis system detects a failure, the measuring
system goes into fault mode.
A dangerous undetected failure exists if the measuring system
switches neither to the defined safe condition nor to the failure
mode when the process requires it.
If the measuring system delivers output currents of "fail low" or
"
fail high", it can be assumed that there is a malfunction.
The processing unit must therefore interpret such currents as a
malfunction and output a suitable fault signal.
If this is not the case, the corresponding portions of the failure
rates must be assigned to the dangerous failures. The stated
values in chapter "Safety-relevant characteristics" can thus
worsen.
The processing unit must correspond to the SIL level of the
measurement chain.
If an SU 501 Ex is used for processing, the mode switch on the
sensor must be set to "max.".
If the demand rate is only once a year, then the measuring
system can be used as safety-relevant subsystem in "low
demand mode" (IEC 61508-4, 3.5.12).
Safe state
Fault description
Configuration of the
processing unit
Low demand mode
OPTISWITCH series 3000 • - two-wire
5
Functional safety
32745
-
EN
-
080414