Warning – Triangle Engineering of Arkansas VAB User Manual
Page 2
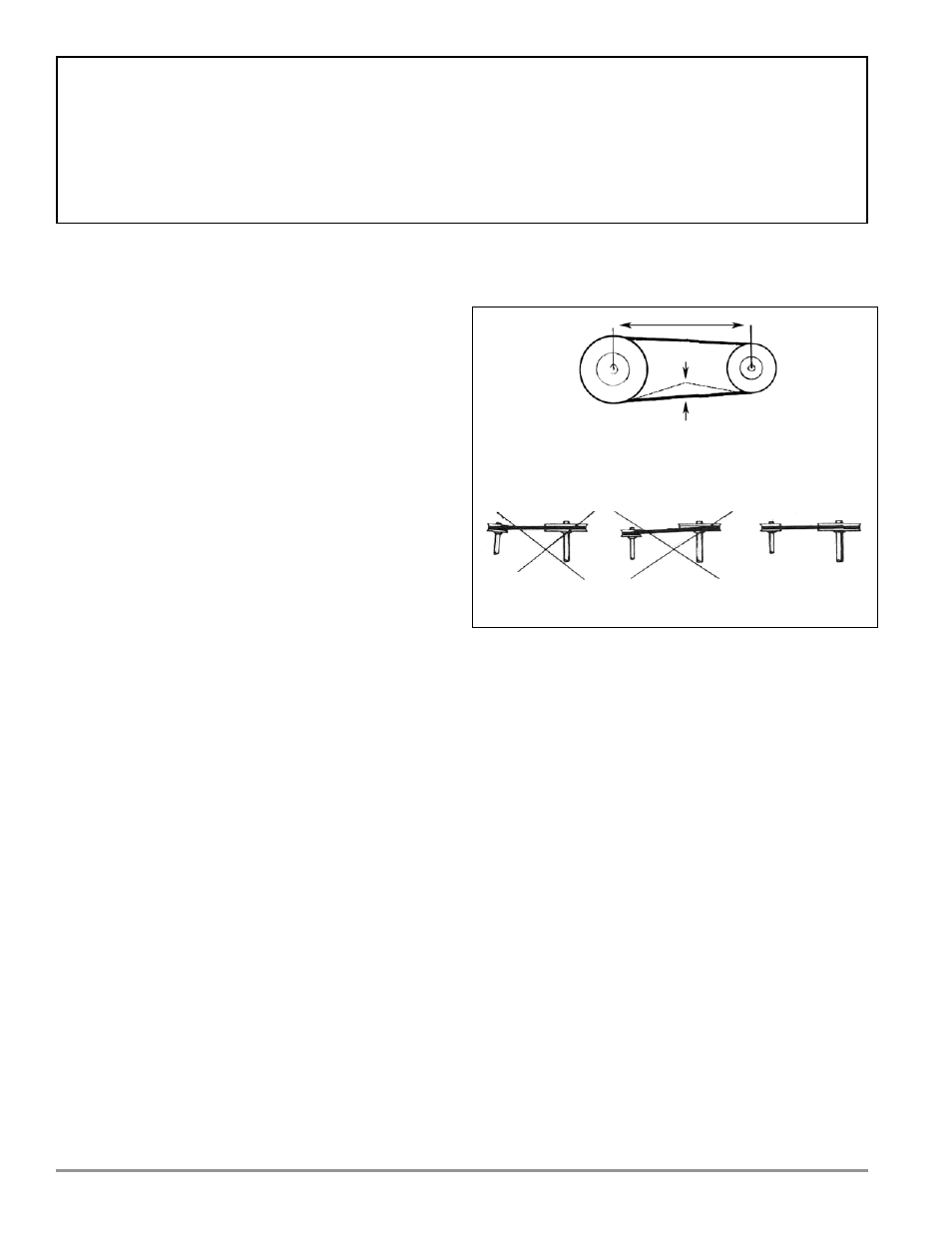
Before installing the ductwork, check all fasteners and
set screws for tightness. This is especially important for
bearings and propellers. Rotate the propeller by hand
to assure it turns freely and does not rub on the tubular
housing.
Direction of propeller rotation should be checked by
turning the unit on momentarily. Rotation should be in
the same direction as the rotation decal affixed to the
unit. To reverse rotation on three phase installations,
simply interchange any two of the three electrical leads.
For single phase installations, follow the wiring diagram
located on the motor.
ROUTINE MAINTENANCE
See WARNING above.
Once the fan has been put into operation, periodic
maintenance should be scheduled to preserve its
reliability and performance.
Items to be checked are:
1. Belts
2. Bearings
3. Fasteners and Set screws
4. Lubrication
5. Removal of dust and dirt
1. BELTS (BELT DRIVE)
Premature belt failures are most frequently caused
by improper belt tension (either too tight or too loose),
misaligned pulleys or prying belts on or off pulleys.
The proper tension for operating a V-belt is the lowest
tension at which the belts will not slip at peak load
conditions. For initial tensioning, the proper belt deflection
is 1/64" for each inch of belt span, measured half way
between pulley centers. For example, a belt span of 32
inches should have 32/64 or 1/2 inch of deflection using
moderate thumb pressure at midpoint of the drive. Check
belt tension after the first 24 hours of operation, after 100
hours of operation and periodically thereafter. Belt tension
can be adjusted by loosening the motor plate bolts and
adjusting the jack screws as required.
It is very important that the drive pulleys remain
in proper alignment after adjustments are made.
Misalignment of pulleys will result in premature belt wear,
noise and loss of fan efficiency.
2. BEARINGS (BELT DRIVE)
The pillow block ball bearings installed on model TAB
fans are grease lubricated, self aligning and selected
for a minimum average life in excess of 200,000 hours.
However, bearings are one of the most critical moving
parts of a fan and should be inspected at regular
maintenance intervals. Locking collars, set screws and
fasteners attaching the bearings to the fan, in addition to
general condition of the bearings, should be checked
3. FASTENERS AND SET SCREWS
Fan vibration has a tendency to loosen mechanical
fasteners. Periodic inspection should include checking all
fasteners and set screws for tightness.
WARNING
DISCONNECT AND SECURE TO THE “OFF" POSITION ALL
ELECTRICAL POWER TO THE FAN PRIOR TO INSPECTION OR
SERVICING. FAILURE TO COMPLY WITH THIS SAFETY
PRECAUTION COULD RESULT IN SERIOUS INJURY OR DEATH.
*Deflection height = 1/64" per inch of span
BELT AND PULLEY ALIGNMENT
WRONG WRONG CORRECT