SANDPIPER MSA25 User Manual
Page 7
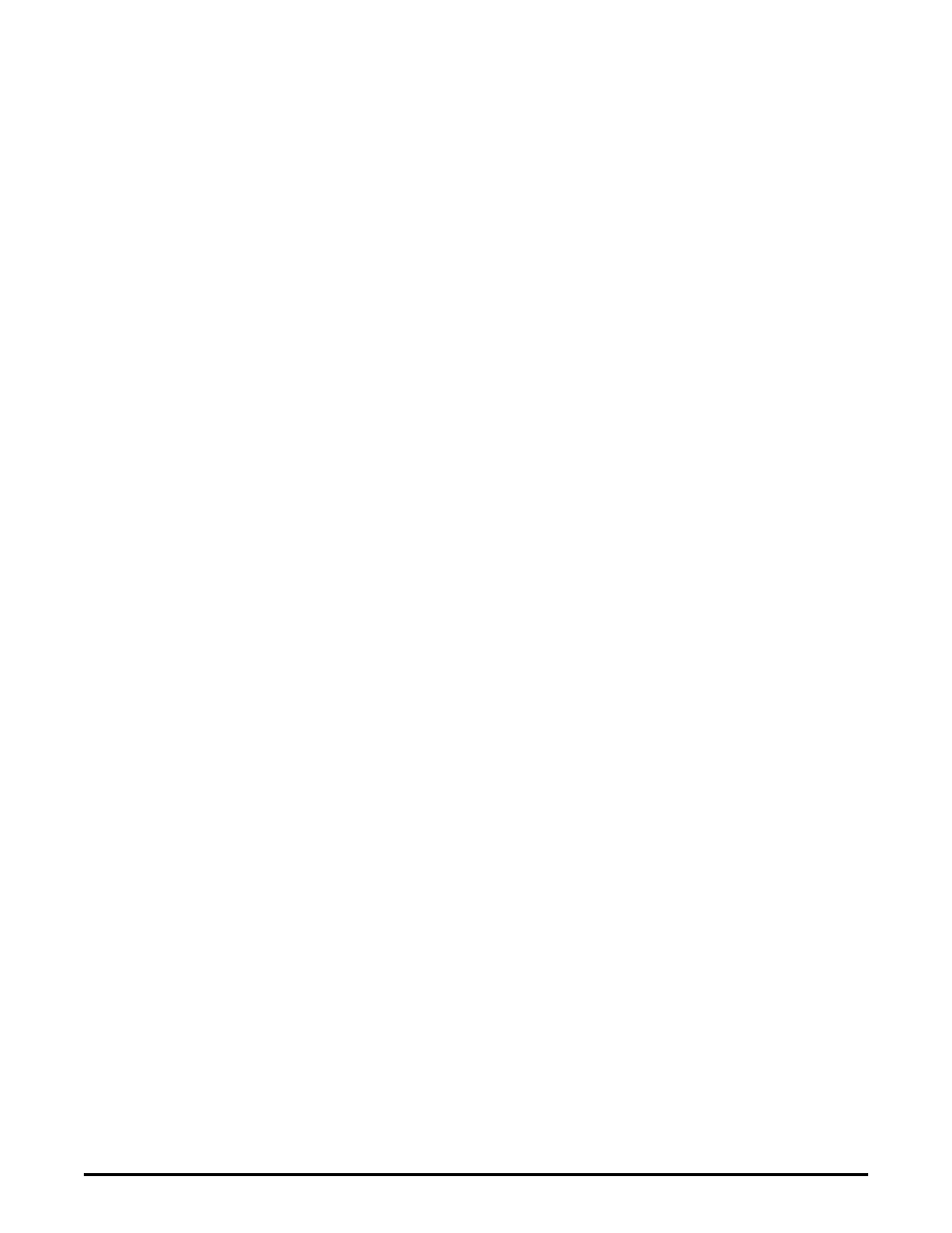
Model MSA1, MSA25 Type 4 Page 6
msa1dl4sm-rev0711
capscrew of the opposite side to keep the rod from rotating. If the opposite chamber
is assembled, the rod need not be held.
When reassembling the outer chambers and the manifold, the bolts securing
the manifold flange to the chamber should be snugged prior to tightening the
chamber bolts.
The sleeve and spool set is located in the valve body, which is held onto the
intermediate bracket by four (4) capscrews. Loosening the four (4) hex head capscrews
allows the valve body to come out of place.
Once the valve body is off the pump, remove the retaining ring holding the endcap
on the body to inspect the spool and sleeve set. The spool of the air distribution valve
is closely sized to the sleeve. The spool must slide freely in the sleeve. Accumulation
of dirt and contaminants may prevent the spool from moving freely. It may stick in a
position that prevents the pump from cycling.
Clean all parts before reassembly. Use a safety solvent and air oil to keep the
parts from oxidizing. Any nicks on the spool should be removed with a fine stone or
crocus cloth.
When removing the stainless steel sleeve, carefully press it out of the body,
preferably using an arbor press. Reinstall it into the body until it bottoms out against
the opposite end cap. Use new o-rings when reinstalling and apply a light coating of
grease or o-ring lube before placing in the valve body.
Reinstall the spring, end cap, and new retaining rings. Tighten the four capscrews
to eliminate air leakage. Tighten at 150 in/lbs (16.9 newton meters). Reinstall the
body on the intermediate bracket with new gaskets.
A NOTE ABOUT AIR VALVE LUBRICATION
The MARATHON pump’s pilot and main air valve assemblies are designed to
operate WITHOUT lubrication. This is the preferred mode of operation. There may be
instances of personal preference, or poor quality air supplies when lubrication of the
compressed air supply is required. The pump air system will operate with properly
lubricated compressed air supplies. Proper lubrication of the compressed air sup-
ply would entail the use of an air line lubricator (available from Warren Rupp) set to
deliver one drop of 10 wt., non-detergent oil for every 20 SCFM of air the pump con-
sumed at its point of operation. Consult the pump’s published Performance Curve to
determine this.
It is important to remember to inspect the sleeve and spool set routinely. It should
move back and forth freely. This is most important when the air supply is lubricated.
If a lubricator is used, oil accumulation will, over time, collect any debris from the
compressed air. This can prevent the pump from operating properly.
Water in the compressed air supply can create problems such as icing or freezing
of the exhaust air causing the pump to cycle erratically, or stop operating. This can
be addressed by using a point of use air dryer to supplement a plant’s air drying
equipment. This device will remove excess water from the compressed air supply and
alleviate the icing or freezing problem.
ESADS: Externally Serviceable Air Distribution System
Please refer to the exploded view drawing and parts list in the Service Manual
supplied with your pump. If you need replacement of additional copies, contact your
local Warren Rupp Distributor, or the Warren Rupp factory Literature Department at
the number shown below. To receive the correct manual, you must specify the MODEL
and TYPE information found on the name plate of the pump.
Models with 1" suction/discharge or larger and METAL center sections
The main air valve sleeve and spool set is located in the valve body mounted on
the pump with four hex head capscrews. The valve body assembly is removed from
the pump by removing these four hex head capscrews.
With the valve body assembly off the pump, access to the sleeve and spool set is
made by removing four hex head capscrews (each end) on the end caps of the valve
body assembly. With the end caps removed, slide the spool back and forth in the
sleeve. The spool is closely sized to the sleeve and must move freely to allow for proper
pump operation. An accumulation of oil, dirt or other contaminants from the pump’s air
supply, or from a failed diaphragm, may prevent the spool from moving freely. This
can cause the spool to stick in a position that prevents the pump from operating. If
this is the case, the sleeve and spool set should be removed from the valve body for
cleaning and further inspection.