Filling of driver chamber with liquid, Troubleshooting – SANDPIPER ST25 User Manual
Page 10
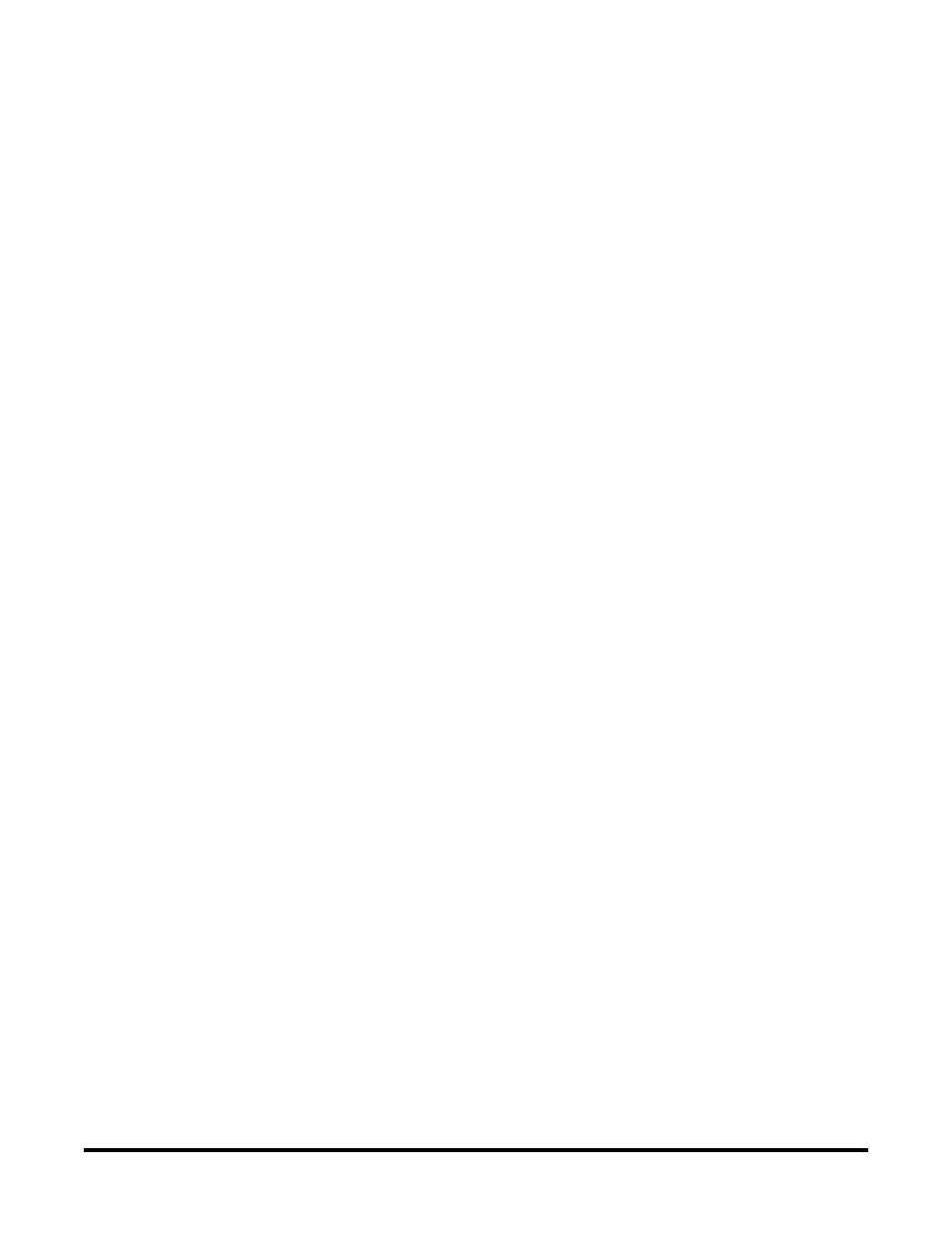
st1dl5sm-rev0614
Models ST1 & ST25 Page 8
FILLING OF DRIVER CHAMBER WITH LIQUID
The driver chambers are filled at the factory with distilled water.
If you need to substitute another liquid to prevent system contamination, first consult
the factory for chemical compatibility with pump construction.
Follow the steps listed below to replace the liquid in the pump after disassembly or
liquid loss:
1. Filling is accomplished through the pipe plugs at the top of the liquid chamber.
Drain ports are at the bottom of the liquid chamber.
2. After the driver fluid has been emptied from the pump, the driver diaphragms will
naturally come to center.
3. Remove the entire manifold assembly exposing the ports in the outer diaphragm
chambers.
4. Fill either side with 722 MI. or 24.6 fluid oz. by volume with the driver liquid. It is
imperative that the driver liquid chambers be filled with the correct amount of driver liquid
as too little or too much will cause premature diaphragm failure and erratic pumping.
5. After filling with the proper amount of liquid, if the liquid does not come to the top
of the fill hole, pressure should be applied to the PTFE diaphragm with a blunt tool
through the material flow port in the outer chamber until the liquid comes to the top. If
the main air valve body and pilot valve are removed, the diaphragm rod will be visible in
the intermediate bracket. The hole in the diaphragm rod will assist manual movement.
Use a long taper punch to move the diaphragm rod.
6. When the driver fluid rises to the top of the fill plug hole, apply pipe dope to the
pipe plug, and thread it into the chamber plug hole. (Do not use PTFE tape.) Keep
pressure on the PTFE diaphragm until the pipe plug is tight to prevent air from drawing
back into the chamber.
7. Repeat the filling procedure for opposite side.
TROUBLESHOOTING
1. Pump will not cycle
A. Check to make sure the unit has enough pressure to operate and that the air inlet
valve is open.
B. Check the discharge line to insure that the discharge line is neither closed nor blocked.
C. If the spool in the air distribution valve is not shifting, check the main spool. It must
slide freely.
D. Excessive air leakage in the pump can prevent cycling. This condition will be evident.
Air leakage into the discharge line indicates a ruptured diaphragm. Air leakage from the
exhaust port indicates leakage in the air distribution valve. See further service instructions.
E. Blockage in the liquid chamber can impede movement of diaphragm.
2. Pump cycles but will not pump
A. Suction side of pump pulling in air. Check the suction line for air leaks and be sure
that the end of the suction line is submerged. Check flange bolting. Check valve flanges
and manifold to chamber flange joints.
B. Make certain the suction line or strainer is not plugged. Restriction at the suction is
indicated by a high vacuum reading when a vacuum gauge is installed in the suction line.
C. Check valves may not be seating properly. To check, remove the suction line and
cover the suction port with your hand. If the unit does not pull a good suction (vacuum),
the check valves should be inspected for proper seating.
D. Static suction lift may be too high. Priming can be improved by elevating the suction
and discharge lines higher than the check valves and pouring liquid into the unit through
the suction inlet. When priming at high suction lifts or with long suction lines operate the
pump at maximum cycle rate.
E. Incorrect driver fluid level or unpurged air in the chamber can cause poor
performance.
3. Low performance
A. Capacity is reduced as the discharge pressure increases, as indicated on the
performance curve. Performance capability varies with available inlet air supply. Check
air pressure at the pump inlet when the pump is operating to make certain that adequate
air supply is maintained.
B. Check vacuum at the pump suction. Capacity is reduced as vacuum increases.
Reduced flow rate due to starved suction will be evident when cycle rate can be varied
without change in capacity. This condition will be more prevalent when pumping viscous
liquids. When pumping thick, heavy materials the suction line must be kept as large in
diameter and as short as possible, to keep suction loss minimal.