Vf series, General pump – General Pump VF Owner Manual User Manual
Page 8
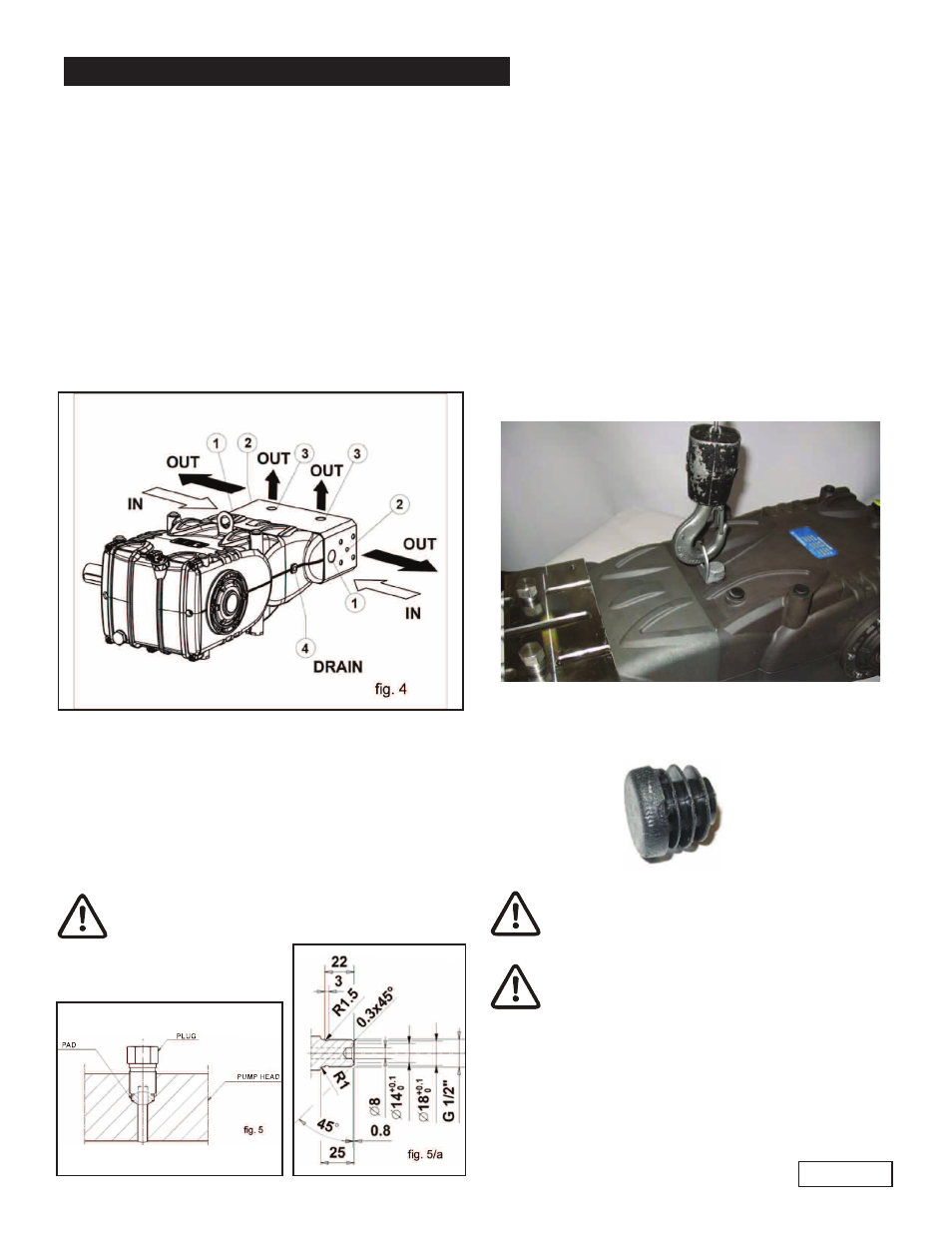
GENERAL PUMP
A member of the Interpump Group
VF SERIES
Page 8
9. PUMP INSTALLATION
9.1 Installation
The pump must be installed in a horizontal position using
the correct threaded feet M16 x 1.5; fasten the screws with
a torque value of 155 ft. lbs. (210 Nm). The base must be
perfectly flat and sufficiently rigid in order to avoid bending
and misalignments on the pump/transmission coupling axis
due to the torque applied during operation. The unit must
not be rigidly fixed to the pavement, but requires the use of
anti-vibration elements. For special applications, please
contact the Customer Service Department.
The pump is equipped with a lifting bracket to facilitate
installation as shown in the following figure.
8. PORTS AND CONNECTIONS
VF Series pumps (see fig. 4) are provided with:
1. 2 inlet ports “IN”, 3/4” Gas. The line can be connected
to either of the two inlet ports; the ones not being
used must be hermetically sealed.
2. 2 outlet ports “OUT”, Ø 8 mm
3. 2 auxiliary ports, 1/2” gas; they can be used for the
pressure gauge and the safety valve.
4. 1 drain port “DRAIN” supplied with an adjustable 90
0
rapid fitting for Ø 10 mm polyimide hoses; it is
needed to recover the fluid drained from the packing
cooling circuit, and must be connected to the outlet
port being careful to avoid counter-pressure.
8.1 Conic sealing pads
The VF pumps are equipped with 4 conic steel pads to be
used in correspondence of the pump’s delivery ports (fig. 5)
or in the optional fitting flanges. Their function is to guaran-
tee the sealing of the connection. The seat of the pump’s
delivery port is already machined in order to hold the conic
pad; if necessary, the connections for the delivery fitting or
the closing plug must be correctly machined as indicated in
fig. 5/a.
At each disassembly, the conic pad must be
replaced.
In case of disassembly, to avoid letting dirt inside the front
part of the crankcase, close the threaded hole with the
appropriate cap, supplied.
Replace the crankcase cap with the oil dipstick
and check oil level. The oil dipstick must always
be accessible, even when the unit is assembled.
The pump’s shaft (PTO) must not be rigidly
connected to the motor unit. The following
transmission
types
are
suggested:
• hydraulic by means of flange; for correct
application, please contact the Customer
Service Department
• Belts
• Cardan Joint (please respect the maximum
working angles indicated by the manufacturer)
• Flexible joint
Ref 300662 Rev.C
06-12