SPP Pumps Eurostream User Manual
Page 8
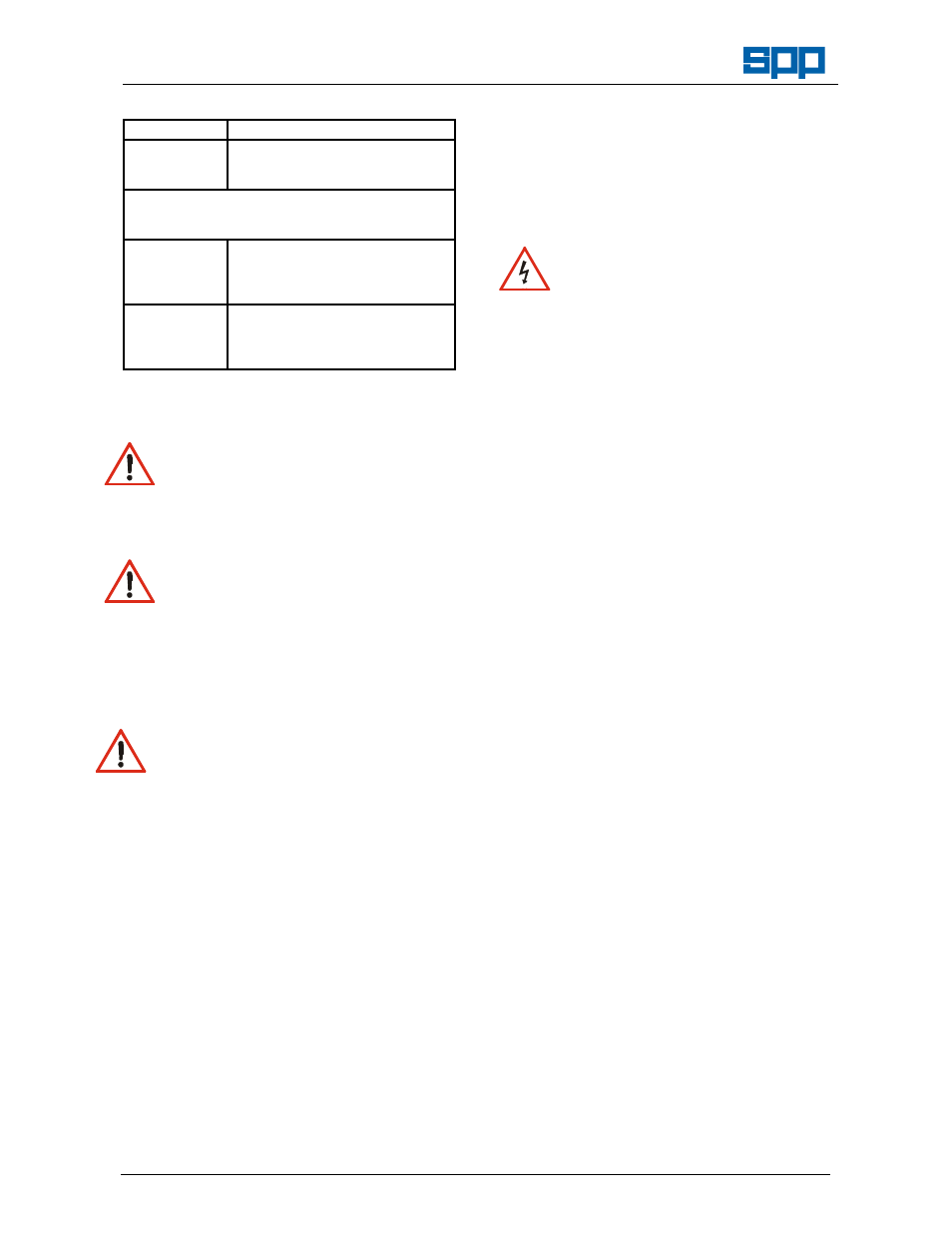
Manual No/Rev
W22-001E / 9
Operators Instructions for
Eurostream Centrifugal Pumps
Our policy is one of continuous improvement and we reserve the right to alter specifications at any time
Page 8 of 20
Recommended Maintenance Schedule
Period:
Maintenance Required:
Weekly
Carry out periodic checks as shown
in Section 5.3 and take corrective
action as shown in Section 7.
Where specified in the motor manufacturer's
instructions at the recommended intervals, check and
lubricate the motor bearings.
Half Yearly or
After 5000
Hours
Running
Check and tighten all holding down
bolts if found loose, refer to Section
9 for recommended bolt tightening
torques.
Each Year
Assess the performance of the
pump against the duty
specifications and take corrective
action as shown in Section 7
The following hazards may arise during
maintenance work:
Fluid Pressure Jet Hazards
Check and ensure that the pump
operates at below the Maximum
Working Pressure specified in the manual or
on the pump nameplate and before
maintenance, ensure that the pump is
drained down.
Hazardous Materials
Wear a suitable mask or respirator
when working with packing or gasket
components that contain fibrous material, as
these can be hazardous when the fibrous
dust is inhaled. Be cautious, if other
supplier's
components
have
been
substituted for genuine SPP Pumps parts,
these may then contain hazardous materials.
Hazardous Gases, Mists, Sprays
and Leaks
Be aware of the hazards relating to the
pumped fluid, especially the danger from
inhalation of noxious and toxic gases, skin
and eye contact or penetration. Obtain and
understand
the
hazardous
substance
(COSHH) data sheets relating to the
pumped fluid and note the recommended
emergency and first aid procedures.
BEFORE
ATTEMPTING
ANY
MAINTENANCE
ON
A
PUMP,
PARTICULARLY
IF
IT
HAS
BEEN
HANDLING ANY FORM OF HAZARDOUS
LIQUID, ENSURE THAT THE UNIT IS
SAFE TO WORK ON. THE PUMP MUST
BE FLUSHED THOROUGHLY WITH A
SUITABLE CLEANSER TO PURGE AWAY
ANY OF THE PRODUCT LEFT IN THE
PUMP COMPONENTS. THIS SHOULD BE
CARRIED
OUT
BY
THE
PLANT
OPERATOR AND A CERTIFICATE OF
CLEANLINESS
OBTAINED
BEFORE
STARTING WORK. TO AVOID ANY RISK
TO HEALTH IT IS ALSO ADVISABLE TO
WEAR
PROTECTIVE
CLOTHING
AS
RECOMMENDED BY THE SITE SAFETY
OFFICER,
ESPECIALLY
WHEN
REMOVING OLD SEALS OR GASKETS
THAT MAY BE CONTAMINATED.
6.2
Preparation for Maintenance
Electric Shock & Accidental
Starting
Hazard
ISOLATE
the
equipment
before
any
maintenance work is done. Switch off the
mains supply, remove fuses, apply lockouts
where applicable and affix suitable isolation
warning signs to prevent inadvertent re-
connection.
In order to avoid the possibility of
maintenance personnel inhaling dangerous
fumes or vapours. It is recommended that
maintenance work be carried out away from
the pump location by removal of the motor
and
shaft
assembly
to
a
suitable
maintenance area.
No special tools are required for dismantling
and re-assembling, however, it is important
to ensure the suitable lifting equipment is
available and that the work is carried out in a
clean area.
6.3
Maintenance of Mechanical Seals
Generally there are is no maintenance
required on mechanical seals, they should
be replaced if leakage occurs.
6.4
Dismantling and re-assembly:
6.4.1 General
If the pump is maintained and serviced
regularly, breakdowns that require the pump
to be dismantled should not occur.
If a fault occurs, the cause should be
identified before dismantling. Refer to
Section 7 - Faults and Remedial Action.
Refer to Section 8 - for the Pump Section
Drawing for your pump.
When the pump is being dismantled, parts
must be handled with care, to avoid damage
by dropping and hammer blows.
Where new joints are made, correct gasket
thickness must be maintained.
After re-assembly the rotor must turn easily
by hand, otherwise premature pump failure
may occur.