Testing the automated system, Manual operation, Restoring normal operation – Controlled Products Systems Group 10978021 User Manual
Page 5: Special applications, Maintenance, Repairs
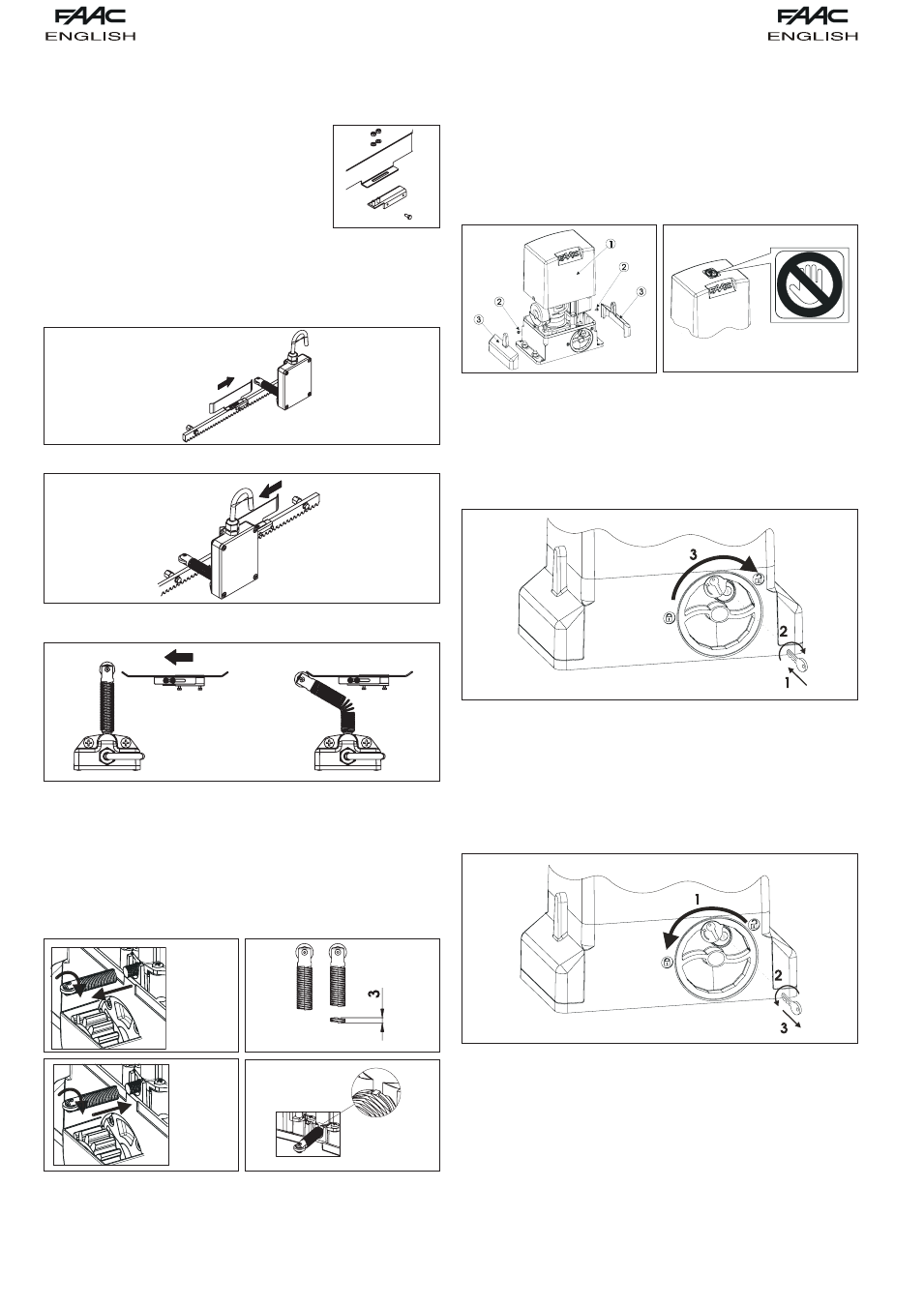
10
Fig.20
Fig.22
Fig.23
Fig.24
Fig.25
Fig.21
Fig.26
Fig.27
Fig.28
Fig.29
6) Repeat the operations at points 4 and 5 for the closing limit switch, Fig. 20.
Values are expressed in mm
Fig.19
Fig.18
6.2. Positioning the limit switches
The operator has a mechanical travel stop with spring-lever, which commands
gate movement to stop when a profiled steel plate, secured on the top of the
rack, activates the spring until the microswitch is tripped. The plate support can be
fitted to all racks with max. width of 13 mm.
Procedure for correct positioning of the two travel stop
plates supplied:
1) Fit and secure the 2 profiled steel plates on the 2 U-
supports, using the supplied nuts and washers, as shown in
figure 18.
2) Prepare the operator for manual operation as
described in paragraph 8.
3) Power up the system.
4) Securing the opening limit switch: manually take the
gate to opening position, leaving 20 mm from the
mechanical travel stop.
5) Allow the plate to slide over the rack in opening direction (Fig.19). As soon as
the opening limit switch LED on the control board goes off, take the plate
forward by about 20÷30 mm and secure it provisionally on the rack, using the
supplied screws.
Important:
a) The plate must activate the limit-switch on the profiled part as shown in figure
21.
b) If the wheel and the travel stop plate are too close, it may be necessary to
shorten the limit-switch spring by a couple of turns. Procedure for shortening the
spring:
- To remove the spring, turn it clockwise. This operation requires some force.
- Shorten the spring as shown in Fig. 23: two turns correspond to about 3 mm.
- Fit the spring turning it clockwise, Fig. 24, until the stop is reached; see Fig. 25.
- Once the spring is back in place, ensure the wheel is horizontal. A wrong wheel
orientation may jeopardise the operation of the limit switches.
8) Re-lock the system (see paragraph 9).
Important: Before sending a pulse, make sure that the gate cannot be moved
manually.
9) Command a complete gate cycle to check if the limit switch is tripped
correctly.
Warning: To avoid damaging the operator and/or interrupting operation of
the automated system, allow a space of about 20 mm from the mechanical
travel stops.
10) Appropriately adjust the position of the travel stop plates and definitively
secure them on the rack.
7. TESTING THE AUTOMATED SYSTEM
After installing the operator, carefully check operating efficiency of all accessories
and safety devices connected to it.
Return the board support to its original position. Fit the cover, Fig. 25 ref. 1, and tighten
the two side screws provided (Fig. 26 ref 2), and snap-fit the side panels (Fig. 26 ref.3).
Apply the danger sticker on the top of the cover (Fig. 27).
Hand the “User’s Guide” to the Customer and explain correct operation and use
of the gearmotor, indicating the potentially dangerous areas of the automated
system.
8. MANUAL OPERATION
Warning: Cut power to the system to prevent an involuntary pulse from
activating the gate during the release manoeuvre.
To release the operator proceed as follows:
1) Insert the key provided and turn it clockwise as shown in Fig. 28 ref. 1 and 2.
2) Turn the release system clockwise, until the mechanical stop is reached, Fig. 28
ref. 3.
3) Open and close the gate manually.
9. RESTORING NORMAL OPERATION
Warning: Cut power to the system to prevent an involuntary pulse from
activating the gate during the manoeuvre for restoring normal operation.
To restore normal operation proceed as follows:
1) Turn the release system anti-clockwise, until its stop is reached, Fig. 29 ref. 1.
2) Turn the key anti-clockwise and remove it from the lock, Fig. 29 ref. 2 and 3.
3) Move the gate until the release system meshes (corresponds to gate locking)
4) Power up the system.
10. SPECIAL APPLICATIONS
There are no special applications.
11. MAINTENANCE
Check the operational efficiency of the system at least once every 6 months,
especially as regards the efficiency of the safety and release devices (including
operator thrust force).
12. REPAIRS
For any repairs, contact the authorised Repair Centres.