English – Controlled Products Systems Group 1049062 User Manual
Page 15
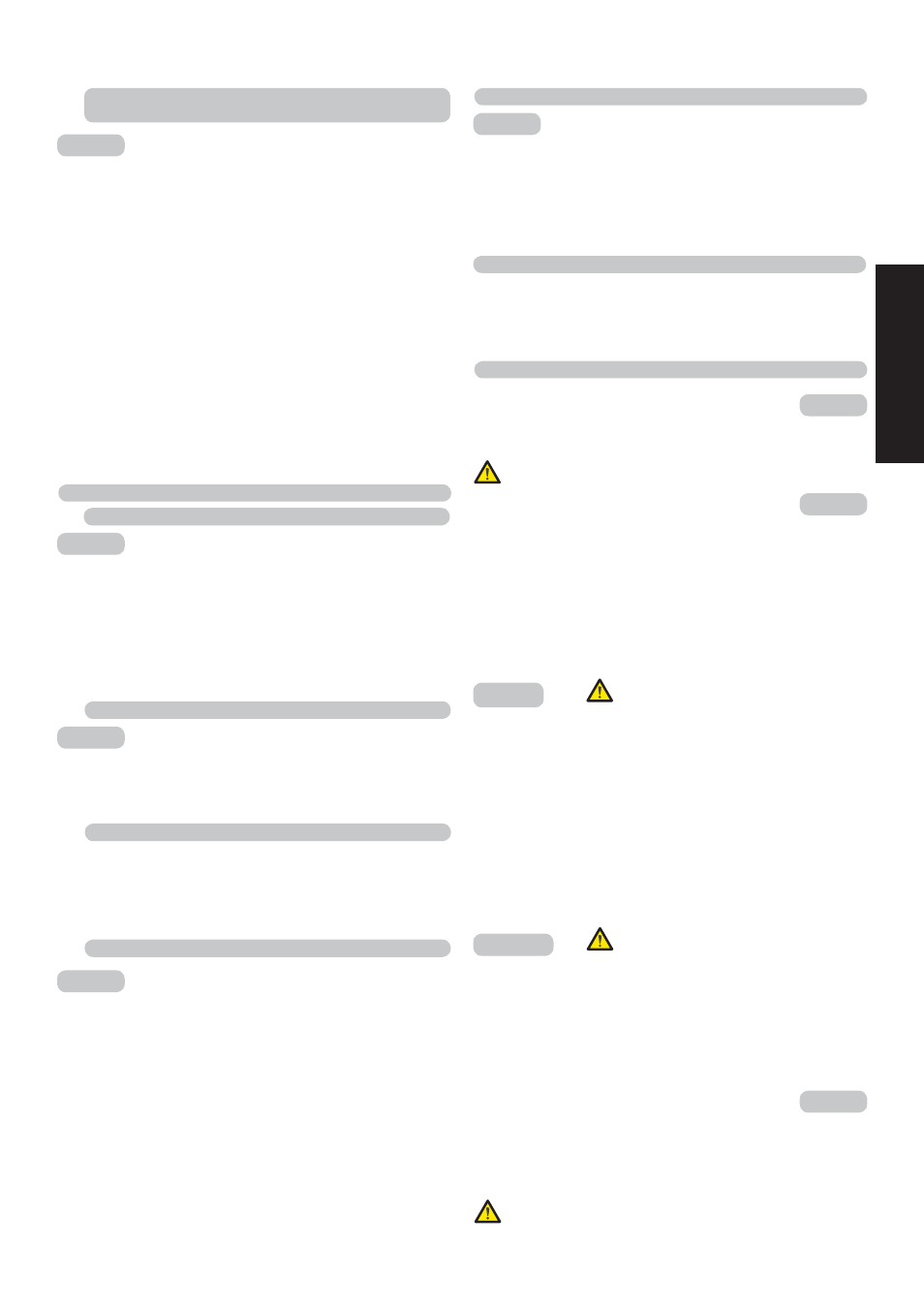
5
ENGLISH
Procedure for converting a right-hand version to
left-hand:
Release the operator.
Loosen the connection (fig.9 ref.A).
Provisionally remove the piston securing screw (fig.9 ref.B)
and the seeger ring (fig.9 ref.C).
Rotate the rocker.
Position the piston from the left side and secure it with the screw
(fig.9 ref.D) and the seeger (fig.9 rif.E) you had removed.
Tighten the connection (fig.9 ref.F).
Re-lock the operator.
Dismantle the container of the control unit and re-install it
on the left of the hood, using the existing holes.
Change over the connectors of the travel-limit sensors (J6
and J9 on the 596/615BPR board).
5.5 TRANSFORMATION FROM RIGHT TO LEFT VERSION
To set the hydraulic system controlling transmitted power,
turn the two by-pass screws (fig.10).
The red screw controls closing movement torque.
The green screw controls opening movement torque.
To increase torque, turn the screws clockwise.
To reduce torque, turn the screws anti-clockwise.
6 START-UP
6.1 ADJUSTING THE TRANSMITTED TORQUE
The point where the automated system begins to make
the slow-down movement can be modified, by moving the
magnetic cylinder inside the seat located on the two arms
of the rocker in the motion unit (fig.11 - ref.2).
Adjust the position of the beam to maximum closing and
opening positions, using the travel limit mechanical stops
as shown in fig.11.ref.1.
To prevent an involuntary impulse from activating the barrier
during the manoeuvre, before restoring normal operation,
switch off power to the system, and turn the triangular key
clockwise until it stops, and then remove it.
If the barrier has to be moved manually due to a power cut
or fault of the automated system, use the release device
as follows.
- Fit the standard triangular key (Fig.13) in the lock and turn
it anti-clockwise through 1 turn.
- Open and close the barrier manually.
After installation, apply the danger warning sticker on the top
of the upright (Fig. 12).
Check operating efficiency of the automated system and all
accessories connected to it.
Hand the “User’s Manual” to the Client, explain correct
operation and use of the barrier, and indicate the potentially
dangerous areas of the automated system.
6.2 ADJUSTING THE MECHANICAL TRAVEL LIMITS
6.3 ADJUSTING THE MAGNETIC TRAVEL LIMITS
6.4 AUTOMATED SYSTEM TEST
7 MANUAL MODE OPERATION
8 RESTORING NORMAL OPERATION MODE
SKIRT KIT
The skirt kit increases visibility of the beam.
It is available in lengths from 2 m to 3 m.
If a skirt kit is installed, the balancing spring must be
adapted.
9 AVAILABLE ACCESSORIES
POSITIONING THE FORK SUPPORT FOUNDATION PLATE WITH
RECTANGULAR BEAM
To position the foundation plate of the fork support, refer to
fig.16 where:
P1 = barrier foundation plate
P2 = fork support foundation plate
L = beam length (in mm)
A = L - 195 (in mm)
FORK SUPPORT
The fork has two functions:
- it prevents the beam, when closed, from bending or splitting
if its end is stressed by extraneous forces.
- it allows the beam to rest when closed and thus prevents
the profile bending downward.
Dimensions are in mm.
Fig. 16
Fig. 16A
ARTICULATION KIT
The articulation kit makes it possible to articulate a rigid
beam to a maximum ceiling height of 3 m. (see specific
instructions).
If the articulated kit is installed, the balancing spring
must be adapted.
POSITIONING THE FORK SUPPORT FOUNDATION PLATE WITH
ROUND BEAM
To position the foundation plate of the fork support, refer to
fig.16A where:
P1 = barrier foundation plate
P2 = fork support foundation plate
L = beam length (in mm)
A = L - 375 (in mm)
Dimensions are in mm.
Fig. 10
Fig. 11
Fig. 12
Fig. 13
Fig. 14
Fig. 15
Fig. 17
Fig. 9