English – Controlled Products Systems Group 1049062 User Manual
Page 14
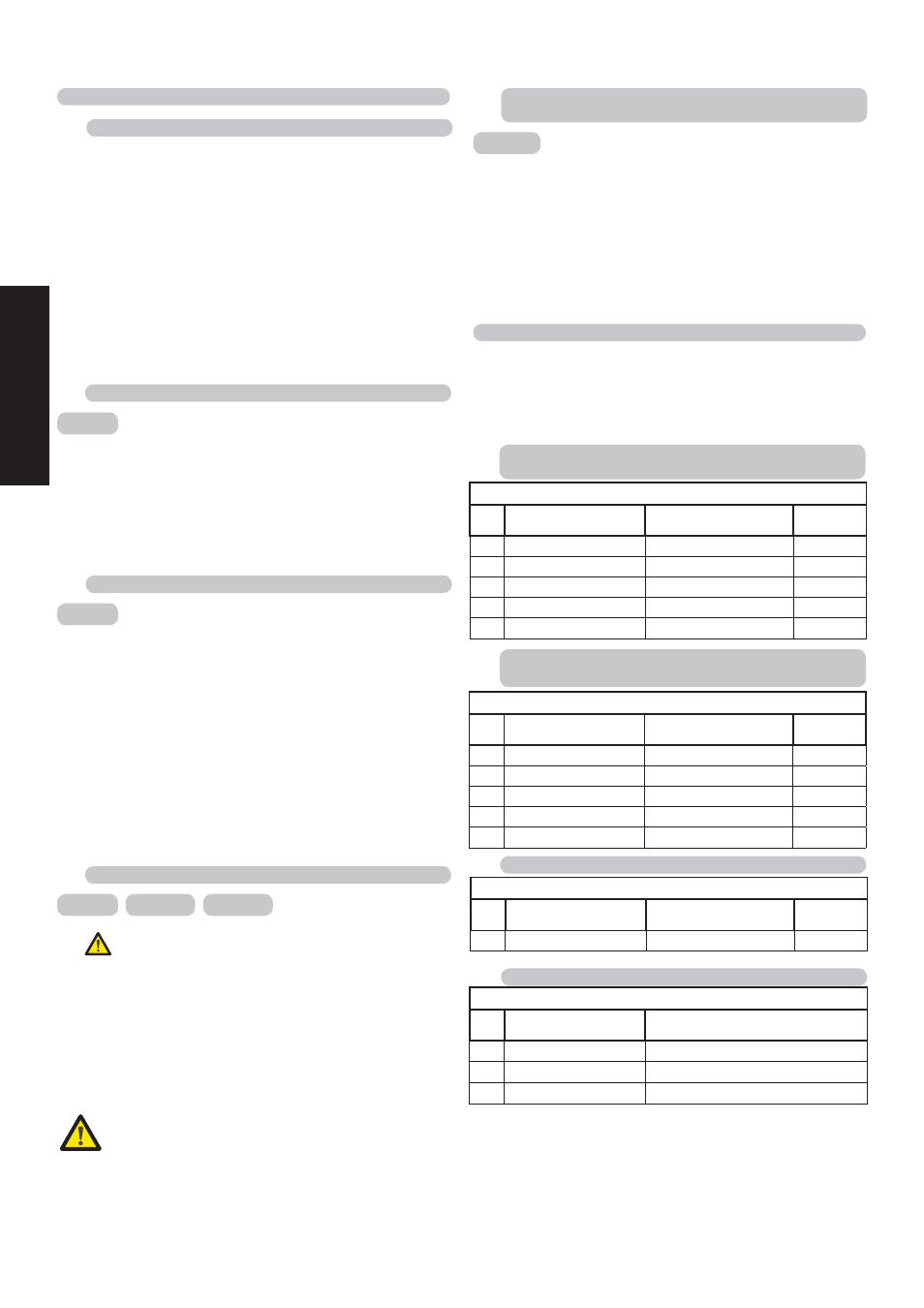
4
ENGLISH
To ensure safety and an efficiently operating automated
system, make sure the following conditions are observed:
•
When moving, the beam must not, on any account,
meet any obstacles or overhead power cables.
•
The soil must permit sufficient stability for the foundation
plinth.
•
There must be no pipes or electrical cables in the plinth
excavation area.
•
If the barrier body is exposed to passing vehicles, install,
if possible, adequate means of protection against
accidental impact.
4.1 PRELIMINARY CHECKS
4 INSTALLING THE AUTOMATED SYSTEM
4.2 MASONRY FOR FOUNDATION PLATE
4.3 INSTALLING THE UPRIGHT
4.4 INSTALLING THE BEAM
The 615BPR automated system is always supplied
in the right-hand version – for left-hand installation,
see chapter 5.5.
1) Make sure that the rod of the piston secured to the rocker
is completely extended (corresponding to the beam’s
vertical position).
2) Remove and store the breather screw as shown in fig.6
1) Remove the cover, unscrewing the screws securing it to
the upright.
2) Using the four nuts and washers supplied, secure the
upright on the foundation plate as shown in fig.5
Remember that the hatch of the upright should normally
face the building.
1) Check if the balancing spring matches the type of beam
installed: see chapter 5.
2) While keeping the beam in vertical position, assemble
the tie rod and spring as shown in fig.8
3) Release the operator (see chapter 7) and position the
beam at 45°, then adjust the tie-rod and set the spring until
the weight of the beam is balanced in that position.
4) Restore normal operation as described in chapter 7.
4.5 INSTALLING AND ADJUSTING THE BALANCING
SPRING
1) Make a foundation plate as shown in fig.4 (referred to
clayey soil)
2) Wall the foundation plate as shown in fig.4, supplying
one or more sheaths for routing electrical cables. Using a
spirit level, check if the plate is perfectly level. Wait for the
cement to set.
IMPORTANT: moderately tighten the pocket securing screw
(max 30Nm)
The 615 BPR automated system requires a balancing spring
for the beam, which must be ordered separately. The spring
varies according to length and type of beam (rigid, skirt or
articulated).
Consult the tables below to see if the spring matches.
5 BALANCING SPRINGS
5.1 SPRINGS FOR RECTANGULAR BEAMS WITH SKIRT
BALANCING SPRING
Ø
rectangular
beam
beam
with skirt
code
5,5
1315 – 2315
1315 - 2315
721008
6,0
2316 – 2815
2316 – 2815
721005
7,0
2816 – 3815
721006
7,5
2816 – 3815
721007
8,0
3816 – 4815
721018
5.2 SPRINGS FOR RECTANGULAR BEAMS WITH FOOT
AND WITH SKIRT AND FOOT
BALANCING SPRING
Ø
beam
with foot
beam with skirt
and foot
code
5,5
1315 – 1815
1315 - 1815
721008
6,0
1816 – 2315
1816 – 2315
721005
7,0
2316 – 2815
721006
7,5
2316 – 3315
721007
8,0
2816 – 3815
721018
5.4 SPRINGS FOR ROUND BARS
BALANCING SPRING
Ø
round beam
code
5,5
1500 –3000
721008
6
3001 – 4000
721005
7,5
4001 – 5000
721006
5.3 FOR 615BPR RAPID
BALANCING SPRING
Ø
rectangular
beam
round
beam
code
5,5
1315 – 2315
1315 - 2315
721008
Fig. 4
Fig. 5
Fig. 6
Fig. 7a
Fig. 7b
Fig. 8