Climacool engineering guide specifications – ClimaCool FLEX SERIES 30, 50, 65 User Manual
Page 35
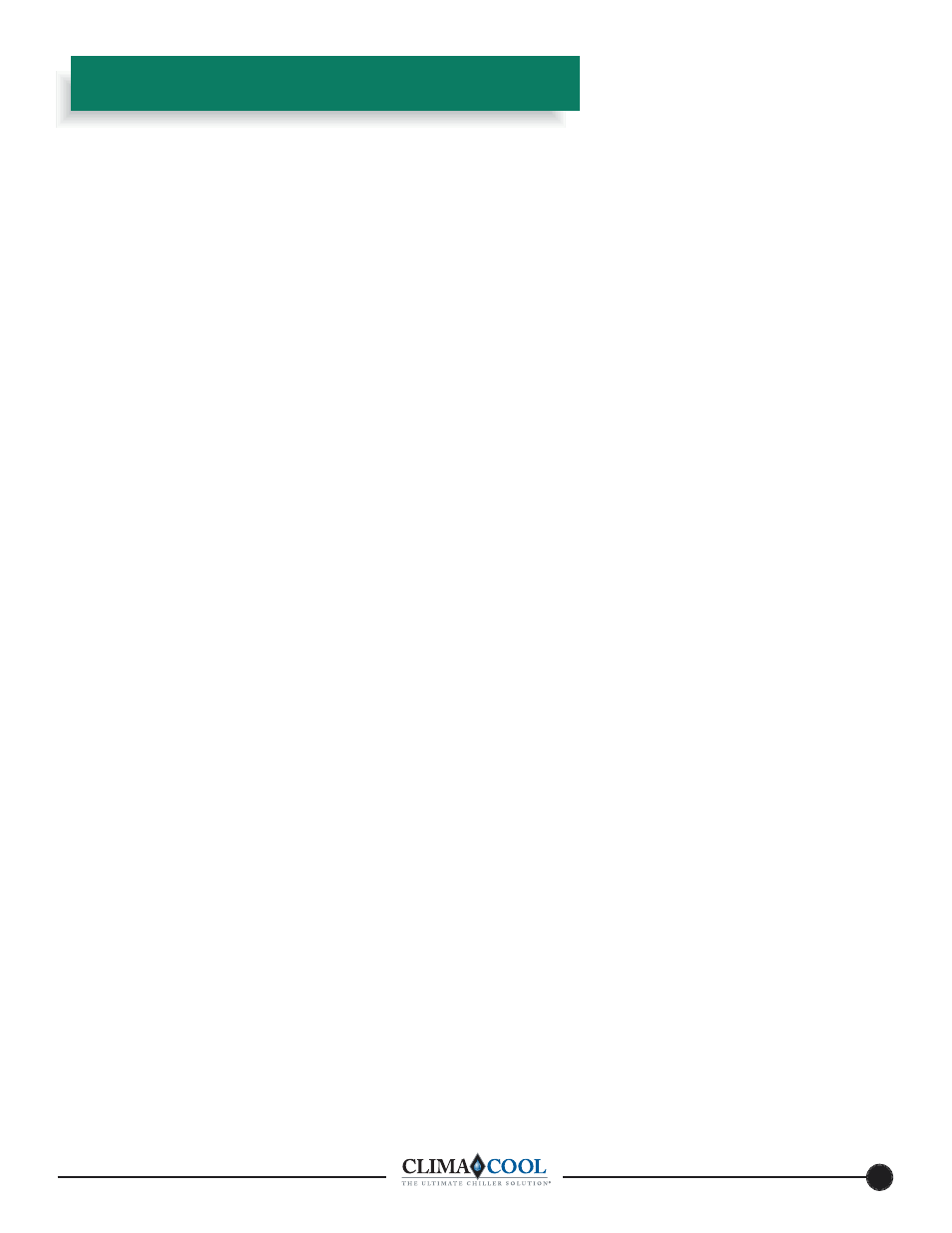
33
General
Furnish and install where shown on the plans water cooled
chiller modules having a total capacity of _______ tons when
cooling _______ GPM of chilled water/glycol solution from
______ °F to ______ °F. The glycol type for the chiller solu-
tion is (ethylene)/(propylene)/(water-only)
circle one, at a
glycol solution percentage of ______ %. The chiller capacity
rating shall be based on a ______ °F drop through the evapo-
rator with a chiller fl ow rate of ______ GPM/ton. The water
cooled chiller modules have a condenser fl ow rate of ______
GPM of water/glycol solution, with a temperature rise from
______ °F to ______ °F. The glycol type for the condenser
solution is (ethylene)/(propylene)/(water-only)
circle one, at
a glycol solution percentage of ______ %. The condenser rat-
ing shall be based on a ______ °F rise through the condenser
with a fl ow rate of ______ GPM/ton.
Modular Unit Design
The
FLEX Series modules must be designed to be refriger-
X
ant-convertible. The system is to be comprised of individual
e
b
t
s
u
m
s
e
l
u
d
o
M
.
n
g
i
s
e
d
n
i
r
a
l
u
d
o
m
e
r
a
t
a
h
t
s
n
o
it
c
e
s
r
e
ll
i
h
c
comprised of individual refrigerant circuits, compliant with
ASHRAE 90.1 operating on either R-22 or R-407C. Each
module is to be less than 34” in width to allow for maneuver-
ing through narrow openings. Each module’s length shall not
s
r
e
n
r
o
c
d
n
u
o
r
a
s
u
i
d
a
r
n
r
u
t
e
h
t
e
z
i
m
i
n
i
m
o
t
”
8
/
5
3
4
d
e
e
c
x
e
and obstacles encountered while moving and placing the unit
in the equipment room. Every module shall be capable of
y
ti
c
a
p
a
c
t
c
e
j
o
r
p
e
h
t
t
e
e
m
o
t
e
ti
s
n
o
g
n
il
p
u
o
c
d
l
e
fi
requirements.
Unit Construction
The frame design of each module shall utilize a painted,
heavy gauge, cold rolled steel frame for mounting the com-
pressors, condenser and evaporator. The frame must allow
for front or rear service access of the heat exchangers. The
e
p
i
p
l
e
e
t
s
n
o
b
r
a
c
”
6
d
e
d
l
e
w
g
n
i
s
u
d
e
t
c
u
r
t
s
n
o
c
e
b
ll
a
h
s
ti
n
u
c
i
n
o
r
d
y
h
e
h
t
o
t
y
ti
li
b
a
t
s
d
n
a
h
t
g
n
e
r
t
s
e
v
i
g
o
t
d
e
r
u
g
fi
n
o
c
section of the machine. Connection to the adjacent module
h
t
o
b
n
o
s
e
g
n
a
fl
d
e
t
a
r
I
S
P
5
8
2
g
n
i
s
u
y
b
d
e
h
s
il
p
m
o
c
c
a
s
i
condenser and chiller water circuits. The main headers must
y
ti
li
b
a
t
s
e
z
i
m
i
n
i
m
o
t
e
r
u
t
c
u
r
t
s
d
i
g
i
r
g
n
o
r
t
s
y
l
e
m
e
r
t
x
e
n
a
m
r
o
f
.
n
o
it
a
r
e
p
o
d
n
a
n
o
it
a
ll
a
t
s
n
i
g
n
i
r
u
d
s
m
e
l
b
o
r
p
Module Isolation and Room Footprint Requirements
All service and maintenance isolation valves must be con-
tained within the module footprint dimensions (34" wide x
43 5/8" deep). All water isolation valves must be recessed
within the 6" header condenser and evaporator water pip-
ClimaCool Engineering Guide Specifications
ing dimensions front and rear to prevent valve damage and
to minimize service clearances. All isolation valves must
be contained within the module dimensions. Valves which
extend beyond the main water header dimensions must be
approved by the project engineer if they cause an increase in
the equipment room footprint or add to the service clearance
dimensions. A motorized valve requires a 1 1/2" extension for
variable primary fl ow.
Electrical Cabinet Dimensional Parameters
The electrical cabinet construction must be recessed within
the module footprint dimensions (34" wide x 43 5/8" deep).
The electrical control cabinet must be recessed within the 6"
header fl anges of the condenser water piping, top and bottom
to prevent damage and to minimize service clearances. The
electrical cabinet construction must allow for electrical ac-
cess without removal of any sound attenuation covers.
Hydronic Design
Each chiller shall utilize a water header system of modules
bolted in series to maintain constant and full flow to each of
the heat exchangers while in operation. Each module shall be
factory supplied with isolation valves on all water circuits to
allow repair or maintenance of the heat exchangers without
interrupting operation of the entire system. The chilled water
piping on each module shall be pre-insulated at the factory
with 3/4” closed cell foam rubber. Insulation on the chilled
water header connection fl anges is to be applied in the fi eld
by the installer, once the modules are bolted together on site.
Service ports (2) 3/4" threaded ball valves, shall be provided
on the inlet and outlet of each plate heat exchanger, condens-
er and evaporator for maintenance back fl ush and cleaning.
Pete's ports shall be provided on all modules as standard.
Modular Chiller FLEX CS Strainer
X
The
FLEX CS strainer shall be designed for a fl ow of ____
X
GPM, with a maximum pressure loss during maximum fl ow
of 1 PSI. Strainer shall be provided with 80-mesh/178-micron
fi lter element, conical in shape and vertical in orientation.
Pressure construction of the strainer housing, fl anges, nipples,
and screens shall be of type 304 or optional 316 stainless
steel. Strainers shall be provided with 1/4” gauge ports on
the inlet and outlet side of screen and with debris fl ush port
integral to the operation of the strainer. Strainer housing shall
be rated for 125 PSI (clamp lids) or 150 PSI (bolted lid). The
fi lter/strainer shall be installed on the condenser and chilled
water inlets of each bank of chillers.
www.climacoolcorp.com
®