Table e, Torq / gard ratings, Automatic reset – DE-STA-CO TG20 User Manual
Page 5: Single position, Lubrication
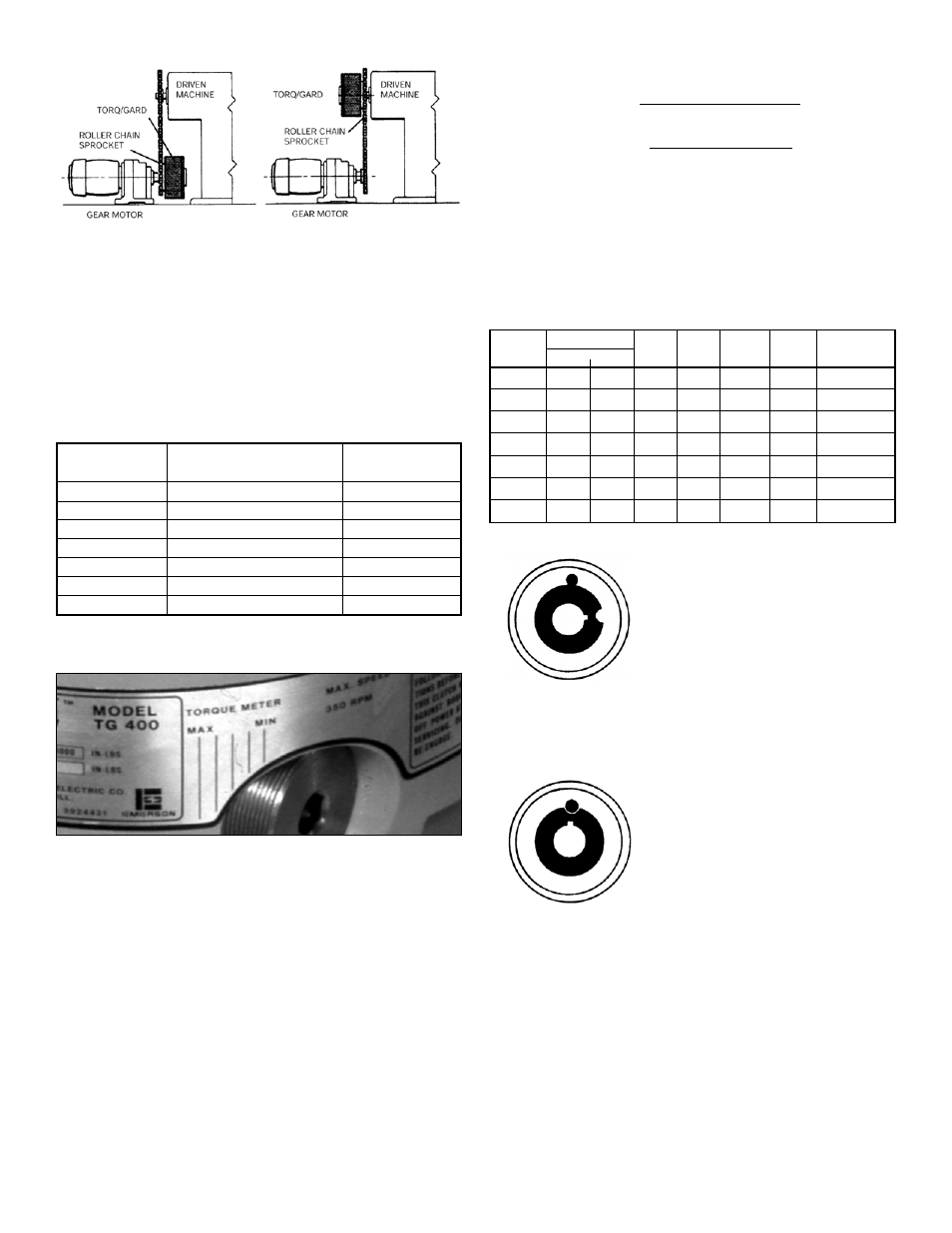
Mounting the clutch on the output of the
gear motor or reducer provides the most
economical clutch assembly. The Torq/Gard
is designed to protect the weakest link in
the drive system.
The Torq/Gard is mounted on the driven
machine and powered through a chain and
sprocket drive. Mounting the clutch in this
position tends to absorb peak starting torques.
The Torq/Gard Clutch is delivered with the torque set at the low end
of its torque range.
1. Turn the single Hex.-Socket Head adjusting nut clockwise to
increase the Torque Setting. (Refer to Table E.) Note: 1/2 inch
Hex-Keyed (Allen) Wrench is required.
Table E
APPROXIMATE TORQUE
MAXIMUM
MODEL
(IN.-LBS.) PER TURN
TURNS
TG-3
2.67
7.5
TG-6
4.4
7.5
TG-20
11
13
TGC60
50 8
TGC200
100 11
TGC400 225
9
TGC800 450
9
2. Sighting the front face of the adjusting nut with the Torque Meter
Lines on the nameplate indicates the approximate torque setting.
3. The “Min.” line on the nameplate is the point at which the
adjusting nut is threaded. Before setting the torque, Perma-Lok
HM118 should be applied to the exposed threads.
4. The first line on the Torque Meter beyond “Min.” represents the
low torque setting.
Warning: The clutch should not be operated at torque settings
below this “line”.
5.
Do not set torque if the clutch is disengaged as an erroneous
torque setting will result.
Warning: Do not remove the adjusting nut. Extremely fine threads
are used to reduce the possibility of the adjusting nut losing its
setting. If the adjusting nut is removed for any reason, (including
lubrication) upon replacing, hand thread the first few turns or cross
threading may occur.
Tripping torque can be established by progressively increasing the
torque setting until the clutch no longer trips under starting loads.
If the tripping torque value is known, the clutch may be pre-set with
a torque wrench or a torque arm and calibrated spring scale.
The Torq/Gard may also be sized by applying one of the following
formulas:
Torque (In.-lbs.) = Horsepower (HP) x 63025
RPM
OR Horsepower =
Torque (In.-lbs.) x RPM
63025
Tripping Torque = Operating Torque x Service Factor
Note: The nameplate contains a sensitized “rectangle” on which
the torque setting may be recorded with ball point pen or a
numbering die.
Warning: The Torq/Gard Clutch is not a “FAIL SAFE” device and
cannot be used on “overhauling” or “holding” load applications.
TORQ / GARD RATINGS
Torque (in.-lbs.)
HP
RPM
Weight
Inertia
Bore Dia.
Models Min.
Max.
Max.
Max.
(lbs.) (WK2)
Max. (inches)
TG-3
13
32
1.5
1800
1.5
1.4
1/2
TG-6
23
56
2.5
1800
1.5
1.4
1/2
TG-20
56
203
4
1800
2.5
5.7
3/4
TGC 60
200
600
8.5
900
5.5
10
1-1/4
TGC 200
600 2000 21.5 680 12
46
1-15/16
TGC
400
2000
4000
22.2
350 38 455 2-7/16
TGC
800
4000
8000
44.4
350 38 455 2-7/16
Automatic Reset
The Torq/Gard Clutch is automatically
reset by “jogging” the motor after the
overload has been corrected. At speeds
under 50 RPM the Torq/Gard will
re-engage, without jogging, upon
starting the motor. The clutch will not
re-engage if the overload exceeds the
torque setting.
Warning: Do not re-engage the Torq/Gard manually. When the clutch
snaps into engagement, injury could occur if the operator’s hand is
near a chain and sprocket or belt drive.
Single Position
The Torq/Gard always resets in the same
position when tripped. It is an excellent
choice in applications that must remain
registered or timed. All Torq/Gard
Clutches are fully reversible.
Lubrication
The Torq/Gard is factory lubricated with Mobilith AW2 and does not
require additional lubrication for many years, under normal
operating conditions.
Clutches used in extreme operating applications may be opened for
regreasing.
Open clutch for greasing by removing torque adjusting nut, detector
system, cover bolts and then tap hub end opposite cover with a soft
hammer. “Do not pry open at cover split line”.
Apply grease (AW2 or equiv.) to hub bearing journals, hub cam
track, follower, thrust washer surfaces and all needle bearings.
5