DE-STA-CO TG20 User Manual
Page 4
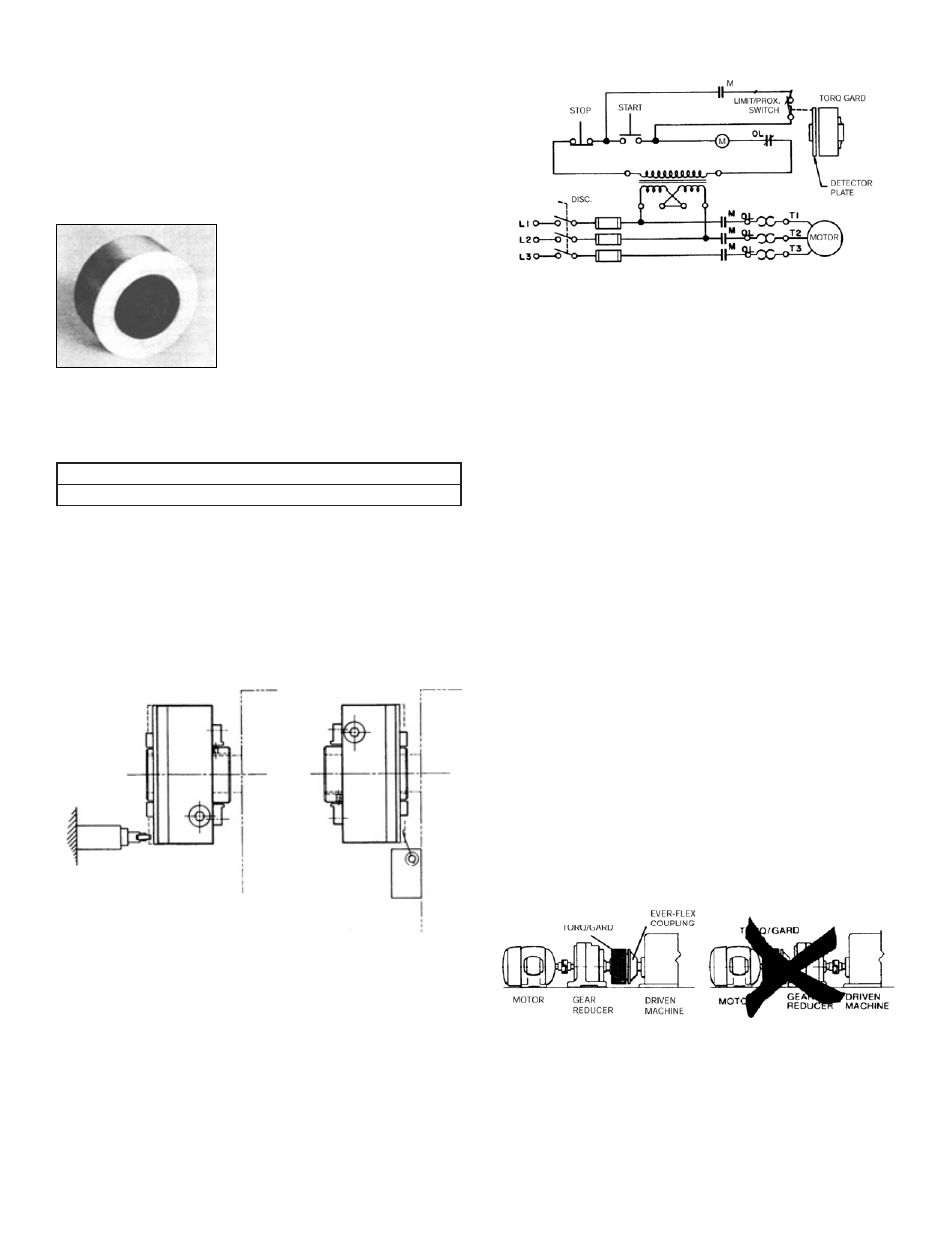
Warning: High inertia loads, reversing loads, excessive vibration or
continual tripping may require the use of Perma-Lok HM160.
6. Tighten set screws against shaft and key.
Warning: Check to insure that the set screws do not extend
beyond the hub on the adapter end. When used on the detector
end the set screws must also engage the detector cam, but must
not extend beyond the detector cam.
Overload Detection
The axial movement of the Detector
Mechanism, when used in conjunction
with a limit/prox. switch, electrically
disconnects the prime mover (motor)
from the load.
The Detector Mechanism consists of a
spring loaded plate mounted on the
clutch cover plate cam. When an
overload occurs, the cam releases the
detector plate a sufficient distance to
actuate a limit/prox. switch. When the overload has been cleared, the
re-engagement of the clutch automatically resets the detector
mechanism. Warning: Detector systems are recommended on all
applications and mandatory on the following:
TG60/TG200 - At speeds over 100 RPM
TG-400/TG800 - At all speeds
Infinitely high shock loads can occur, depending on the type of jam
or overload. The detector system further protects your equipment
under these conditions. On high inertia applications, breaking the
prime mover may have to be considered.
1. The limit/prox. switch must have a rigid mounting.
2. Locate the limit/prox. switch so the detector plate travel will
acuate the limit/prox. switch.
Note: Refer to Figure 1 and Figure 2 for typical installations. Figure 1
mounting is preferred for reasons of rigidity.
3. Refer to the Torq/Gard dimension prints on page 5 for the
detector plate “travel”.
4. When mounting the limit/prox. switch, consult the
manufacturer’s specifications for pre-travel and overtravel.
5. Wire the limit/prox. switch in parallel with the “start” contactor
to permit motor starting after the overload has been cleared.
Note: Refer to Figure 3 “Typical Wiring Diagram”. Limit/prox.
Switches are available with additional contacts to further acuate
warning alarm systems.
Typical Wiring Diagram
6. The detector mechanism can be installed in the field.
A. Place the three (3) detector springs in the three shallow
holes in the Torq/Gard cover.
B. Place the “white” detector plate guide pins in the three deep
holes in the cover.
Note: The pins are registered to fit in one position only.
C. Place the “black” detector cam on the clutch hub with flat
side up.
D. Rotate the cam until each cam lobe is directly over the
detector plate ears and the set screw holes are aligned
with the set screw holes in the hub.
Note: The clutch must be in its engaged position for proper
alignment of the detector mechanism.
E. Secure the detector cam to the clutch hub with the correct
length set screws, using Perma-Lok HM118. (Refer to
Tables B, C or D for the correct shaft set screws.)
Warning: Factory mounted detector mechanisms utilize set
screws for shipping purposes only. The correct length of the set
screws is determined by the shaft diameter used.
Torque Setting
The torque is infinitely adjustable within the nameplated torque
limits of the clutch. Determine the operating and tripping torque
required to drive your machine.
A. Operating torque is the normal full load torque required by
the application.
B. Tripping torque, which is usually higher than operating
torque, depends on the starting torque requirements of
the application and the location of the Torq/Gard Clutch.
C. Mounting the clutch away from the motor tends to absorb
peak starting torques through power transmission and
machine components. (Refer to Fig. 4.)
D. Tripping torque should be set higher than the point at
which the clutch will “nuisance trip” on starting, but
below the maximum torque value the machine can
safely absorb.
Direct Drive application with the Torq/Gard
mounted on the low speed output shaft of
the reducer. The Torq/Gard is shown with a
Browning Ever-Flex half coupling which
mounts on the clutch adapter without
modification. Browning Chain Coupling Kits
are also available for the Torq/Gard when
greater misalignment capabilities are
required. Either side of the Torq/Gard can be
used as the input.
The Torq/Gard should not be used on the
high speed input side of the reducer.
Clutch sensitivity becomes a function of
the reducer’s gear ratio. As an example,
when used with a 100 to 1 reducer, a 100
inch-pound torque variation on the output
side will reflect only a 1 inch-pound
change on the input side. Do not exceed
the maximum RPM shown in the
Torq/Gard selection table.
Figure 1
Figure 2
Figure 4
Figure 3
4