American Expedition Vehicles Tummy Tucker – TJ Rubicon models User Manual
Page 12
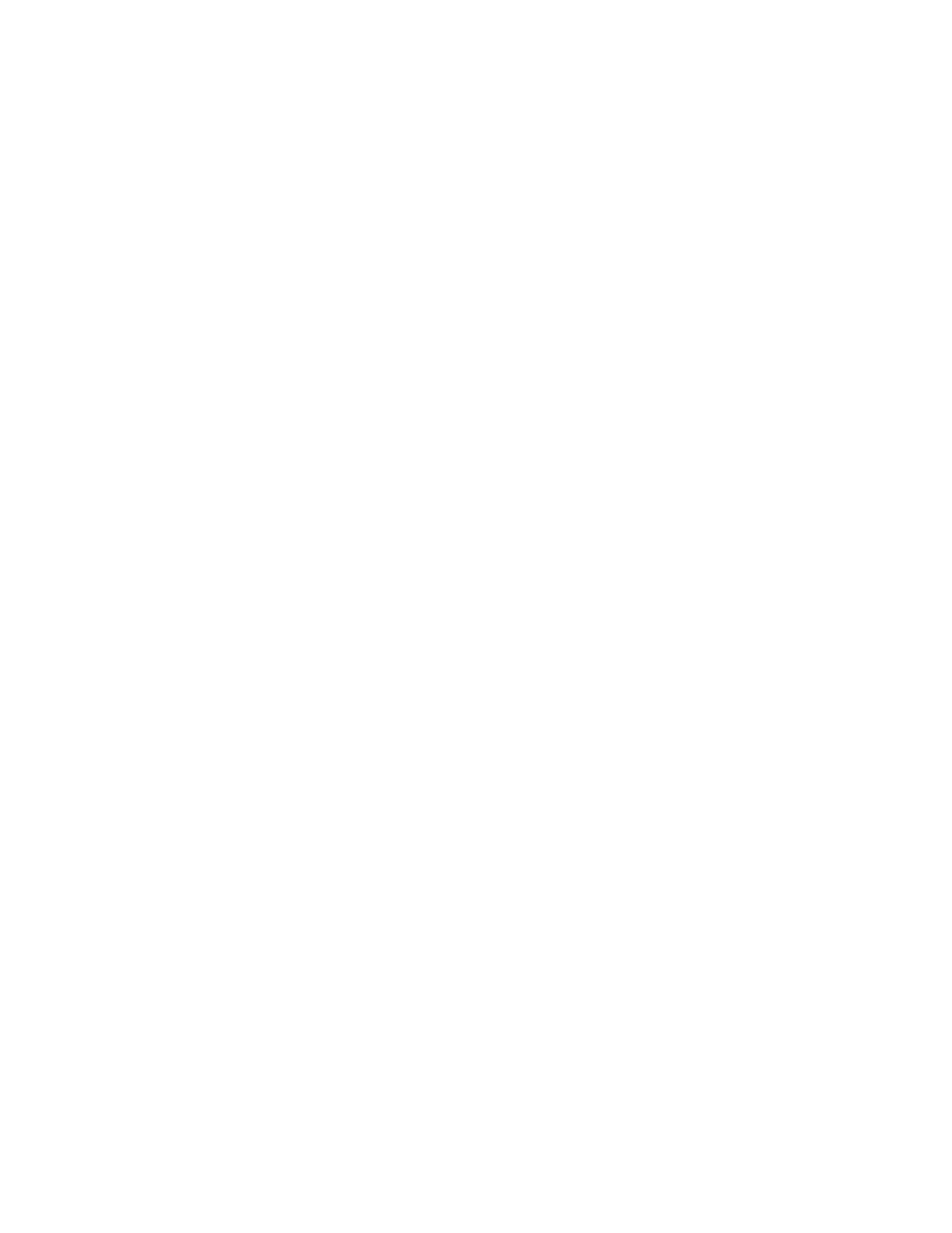
Installation Instructions:
Tummy Tucker™ – TJ Rubicon models
Nth30116 v4.doc
page 12 of 13
www.aev-conversions.com
Appendix: Installation Issues and Additional Modification Solutions
Issue: Vibration while driving. Since drive shaft angles and related vibrations are affected by many
factors besides the TT, including lift height, etc., Nth Degree does not include the means to correct
driveline angles with any TT kit and full-price returns are not granted for vibration issues. If you have any
suspension lift on your Rubicon at all, you must have a double Cardan rear drive shaft and a means to
adjust your rear axle pinion angle.
Be sure the vibration is not out-of-balance tires, etc. by noting the ‘speed’ of the vibration – tire
vibrations are much slower than drive shafts due to the axle ratio. Also, an out-of-balance drive shaft
(due to lost weights or bent, etc.) will vibrate steadily and the intensity will increase evenly with vehicle
speed (like a tire, but faster as mentioned). Vibrations due to bad joint angles will generally have speed
ranges where the vibration intensifies and others where it nearly disappears. Also an angle-induced
vibration will be cyclical – it will ‘drone’ in and out at a given vehicle speed. .If you have issues and don’t
know what to do, here are some tips:
Solution Suggestions: In general, if your suspension lift height is under +5” and you have a double
cardan drive shaft, and a (standard) low pinion rear axle, your should be able to cure most drive shaft
angle-related vibration issues below 80 mph by fine-tuning the pinion angle. However, tire size, axle
ratio, etc. are also factors, so the ‘solution’ may not be as simple as pinion angle. If you are using
relatively small tires for your axle ratio (such as 33’s with 4.56 gears), your driveshaft spins faster at a
given speed and makes eliminating vibrations harder. Some steps to diagnose the problem after
verifying it is not a balance issue:
First, confirm that your relative joint angle at the axle pinion joint is about 1.5 degrees, with the pinion
flatter than the driveshaft – if not, correct this first. Second, check the relative angle at the t-case end – it
should be no more than 22 degrees. If it is more, you may have to choose a combination of ways to
reduce the angle - these can include: shimming the TT down at the frame, adding/increasing the motor
mount lift, lowering the lift height, using a high pinion rear axle, or installing a special high-operating-
angle drive shaft such as a Bigelow/Cornay joint (not just a ‘clearanced’ joint). If you are using a custom
driveshaft that uses an adapter to the factory output flange, you can also reduce the angle by 1-2
degrees or more by changing to a yoke-type output and eliminating the damper and flange – this will
require a new driveshaft that has a yoke-type CV joint and can be about 1.5” longer than the flange-type
CV driveshaft.
If you are having a vibration issue that is dependent on your driving (turning left, accelerating hard,
etc.), the issue may not be angles but contact somewhere between rotating parts and non-rotating ones
– or light contact to the body floor. Check for clearance around both drive shafts including screws
protruding from the floor, etc. Keep in mind that the t-case front output rises during acceleration (may
touch floor) and drops during compression braking (may touch TT). If you have an automatic and feel 3
to 4 mild ‘thumps’ during a hard launch from standing still that seem to come from right under the driver’s
seat, you need more clearance at the dimple from step 4.
Issue: Vibration while Idling. If you notice significantly more vibration while sitting still with the engine
running, the issue is most likely that there is contact somewhere between the powertrain and the body
floor or TT. These should have been caught and corrected in step 12, but something may have been
overlooked or too hidden to detect visually.
Solution Suggestions: Thoroughly inspect the area above the TT for any contact between parts that
was missed previously. On 4-speed automatics, especially check the clearance above the bellhousing
as mentioned in step 4a.
Also check the t-case linkage relay rod and confirm that it is not bound up or plunged to the point
where it is contacting the tunnel though the tunnel-end bracket. If the linkage is not close to horizontal, it
may be binding and the vibration is then transmitted to the interior through the rod. You can try
disconnecting the relay rod to test if it is the ‘noise path’.
Another possibility is wrong or incorrectly installed isolators. Make sure that the isolators are sitting
flat on the TT and have a uniform, slightly conical shape. If they appear distorted to one side, front, or
back, or are otherwise unevenly shaped, there is an unnatural preload on them that should not be