Gorman-Rupp Pumps PA4B60-4045H 1497876 and up User Manual
Page 38
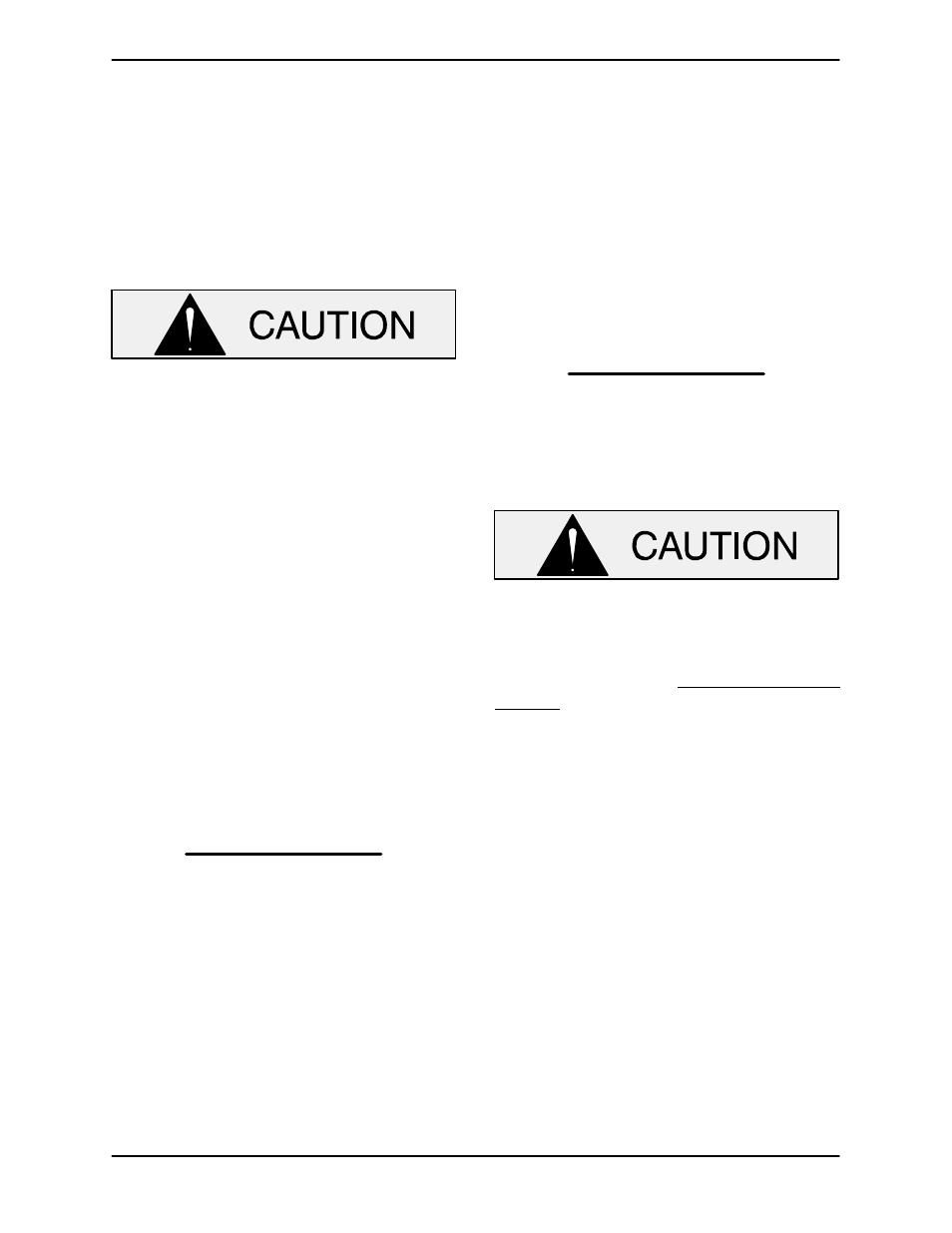
PA SERIES
OM−06228
MAINTENANCE & REPAIR
PAGE E − 18
After the bearing is installed on the shaft, pack the
bearing by hand with No. 0 lithium base grease un-
til the bearing rollers are thoroughly lubricated. Se-
cure the bearing on the shaft with the bearing re-
taining ring (24).
Slide the shaft and assembled bearing into the in-
termediate bore from the drive end until the bear-
ing seats squarely against the bore shoulder.
When installing the shaft and bearing into
the bearing bore, push against the outer
race. Never hit the balls or ball cage.
If removed, install the retaining ring (20) in the
groove in the oil chamber plate (21). Install a new
O-ring (22) in the groove in the oil chamber plate
and lubricate it with light oil.
Install the same thickness of bearing adjusting
shims (9) as previously remove, and position the
bearing retainer (23) against the shims. Install a
new gasket (17) and press the oil chamber plate
into the intermediate until the retaining ring (20) is
fully seated against the bearing retainer. Secure
the oil chamber plate to the intermediate with the
hardware (18 and 19).
NOTE
Impeller shaft endplay should be between .002 and
.010 inch (0,05 to 0,25 mm). To achieve the correct
endplay, add or remove bearing shims (9) as re-
quired.
Position the inboard lip seal (18) in the intermediate
bore with the lip positioned as shown in Figure 4
and press it into the intermediate until it is just flush
with the inner machined face of the intermediate
bore.
Position the outboard lip seal (18A) in the inter-
mediate bore with the lip positioned as shown in
Figure 4 and press it into the intermediate until it is
fully seated against the inboard lip seal.
Lubricate the bearing cavity as indicated in LUBRI-
CATION at the end of this section.
Securing Intermediate and Drive Assembly to
Engine
(Figure 5)
Install the shaft key (14, Figure 4) in the shaft key-
way. Position the flexible portion of the coupling as-
sembly (3) on the shaft to the dimension shown in
Figure 5.
NOTE
The flexible portion of the coupling must be proper-
ly positioned on the shaft. The heads of the caps-
crews in the center of the coupling must be posi-
tioned toward the pump end of the shaft.
Align the keyway in the bushing (2) with the shaft
key and slide it onto the shaft. Rotate the flexible
portion of the coupling until the tapped holes for
the two setscrews align with those in the bushing,
and install the setscrews.
Make certain that the flexible portion of the
coupling is mounted as shown in Figure 5.
The end of the shaft must be recessed
aproximately 0.41 inch (10 mm) from the
face of the bushing. This dimension is
critical. If the coupling is not properly posi-
tioned on the shaft, the coupling parts may
not fully engage, or a pre-load condition
can cause premature bearing failure.
With the flexible portion of the coupling and the
bushing properly positioned on the shaft, tighten
the two setscrews in an alternating sequence until
the bushing and coupling are fully secured. Torque
the setscrews to 14.6 ft. lbs. (175 in. lbs. or 2 m.
kg.).
If the complete coupling assembly is being re-
placed, apply ‘Loctite Retaining Compound No.
242’ or equivalent compound to the threads of the
capscrews (5). Secure the outer ring of the cou-
pling to the engine flywheel by installing the hard-
ware (4 and 5) and torquing the capscrews to 45 ft.
lbs. (540 in. lbs. or 6,2 m. kg.).
NOTE
To ease installation, lightly lubricate the rubber por-
tion of the coupling with a non-petroleum based