Gorman-Rupp Pumps PA6C60-QSB4.5P 1537244 and up User Manual
Page 45
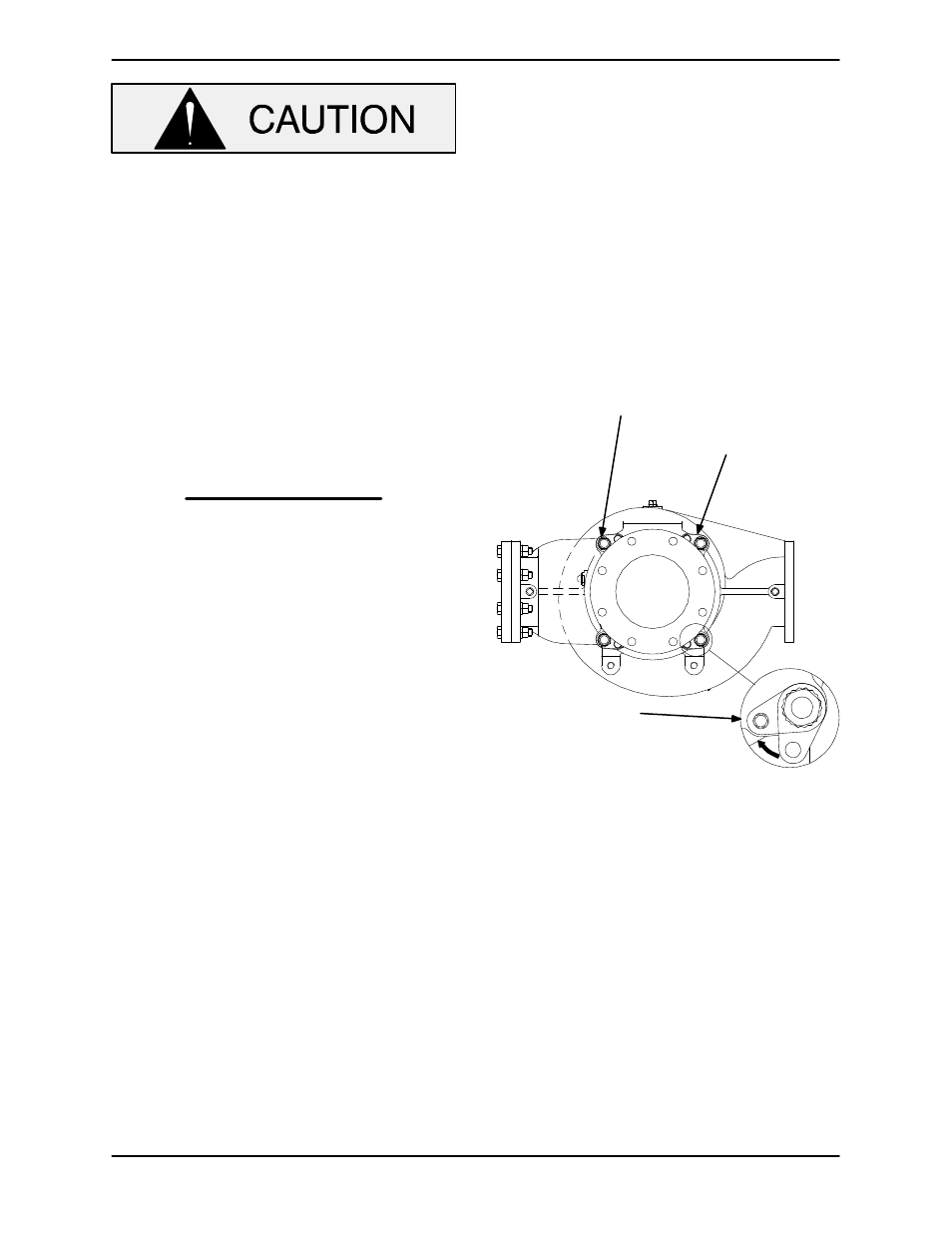
OM-06553
PA SERIES
MAINTENANCE & REPAIR
PAGE E - 23
The shaft and impeller threads must be
completely clean before reinstalling the im
peller. Even the slightest amount of dirt on
the threads can cause the impeller to seize
to the shaft, making future removal difficult
or impossible without damage to the im
peller or shaft.
Install the same thickness of impeller adjusting
shims (29) as previously removed and screw the
impeller assembly onto the shaft until tight.
NOTE
At the slightest sign of binding, immediately back
the impeller off, and check the threads for dirt. Do
not try to force the impeller onto the shaft.
A clearance of .025 to .040 inch (0,64 to 1,02 mm)
between the impeller and the seal plate is neces
sary for maximum pump efficiency. Measure this
clearance, and add or remove impeller adjusting
shims as required.
Secure the impeller to the shaft with the impeller
washer and capscrew (26 and 27).
Pump Casing Installation
(Figure 4)
Lubricate the rotating assembly O‐rings (15 and
16) with a light coating of grease. Use a suitable
hoist and sling to slide the pump casing (1) over the
rotating assembly.
Install two shims (17) at each mounting location
and secure the casing to the rotating assembly (2)
with the hardware (18 and 19).
Wear Plate And Back Cover Plate Installation
And Adjustment
(Figures 4 and 11)
If the wear plate (24) was removed for replace
ment, carefully center it on the back cover plate as
sembly (32) and secure it with the hardware (26
and 27).
Lubricate the O‐rings (16 and 25) with light grease
and install them in the grooves in the wear plate
and back cover.
Clearance between the impeller and wear plate is
adjusted using the four back cover nuts (31) and
locking collars (28). There are 18 detents on the
I.D. of each locking collar. Indexing the collars one
detent on the adjusting screws represents approxi
mately .005 inch (0,13 mm) of wear plate clear
ance. The recommended clearance between the
wear plate and the impeller is .010 to .020 inch
(0,25 to 0,50 mm).
USE TWO
OPPOSING
BACK COVER
NUTS TO PRESS
BACK COVER
INTO PUMP
CASING
USE TWO REMAINING
ADJUSTING SCREWS AND
LOCKING COLLARS TO SET
FACE CLEARANCE
TURN INDEX COLLARS
3 DETENTS COUNTER‐
CLOCKWISE, THEN
TURN CLOCKWISE UN
TIL SCREW HOLES
ALIGN
Figure 11. Installing and Adjusting Back Cover
Screw the four adjusting screws (30) into the
tapped holes in the back cover plate until they are
just flush with the machined surface on the back
side of the cover plate.
Align the back cover plate over the studs (23) and
slide it into the pump casing. Use two back cover
nuts (31) on diagonally opposing studs to press
the back cover into the pump casing until the wear
plate just touches the impeller when the shaft is
turned by hand. Tighten the nuts evenly to avoid
binding.
With the wear plate just touching the impeller, turn
the two free adjusting screws until they engage the
pump casing. Position the locking collars over the