Gorman-Rupp Pumps 4D-X3 1P User Manual
Page 15
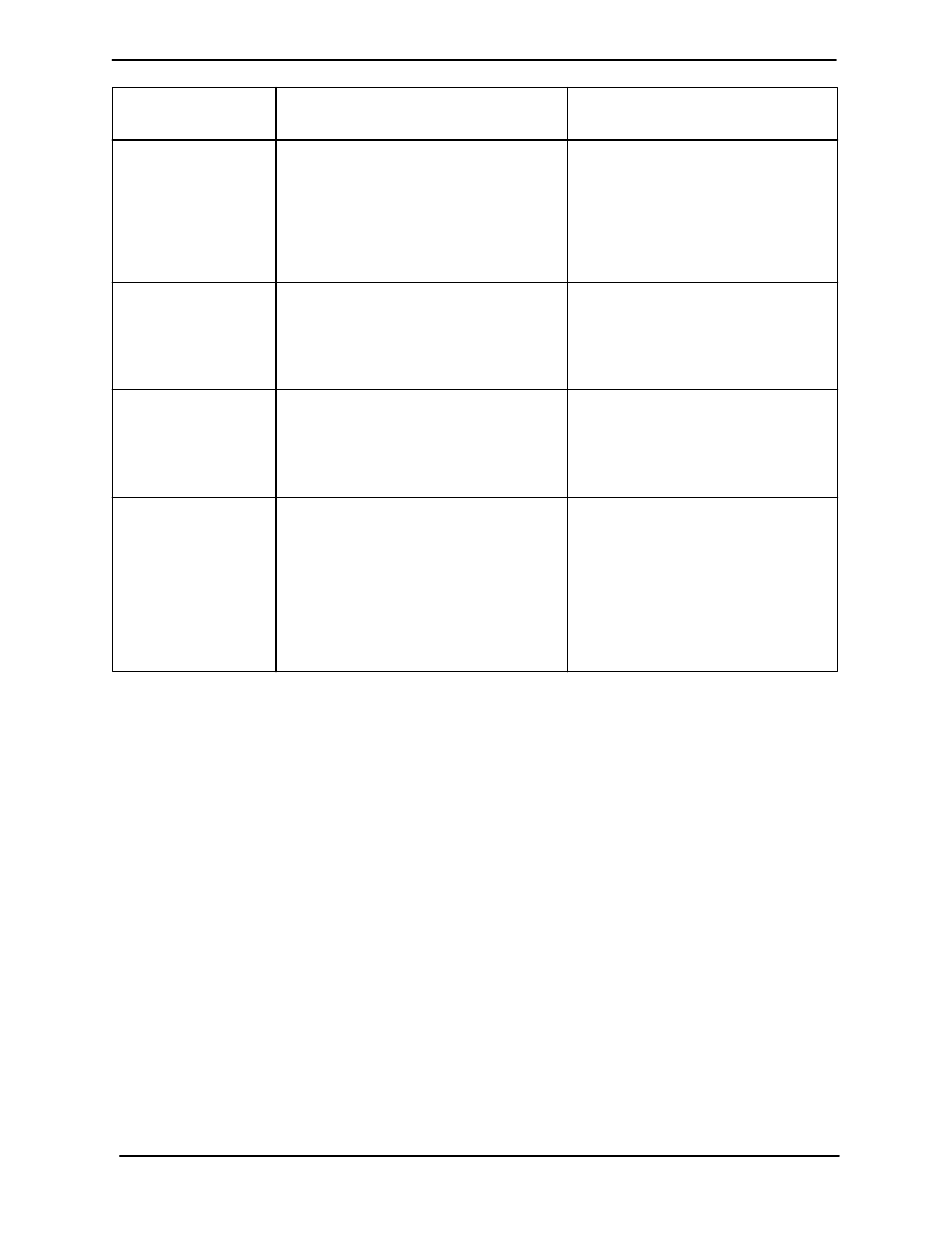
TROUBLE
POSSIBLE CAUSE
PROBABLE REMEDY
PUMP REQUIRES
TOO MUCH
POWER
PUMP CLOGS
FREQUENTLY
EXCESSIVE NOISE
BEARINGS RUN
TOO HOT
OM--01515
D SERIES
TROUBLESHOOTING
PAGE D -- 2
Liquid solution too thick.
Dilute if possible.
Integral discharge check valve clogged Clean valve.
or binding.
Bearings in motor or gearbox
Check bearings.
worn or binding.
Integral suction or discharge check
Clean valves, check that flange nuts
valve clogged, binding, or not seating
are tight.
properly.
Liquid solution too thick.
Dilute if possible.
Pump, gearbox, or motor not
Check and tighten mounting bolts.
securely mounted.
Gearbox or motor not properly
See
LUBRICATION in MAINTE-
lubricated.
NANCE AND REPAIR.
Bearing temperature is high, but within Check bearing temperature regularly
limits.
to monitor any increase.
Low or incorrect lubricant.
Check for proper type and level of
lubricant.
Drive misaligned.
Align drive properly.
PREVENTIVE MAINTENANCE
Since pump applications are seldom identical, and pump wear is directly affected by such things as the
abrasive qualities, pressure and temperature of the liquid being pumped, this section is intended only to
provide general recommendations and practices for preventive maintenance. Regardless of the application
however, following a routine preventive maintenance schedule will help assure trouble-free performance
and long life from your Gorman-Rupp pump. For specific questions concerning your application, contact
your Gorman-Rupp distributor or the Gorman-Rupp Company.
Record keeping is an essential component of a good preventive maintenance program. Changes in suction
and discharge gauge readings (if so equipped) between regularly scheduled inspections can indicate
problems that can be corrected before system damage or catastrophic failure occurs. The appearance of
wearing parts should also be documented at each inspection for comparison as well. Also, if records indi-
cate that a certain part (such as the seal) fails at approximately the same duty cycle, the part can be checked
and replaced before failure occurs, reducing unscheduled down time.
For new applications, a first inspection of wearing parts at 250 hours will give insight into the wear rate for
your particular application. Subsequent inspections should be performed at the intervals shown on the
chart below. Critical applications should be inspected more frequently.