Gorman-Rupp Pumps 16C2-4045T 1514991 and up User Manual
Page 30
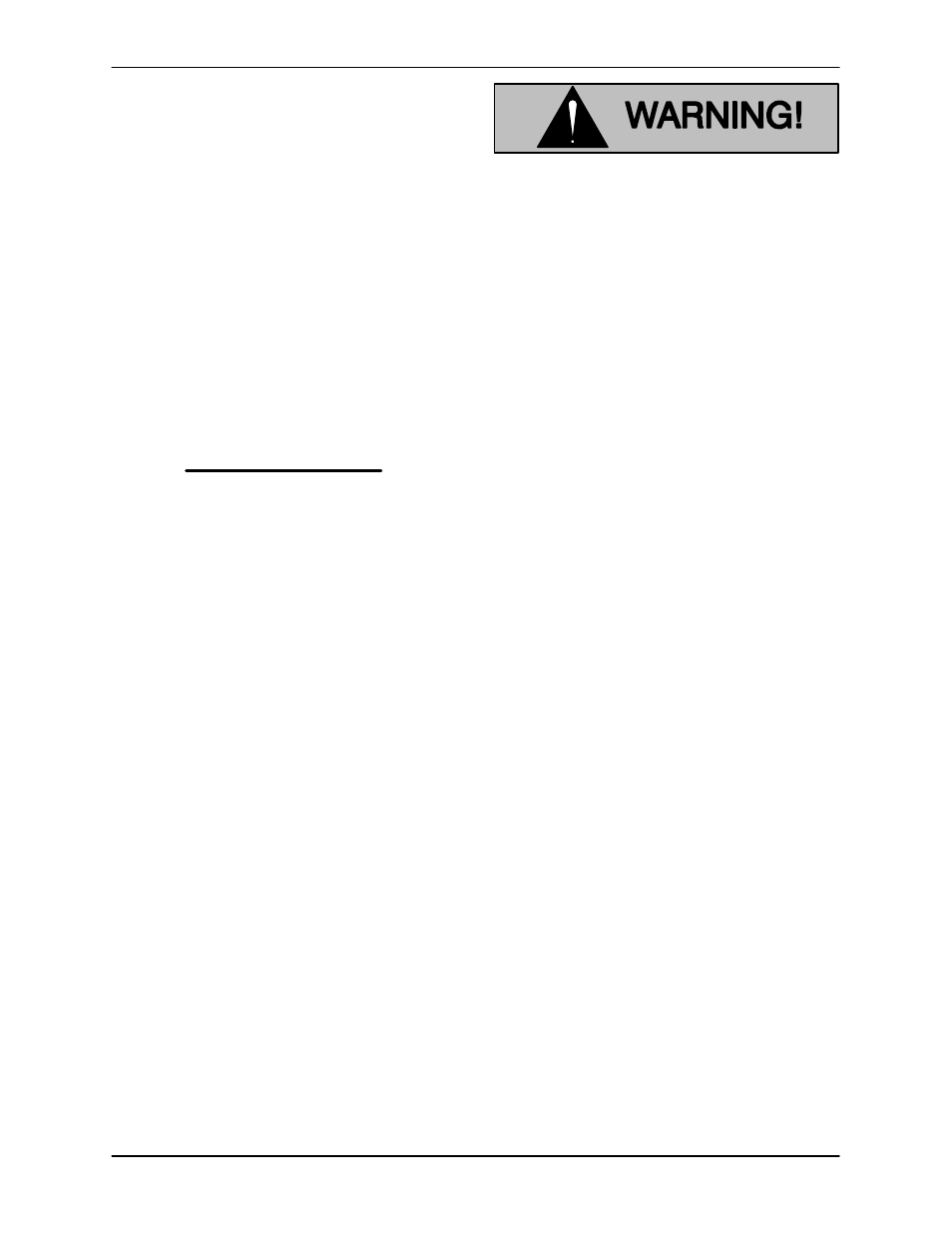
10 SERIES
OM-06541
MAINTENANCE & REPAIR
PAGE E - 10
Inspect the wear plate and replace it if badly scored
or worn. To remove the wear plate, disengage the
hardware (52 and 53).
Suction Check Valve Removal
(Figure 3)
If the check valve assembly (73) is to be serviced,
reach through the back cover opening and hold
the assembly in place while removing the check
valve pin (74). Slide the assembly out of the check
valve seat (65) and remove it from the pump.
NOTE
Further disassembly of the check valve is not re
quired since it must be replaced as a complete unit.
Individual parts are not sold separately.
The check valve assembly may also be serviced by
removing the suction flange (70). To remove the
flange, disengage the hardware (68 and 69) and
separate the flange from the check valve seat. Re
move the machine screws (66) and pull the seat
and assembled check valve from the suction port.
Remove the check valve pin and pull the check
valve assembly out of the seat.
Replace the flange gaskets (64 and 67) as re
quired.
Pump Casing Removal
(Figure 3)
To service the impeller or seal assembly, discon
nect the suction and discharge piping. Remove the
hardware securing the pump casing (1) to the
base.
Remove any leveling shims used under the casing
mounting feet. Tie and tag the shims for ease of
reassembly.
Remove the nuts (16) securing the pump casing to
the seal plate (48). Install a standard 5/8‐11
UNC-2B lifting eye in the tapped hole in the top of
the pump casing. Be sure to screw the eye into the
casing until fully engaged. Use a hoist and sling of
suitable capacity to separate the casing from the
seal plate and intermediate.
Do not attempt to lift the complete pump
unit using the lifting eye. It is designed
to facilitate removal or installation of in
dividual components only. Additional
weight may result in damage to the
pump or failure of the eye bolt.
Remove the pump casing gaskets (49). Tie and tag
the gaskets or measure and record their thickness
for ease of reassembly.
Impeller Removal
(Figure 3)
Turn the cross arm on the automatic lubricating
grease cup (17) clockwise until it rests against the
cover (see Figure 6). This will prevent the grease
from escaping when the impeller is removed.
To remove the impeller (2), tap the vanes in coun
terclockwise direction (when facing the impeller)
with a block of wood or soft‐faced mallet. Be care
ful not to damage the impeller. When the impeller
breaks loose, unscrew it from the shaft. Use cau
tion when removing the impeller; tension on the
shaft seal spring will be released as the impeller is
unscrewed. Inspect the impeller and replace if
cracked or badly worn.
Slide the impeller adjusting shims (31) off the im
peller shaft (42). Tie and tag the shims or measure
and record their thickness for ease of reassembly.
Seal Removal and Disassembly
(Figure 3)
To remove the seal assembly (3), remove the
grease cup and piping (17, 18 and 19). Slide the
seal plate and seal parts off the shaft as a single
unit. Be careful not to drop or damage any seal
parts.
Carefully remove the stationary and rotating seal
elements, packing rings, seal spring, and shaft
sleeve from the seal plate.
NOTE
The seal assembly may be removed without com