Gorman-Rupp Pumps 86A2-4024H 1535998 and up User Manual
Page 33
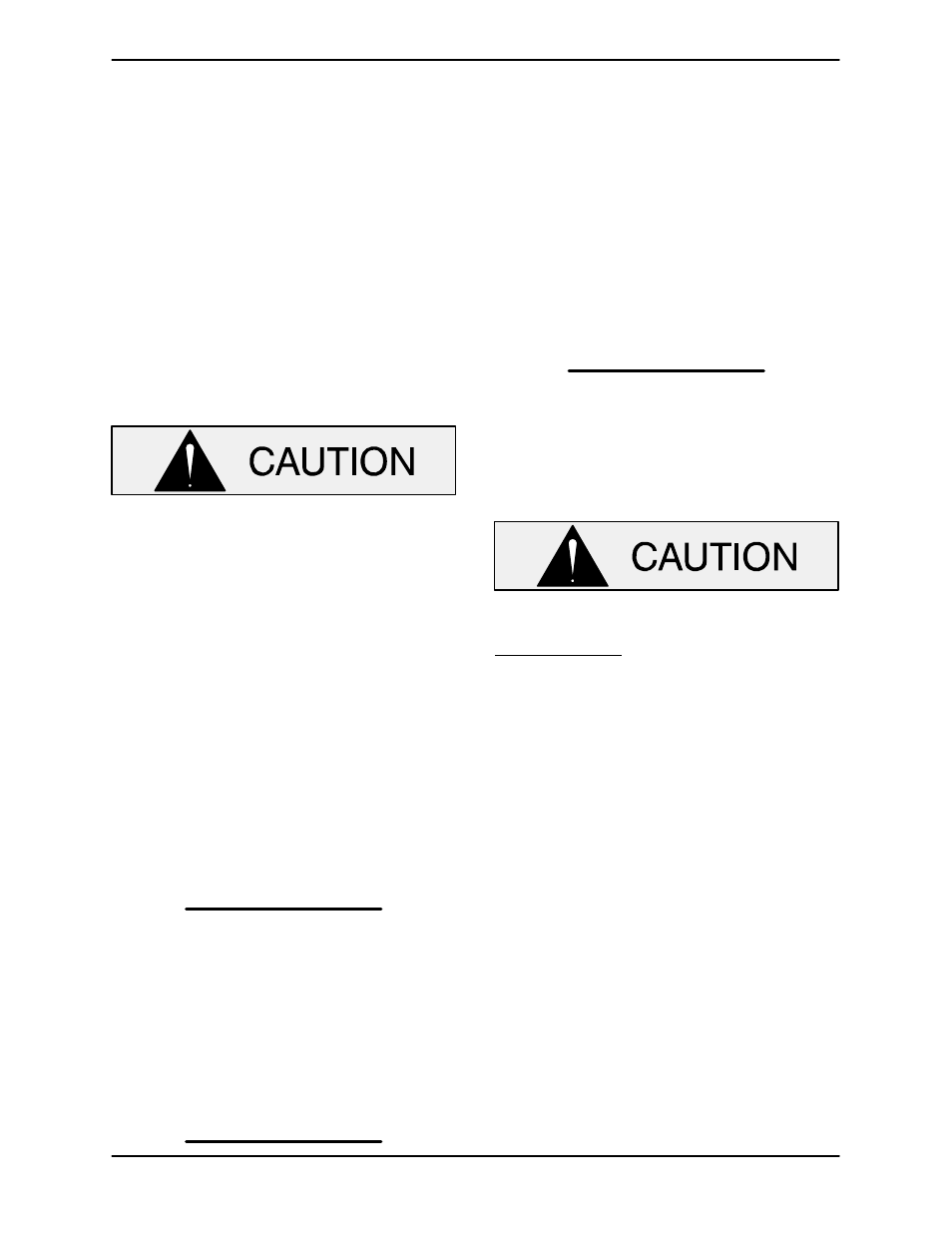
80 SERIES
OM-06413
MAINTENANCE & REPAIR
PAGE E - 14
Slide the seal spacer washer (15) onto the shaft
with the chamfered side facing the shaft shoulder.
Reinstall the automatic grease cup and piping (16,
17 and 18) in the seal plate. After the impeller has
been installed, lubricate the seal as indicated in
LUBRICATION.
Impeller Installation
(Figure 3)
Inspect the impeller, and replace it if cracked or
badly worn. Inspect the impeller and shaft threads
for dirt or damage, and clean or dress the threads
as required.
The shaft and impeller threads must be
completely clean before reinstalling the im
peller. Even the slightest amount of dirt on
the threads can cause the impeller to seize
to the shaft, making future removal difficult
or impossible without damage to the im
peller or shaft.
Install the same thickness of impeller adjusting
shims (13) as previously removed. Apply `Never‐
Seez' or equivalent to the shaft threads and screw
the impeller onto the shaft until tight. Be sure the
seal spring seats squarely on the back side of the
impeller.
NOTE
At the slightest sign of binding, immediately back
the impeller off, and check the threads for dirt. Do
not try to force the impeller onto the shaft.
A clearance of .020 to .040 inch (0,5 to 1,0 mm) be
tween the impeller and the seal plate is recom
mended for maximum pump efficiency. Measure
this clearance and add or subtract impeller shims
as required.
NOTE
The seal plate must be tight against the intermedi
ate while setting the back impeller clearance.
Securing Intermediate And Drive Assembly To
Engine
(Figure 4)
Install the shaft key (25, Figure 3) in the shaft key
way. Position the flexible portion of the coupling as
sembly (3) on the shaft as shown in Figure 4.
NOTE
The flexible portion of the coupling must be proper
ly positioned on the shaft. The heads of the caps
crews in the center of the coupling must be posi
tioned toward the pump end of the shaft.
Align the keyway in the bushing (2) with the shaft
key, and slide it onto the shaft until it is just flush
with the end of the shaft. Rotate the flexible portion
of the coupling until the tapped holes for the two
setscrews align with those in the bushing, and in
stall the setscrews.
Make certain that the flexible portion of the
coupling is mounted as shown in Figure 4.
This is critical. If the coupling is not prop
erly positioned on the shaft, the coupling
parts may not fully engage, or a pre‐load
condition can cause premature bearing
failure.
The end of the shaft must be just flush with
the face of the bushing. This will allow the
two portions of the coupling to fully engage
when the intermediate is secured to the en
gine bellhousing, without pre‐loading the
bearings.
With the flexible portion of the coupling and the
bushing properly positioned on the shaft, tighten
the two setscrews in an alternating sequence until
the bushing and coupling are fully secured. Torque
the setscrews to 14.5 ft. lbs. (175 in. lbs. or 2,02 m.
kg.).
If the complete coupling assembly is being re
placed, apply `Loctite Retaining Compound No.
242' or equivalent to the threads of the hardware (4
and 5), and secure the outer ring of the coupling to
the engine flywheel by torquing the hardware to 45
ft. lbs. (540 in. lbs. or 6,2 m. kg.).