Gorman-Rupp Pumps 06D1-GA 1005542 and up User Manual
Page 16
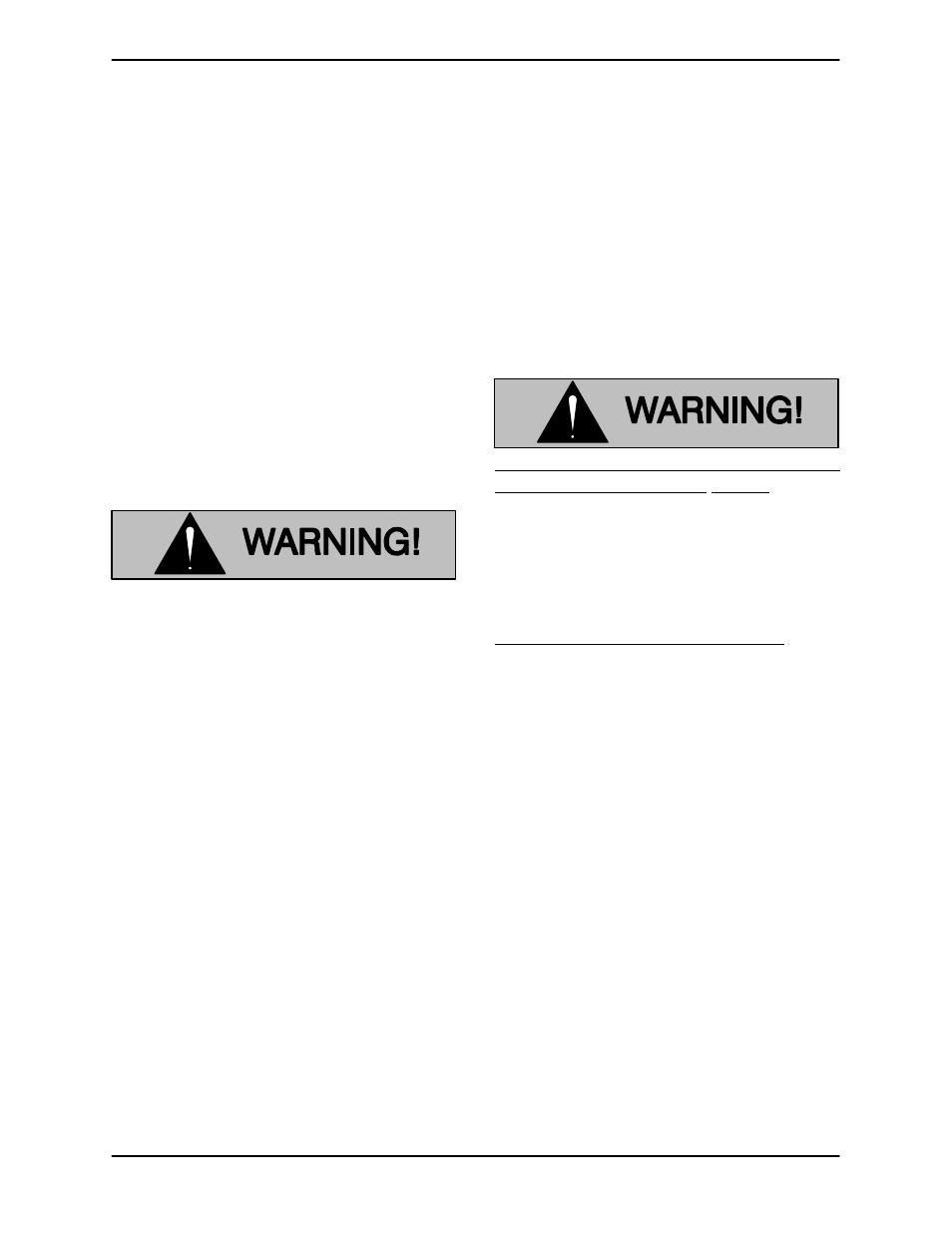
OM-01256
0 SERIES
OPERATION
PAGE C - 2
ing the input drive shaft. The correct direction of
pump rotation for pump model 06D1-GAR is
clockwise when facing the input drive shaft. The
pump could be damaged and performance ad
versely affected by incorrect rotation. If pump per
formance is not within the specified limits (see the
curve on Page E-1), check the direction of rotation
before further troubleshooting.
Drive
This pump is designed for operation with a power
take‐off unit coupled to the drive shaft on the gear
box. The gearbox assembly has a ratio of 2.18:1,
and is designed for operation at a maximum input
speed of 2200 RPM . Do not operate at a higher in
put speed.
The gearbox provided on this pump is
designed for operation at 2200 RPM
maximum input speed. If operated at a
higher RPM, pump components may be
destroyed.
OPERATION
Partially open the discharge throttling valve so that
the discharge line fills slowly to prevent damage to
piping, gaskets, and other devices in the line which
could be affected by shock resulting from rapid fill
ing of the line. When the discharge line is com
pletely filled, adjust the discharge throttling valve to
the desired flow rate.
Leakage
No leakage should be visible at pump mating sur
faces, or at pump connections or fittings. Keep all
line connections and fittings tight to maintain maxi
mum pump efficiency.
Liquid Temperature And Overheating
The maximum liquid temperature for this pump is
160
_ F (71_C). Do not apply it at a higher operating
temperature.
Overheating can occur if operated with the valves
in the suction or discharge lines closed. Operating
against closed valves could bring the liquid to a
boil, build pressure, and cause the pump to rup
ture or explode. If overheating occurs, stop the
pump and allow it to cool before servicing it. Refill
the pump casing
with cool liquid.
Allow an overheated pump to complete
ly cool before servicing. Do not remove
plates, covers, gauges, pipe plugs, or
fittings from an overheated pump. Liq
uid within the pump can reach boiling
temperatures, and vapor pressure with
in the pump can cause parts being dis
engaged to be ejected with great force.
After the pump completely cools, drain
the liquid from the pump by removing
the casing drain plug. Use caution when
removing the plug to prevent injury to
personnel from hot liquid.
Strainer Check
If a suction strainer has been shipped with the
pump or installed by the user, check the strainer
regularly, and clean it as necessary. The strainer
should also be checked if pump flow rate begins to
drop. If a vacuum suction gauge has been in
stalled, monitor and record the readings regularly
to detect strainer blockage.
Never introduce air or steam pressure into the
pump casing or piping to remove a blockage. This
could result in personal injury or damage to the
equipment. If backflushing is absolutely neces
sary, liquid pressure must be limited to 50% of the
maximum permissible operating pressure shown
on the pump performance curve (see Section E,
Page 1).