Pump Solutions Group Neptune Series 7000 dia-PUMP MODELS 7100 thru 7200 User Manual
Page 8
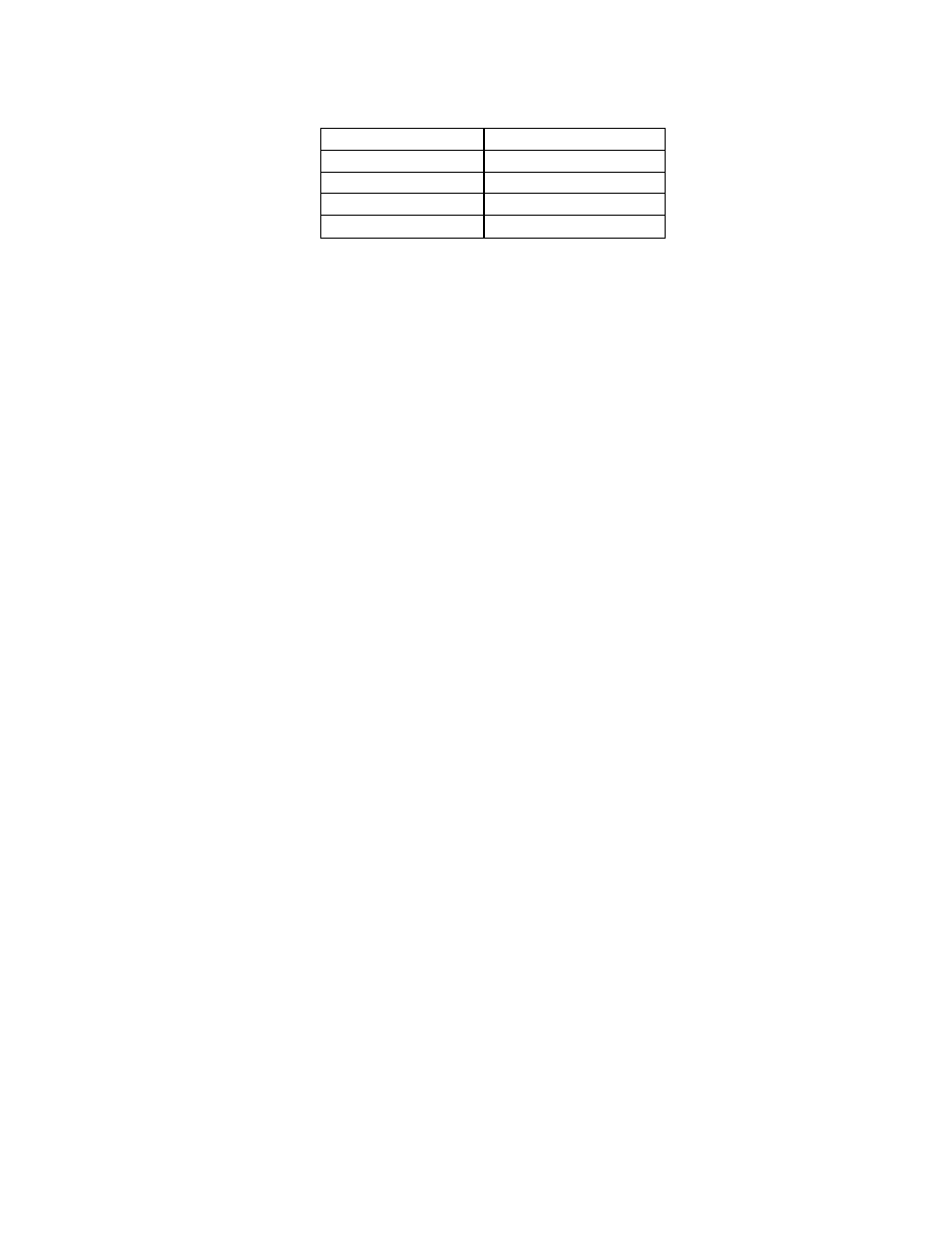
8
The hydraulic fluid supplied by Neptune is Industrial Tufoil
Common sources for hydraulic fluid are:
Fluoramics Inc
Industrial Tufoil
All piping systems should include:
1.1.1
A separate system relief valve to protect piping and process equipment, including the pump, from
excess process pressures.
*An external relief valve is required!!
1.1.2
Shutoff valves and unions (or flanges) on suction and discharge piping. This permits check valve
inspection without draining long runs of piping. Shutoff valves should be of the same size as con-
necting pipe. Ball valves are preferred since they offer minimum flow restriction.
1.1.3
An inlet strainer, if the product is not slurry. Pump check valves are susceptible to dirt and other solid
contaminants unless designed for that service, and any accumulation can cause malfunction. The
strainer should be located between the suction shutoff valve and the pump suction valve. It must be
sized to accommodate the flow rate and the anticipated level of contamination. A 100-mesh screen
size is recommended.
1.1.4
Valve housings or other portions of the reagent head must not support piping weight, as the resulting
stresses can cause leaks. In piping assembly, use a sealing compound chemically compatible with
the process material.
SUCTION PRESSURE REQUIREMENTS
Although Mechanical Diaphragm metering pumps have suction lift capability, a flooded suction is
preferable whenever possible. The pump should be located as close as possible to the suction side
reservoir or other source.
The pump will self-prime with 10 ft (3 meters) of water suction lift (wetted valves, zero back pressure,
full stroke and speed, water like solutions). Once primed, the pump is capable of up to 10 feet (3
meters) of water suction lift.
All Mechanical Diaphragm metering pumps are designed for continuous service at the rated
discharge pressure. The discharge pressure must exceed suction pressure by at least 6 Psia (or
0.41 Bar). This can be achieved where necessary by the installation of a backpressure valve in the
discharge line.
2.0
SUCTION PIPING
2.0.1 The suction piping to the pump must be absolutely airtight for optimum operation any leakage in the
suction line will reduce pumping capacity. Pipe should be one size larger than suction inlet size of
the pump. It is suggested that the suction piping be tested with low air pressure and a soap solution
to assure that no leaks exist. Limit the total length of the suction line to 5-8 feet for suction lift or 8-10
feet for flooded suction. Minimize bends, elbows, or other restrictions for better pumping efficiency.
2.0.2 NEPTUNE RECOMMENDS THAT The Mechanical Diaphragm metering pumps BE OPERATED
WITH A FLOODED SUCTION, AS THIS WILL FACILITATE START UP AND INCREASE THE
SERVICE LIFE OF THE PUMP.