Installation, Site preparation, Flow direction – Pump Solutions Group Neptune GLYCOL FEED SYSTEM G-100-1A, G-100-2A User Manual
Page 9: Suction plumbing, General piping, Alignment, Belt drive, Fasteners, Pressure relief
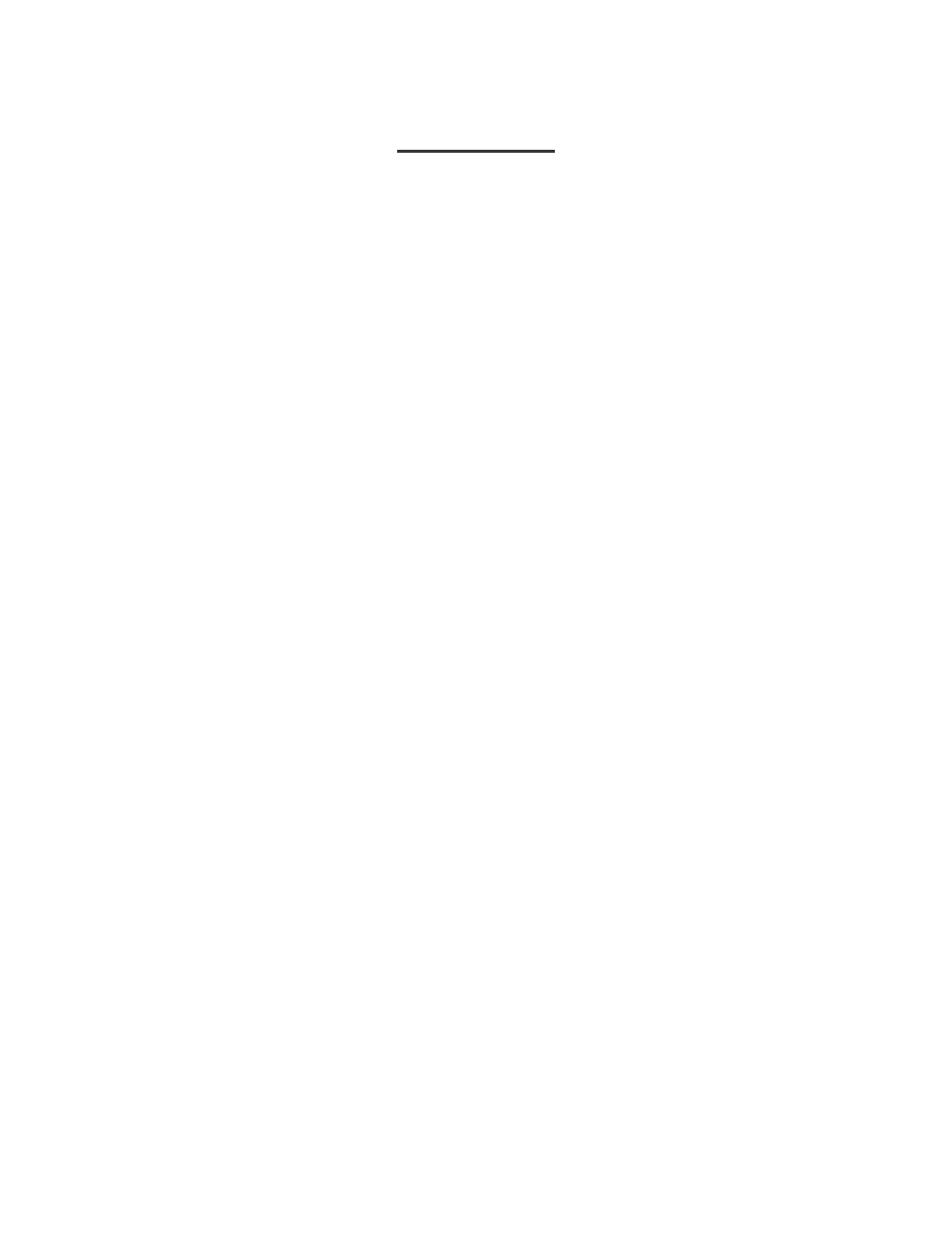
BRONZE ROTARY GEAR PUMP INSTRUCTIONS continued …….
INSTALLATION
Site Preparation
Choose a site that allows easy access to the pump for maintenance. Consider protection from the elements. Guard against drips and spray
from nearby equipment. Choose a solid foundation for mounting. If noise is a concern, consider a rubber pad under the pump base to
dampen.
Flow Direction
Gear pumps will perform equally well in either direction however care must be taken for pumps equipped with integral pressure relief valves.
To change flow direction effectively reversing the suction and discharge ports, simply switch driver rotation by following motor wiring
diagram instructions and change the location of the relief valve as shown below. Most pump motor units are factory supplied with
counterclockwise shaft rotation (when viewing the pump from the shaft end).
Suction Plumbing
Suction side plumbing considerations are key to desirable pump performance. Minimize head loss by assuring sufficient pipe size (especially
important for highly viscous services). Generally the same size pipe as the pump ports is adequate. For long runs (beyond 3 feet) or viscous
fluids, use one or two pipe sizes larger. Strive to keep the lines as short and straight as possible. If flexible lines are used, they should be
selected to prevent wall collapse. To keep the pump from being starved or running dry, be sure there is sufficient fluid supply. A flooded
suction is generally preferred. Suction lifts over 3 vertical feet and long horizontal runs (beyond 3 lineal feet) require a foot or check valve
below the level of the liquid being pumped. When taking suction from a tank or vessel, position the inlet above the maximum expected level
of solids. Use full-bore ball valves or gate valves to minimize restriction. Suction strainers should be properly sized to minimize pressure
drop and positioned for easy cleaning access. If start-up screens are used, be sure they are removed prior to placing the system into regular
operation. Orient lines so as to prevent formation of air pockets. Be sure all joints are tight. Flush out all suction lines prior to installing the
pump.
General Piping
For further ease of maintenance, use union fittings to connect the pump to the system. Install a discharge priming tee for convenience. Do not
spring the piping to connect the pump. Use piping supports or hangers as required. When necessary, provide for thermal expansion and
contraction to avoid placing strain on the pump.
Alignment
Proper alignment is key to seal and bearing performance. Improper alignment can lead to premature pump failure. Check the alignment
carefully between the pump and the drive.
Belt Drive
Though alignment is not as critical as direct connected, ensure that the pump and motor shafts are parallel and in line. For units suitable for
belt drive, be sure that the belt tension is adequate (per the belt manufacturer’s recommendation) but do not overtighten. For heavy pulley
loads, models are equipped with external ball bearing supports. A single 1/2” (A or 4L section) V-belt is satisfactory for drive speeds up to 1
HP 3450 RPM. For larger drive sizes, double-V belts are recommended. Install guards around all moving parts in accordance with OSHA to
prevent personal injury.
Fasteners
Unless the pump has been shipped directly from the factory, it is recommended to check all bolts and nuts for tight-ness to eliminate possible
leakage problems or destructive vibration.
Pressure Relief
Discharge lines should be fitted with properly sized line pressure relief valves to protect both the pump and the system. Pumps equipped with
integral internal bypass relief valves are intended as a safety device against intermittent overpressurization. They are not designed for
continuous use and can lead to overheating. In these instances, a line pressure relief valve is required. The relief outlet should be piped back
to the suction vessel.