Viii. troubleshooting guide, Equipment service, Material safety data sheets – Spencer GasCube Natural Gas Booster Skid Package User Manual
Page 7: Emergency service, Service and operating assistance
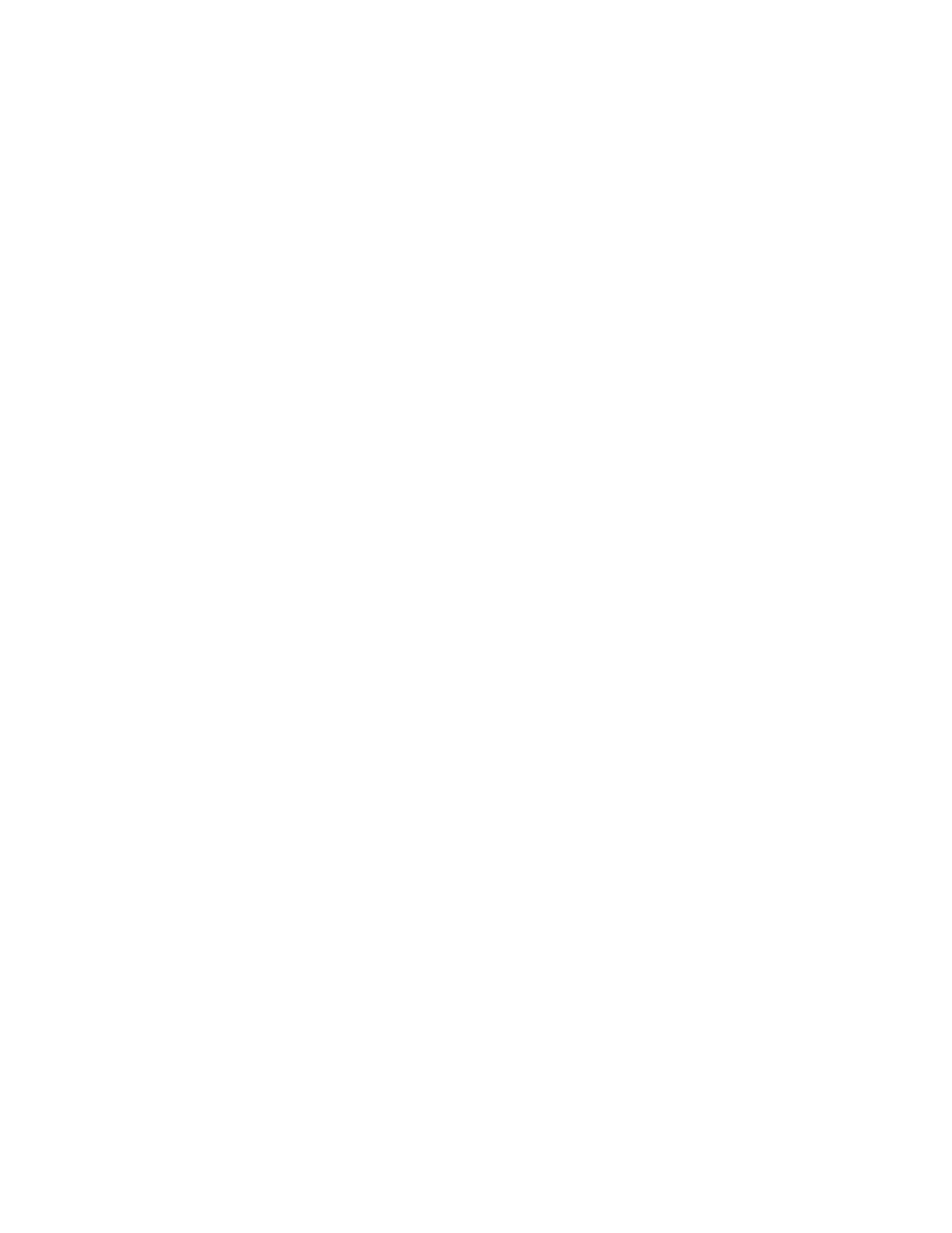
7
The Spencer Turbine Company
u
600 Day Hill Road, Windsor, CT USA 06095
u
TEL 800-232-4321
u
860-688-8361
u
www.spencerturbine.com
VIII. Troubleshooting
Guide
If your GasCube package is not delivering rated
pressure, but motor is not overloaded, check the
following:
1. Correct and reversed rotation will produce two differ-
ent delivery pressures, the higher pressure indicating
correct rotation.
2. Interior parts clogged with dirt.
3. Piping too small and causing high frictional loss (only
applies where pressure is checked at end of piping).
4. Lower specific gravity of gas than shown on nameplate.
5. High inlet gas temperature.
If your gas booster is not delivering rated pressure
and/or motor is overloaded, check the following:
1. Wrong voltage connections.
2. Unit handling more than rated volume because of:
Leaks in piping.
Orifices too large.
Too many orifices.
3. Higher specific gravity than on nameplate.
4. Intake gas temperature too low.
in unnecessary delays. When in doubt, consult the Spencer
Aftermarket Sales Department for further information.
When ordering parts, furnish the following:
• GasCube package serial and system numbers.
• Gas booster serial and model numbers.
• Motor horsepower.
• Part nomenclature — refer to the applicable diagram
(pages 8-14) and locate the needed item by its number
and name.
• Form number of this manual — Form GC
Equipment Service
Spencer provides prompt, courteous factory and field
service for all its machines. To determine the nature of the
disorder and the best way to correct it, service personnel
will be dispatched to your location. A Purchase Order in
advance will facilitate your service request; however, we
will proceed on verbal orders in an emergency.
Our service personnel will determine if your Spencer
warranty covers your required repairs. If the required work
is not covered, we accept Visa, MasterCard and American
Express charges as well as other forms of payment.
NOTE: Spencer products returned to the factory must be
sent freight prepaid and accompanied by a Return Service
Order (RSO) issued by the Spencer Service Department
after we receive your Purchase Order. Service costs will
be quoted after inspection and the work will be performed
upon written acceptance of the quotation.
Material Safety Data Sheets
Spencer is committed to ensuring the safety of its employ-
ees. If Spencer equipment has been exposed to potentially
hazardous contaminants or if Spencer service personnel
could be exposed to a potentially hazardous field environ-
ment, a Material Safety Data Sheet (MSDS) is required (a)
prior to dispatching Spencer service personnel or (b) before
receipt of any equipment for factory service. If special pre-
cautions are necessary to work on the equipment, contact
the Spencer Service Manager. Please be sure to have all
relevant Material Safety Data Sheets (MSDS) on hand for
Spencer’s reference during servicing and repairs.
Emergency Service
Emergency service calls after normal working hours are
routed through our voice mail system at 800-232-4321.
A Spencer service representative will return your call
promptly.
Service and Operating Assistance
Spencer representatives are always available to help
customers achieve maximum equipment performance
and reliability. Likewise, Spencer service personnel will
provide on-site instruction in proper procedures during
field service calls to avoid a recurrence of the problem
encountered.