Bell & Gossett S11574C Heat Transfer Package with Air Separation User Manual
Page 5
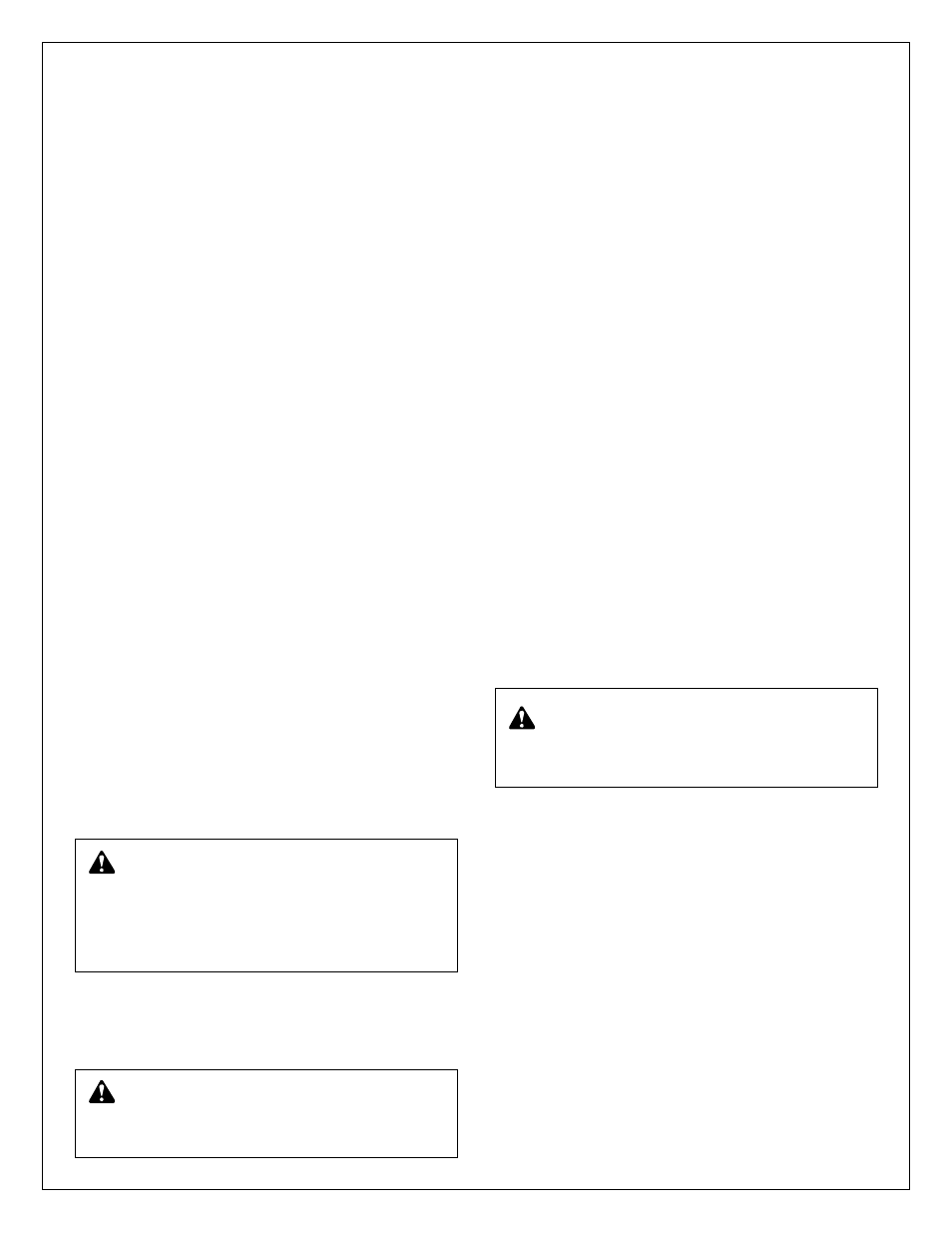
1.25
FIELD CONNECTION DIAGRAMS
1.26
Refer to the specific Installation, Operation, and
Maintenance Manuals for specific details unique to
each component. See the list below.
Component
IOM Part
(1) 1510 Pump
P81673
(2) Triple Duty Valve 2"–10"
V50960
(3) Triple Duty Valve 1"–1-1/2"
V50899
(4) ASME Safety Relief Valve
V55692
(5) Pressure Reducing Valve
V55999
(6) Air Separator, Airtrol Fitting,
ASME Compression Tank
S10300
(7) Enhanced Air Separator Model EAS A03852
(8) Vacuum Breaker
None
(9) High Capacity Air Valve #107A
A82003
(10) ASME Diaphragm
Pressurized Expansion Tanks
A01500
(11) Drain-O-Tank Air Charger
V56916
(12) Air Valve #87
None
(13) Heat Exchanger
HT-50A-SM
(14) Suction Diffuser
A91310
1.27
The following field connection diagrams should be
reviewed prior to unit installation and operation.
Drawing #
Description
Job Specific Print
Wiring
Job Specific Print
Dimensional Drawings
1.28
PIPING CONNECTIONS
1.29
A 3/4" NPT system fill connection is located in the
piping to the expansion tank. It is provided with a gate
valve and a pressure reducing valve with built-in
anti-syphon check valve. The reducing valve is set for
12 PSI system pressure. The PRV may be adjusted to
a higher setting when installed in taller buildings.
1.30
Local codes may govern this connection when made
to a domestic cold water line.
1.31
IMPORTANT: Do not install and operate Bell &
Gossett Pumps, 3D Valves, Suction Diffusers, etc., in
closed systems unless the system is constructed with
properly sized safety devices and control devices.
Such devices include the use of properly sized and
located pressure relief valves, compression tanks,
pressure controls, temperature controls and flow con-
trols as appropriate. If the system does not include
these devices, consult the responsible engineer or
architect before making pumps operational.
2.0
INSTALLATION INSTRUCTIONS
2.1
Location
2.2
Locate the pumping unit for ease of inspection, main-
tenance and service.
2.3
Leveling
2.4
Place the unit on its concrete foundation, supporting
it with steel wedges or shims.
2.5
Grouting
2.6
After the frame has been leveled and securely bolted
to the floor, a good grade of grout should be installed
beneath the base. A suggested mixture for grout is
one part Portland Cement and two or three parts
plain, sharp sand mixed with water until it will pour
easily. Commercial grout mixtures with suspended
iron particles are available. Wet the concrete base
before pouring grout. To hold wedges or shims in
place, allow the grout to flow around them and
beneath the entire length of the base flange.
2.7
Piping
2.8
Be sure to eliminate any pipe strain on the unit.
Support the pipes independently by use of pipe
hangers near the unit. Line up the vertical and hori-
zontal piping so that the bolt holes of the flanges
match. DO NOT ATTEMPT TO SPRING THE PIPE
LINES INTO POSITION. The code for Pressure Piping
(A.S.A.B. 31.1) lists many types of supports available
for various applications.
2.9
As a rule, ordinary wire or band hangers are not ade-
quate to maintain alignment. It is very important to
provide a strong, rigid support for the suction line. A
saddle hanger is recommended.
2.9.1
For critical installations, equipment for absorbing
expansion and vibration should be installed in the inlet
and outlet connections of the unit.
2.9.2
Inspect all piping connections. Joints may become
loose during transit due to vibration and shock. All
joints are to be checked for tightness. Flanged joints
should be checked for proper torque of all flange bolts
prior to filling the system with fluid.
2.9.3
Hot Water Supply Connection
2.10
The supply main may be connected directly to the
B&G Triple Duty Valve mounted on the pump dis-
charge nozzle. In some installations, a flexible con-
nector near the Triple Duty valve may be desirable.
2.11
Hot Water Return Connection
2.12
The return connection is made to the top opening of
the 2 pass heat exchanger head. The return piping
should approach the head such that a union or
flanged joint can be placed in the section of the pip-
ing which is at a right angle to the length of the heat
exchanger. This will allow easy removal of the head
the tube bundle without pipe interference.
2.13
Install a thermometer in the return line near the heat
exchanger.
2.14
Both supply and return mains should be piped so as
to prevent air trapping. All high points in the piping
system should be provided with manual vents to
remove excess air during initial fill. Automatic air vents
must not be used in locations where the system pres-
sure may fall below atmospheric while pumping.
5
WARNING: The heating of water and other fluids
causes volumetric expansion. The associated
forces may cause failure of system components and
release of high temperature fluids. This will be prevented
by installing properly sized and located pressure relief
valves and compression tanks. Failure to follow these
instruction could result in serious personal injury, death,
and/or property damage.
WARNING: Heavy load may drop if not lifted
properly. Do not lift the entire unit by the motor eye-
bolts. Lift the unit with slings placed under unit base rails.
Failure to follow these instructions could result in seri-
ous personal injury, death, and/or property damage.
CAUTION: Failure to check all joints for tightness
and flange bots for proper torque could result in
leaks and/or flooding. Failure to follow these instructions
could result in property damage and/or moderate per-
sonal injury.