Analytical Industries GPR-1200 ATEX Portable Trace PPM Oxygen Analyzer User Manual
Page 30
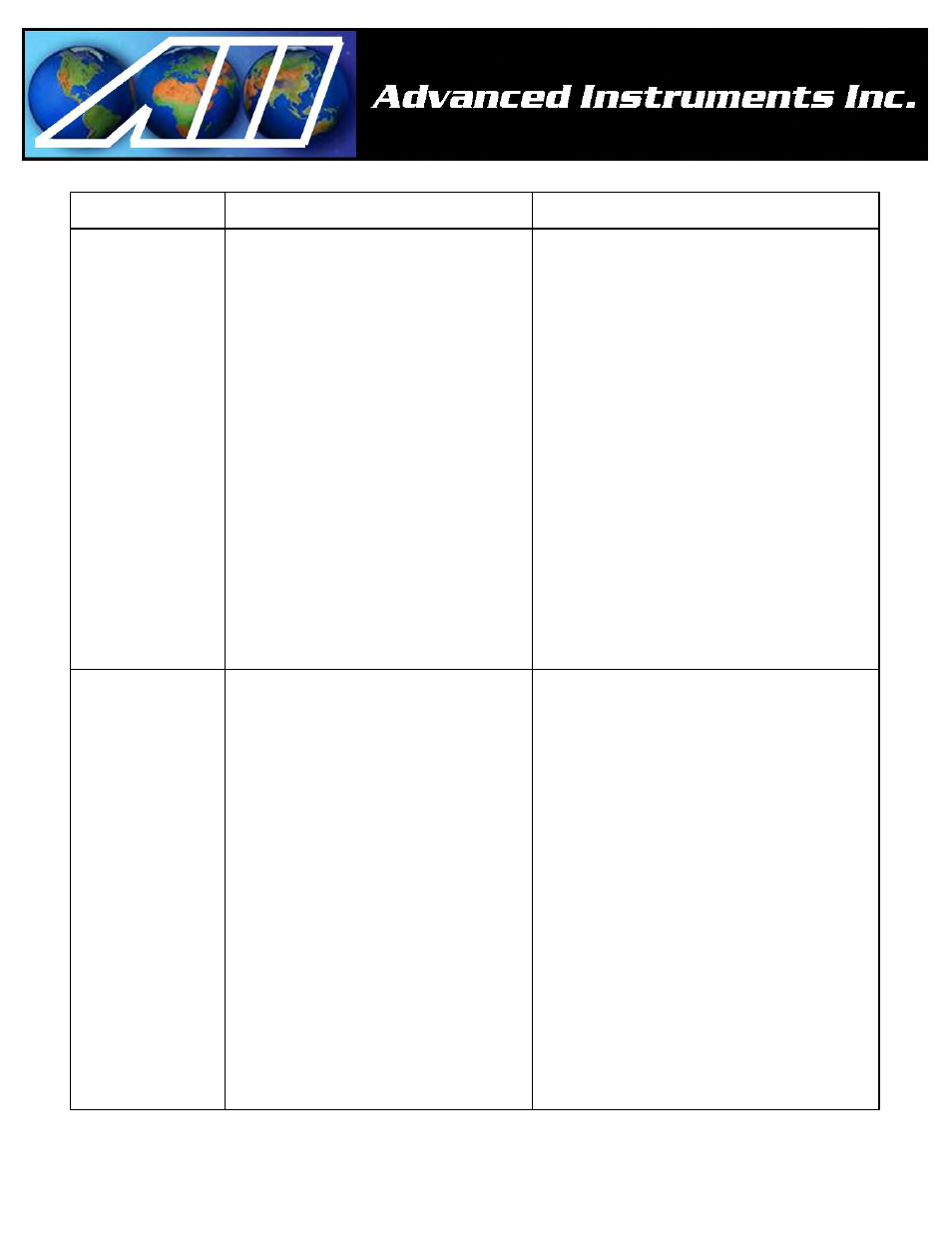
30
Symptom
Possible Cause
Recommended Action
Erratic O
2
reading
or
No O
2
reading
Test sensor independent from analyzer
Change in sample pressure
Dirty electrical contacts in upper section of
sensor housing
Corroded solder joints on sensor PCB from
corrosive sample or electrolyte leakage from
sensor
Corroded spring loaded contact in upper
section of sensor housing from liquid in
sample or electrolyte leakage from sensor
Liquid covering sensing area
Improper sensor selection
Presence of interference gases
Presence of sulfur gases
Unauthorized maintenance
Sensor nearing end of life
Remove sensor from housing. Using a volt-meter set
to uA output; apply the (+) lead to the outer ring of
the sensor PCB and the (-) lead to the center circle
to obtain the sensor’s output in air. Contact factory
with result.
Sensors without PCB use mV setting.
Calibrate the analyzer (calibrate at pressure and
temperature of sample)
Clean contacts with alcohol (minimize exposure time
of MS sensor to ambient air to extent possible)
Replace sensor and return sensor to the factory for
warranty determination
Upper section of sensor housing: Clean contacts with
alcohol, flow sample or zero gas for 2-3 hours to
flush sample system and sensor housing
Sensor: Replace if leaking and return it to the factory
for warranty determination
Wipe with alcohol and lint free towel or flow sample
or zero gas for 2-3 hours to flush
Replace GPR/PSR sensor with XLT sensor when CO
2
or acid gases are present
Consult factory
Replace sensor and install scrubber
Replace sensor, obtain authorized service
Replace sensor
Erratic O
2
reading
or
Negative O
2
reading
or
No O
2
reading
possibly
accompanied by
electrolyte leakage
Pressurizing the sensor by flowing gas to the
sensor with:
the vent restricted or
SHUT OFF valve closed
and
suddenly removing the restriction draws a
vacuum on the sensor
or
partially opening the valves upstream of the
analyzer when using a pump downstream of
the analyzer to draw sample from a process at
atmospheric pressure or a slight vacuum
A pressurized sensor may not leak but still
produce negative readings.
Placing a vacuum on the sensor in excess 4”
of water column is strongly discouraged.
The front sensing membrane is .000625 thick,
heat sealed to the sensor body and subject to
tearing when vacuum is suddenly applied.
A premature adjustment of the ZERO OFFSET
potentiometer is a common problem
Zero the analyzer. If not successful replace the
sensor
Avoid drawing a vacuum on the sensor
From MAIN MENU select DEFAULT ZERO