Equa 2 lecture seating specifications – Theatre Solution Lecture Seating Equa 2 User Manual
Page 3
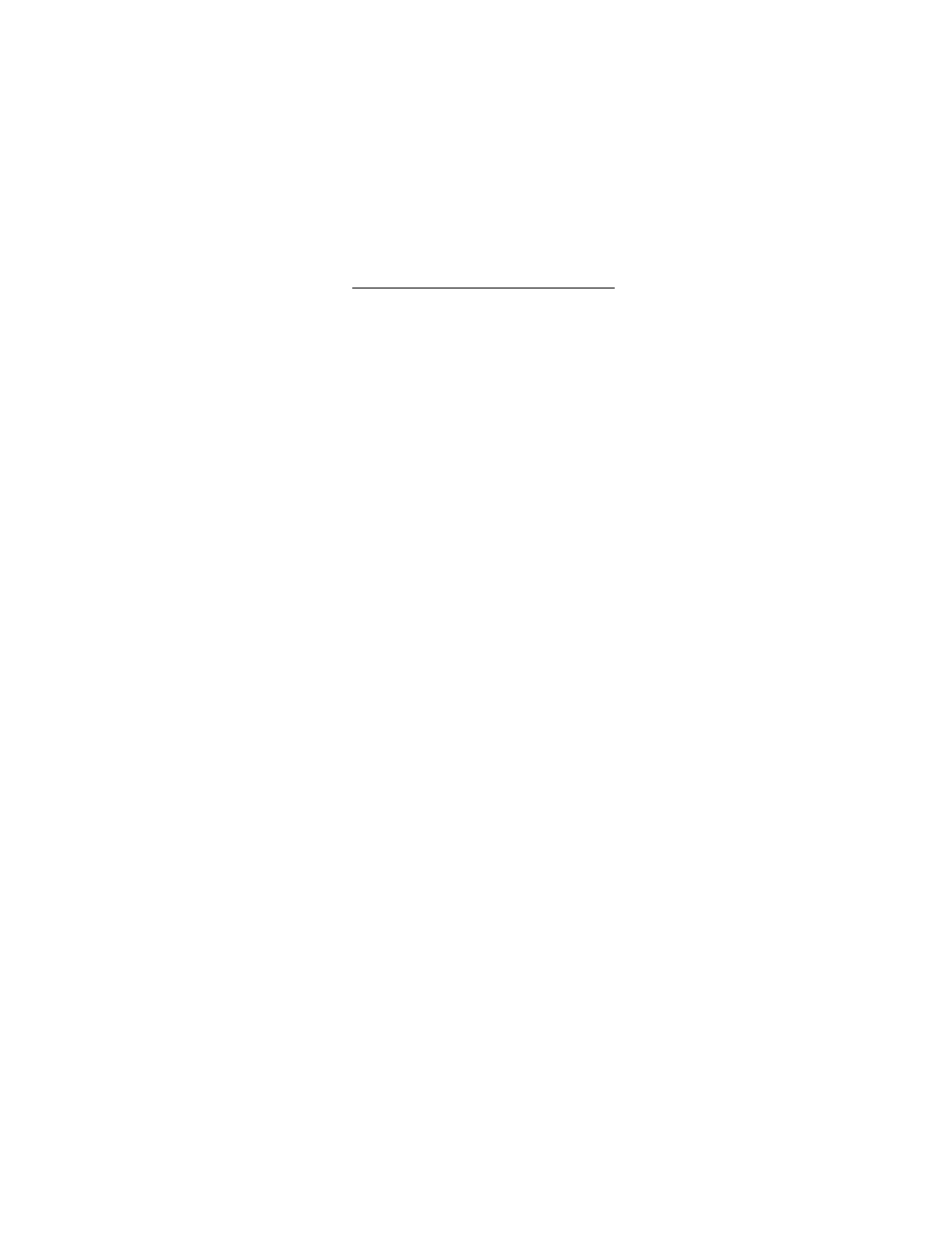
Equa 2 Lecture Seating Specifications
Page 3 of 5
held in place with injection molded polycarbonate fasteners spin welded to the outer shell and shall snap on
and off for replacement.
E. Chair shall include a knee-tilt mechanism with a tilt tension adjustment.
F. Chair shall conform to CAL 117 requirements.
2.7 WORKSURFACES
A. Tables are to be a 3-ply warp resistant construction with a core of 1-1/8” thick 45-50 lb. density particle
board, a 0.020” Kraft backer sheet, and a face material of 0.030” high-pressure laminate.
B. The edge detail is to be (select one edge detail from the list below)
1.
3mm PVC – 3mm x 1-1/4” PVC on all table edges that would be exposed after installation, with a 1/8”
radius on the top and bottom edges. The table corners are square with an overlap joint.
2.
3mm Hardwood – 3mm x 1-1/4” hardwood on all table edges that would be exposed after installation,
with 1/8” radius on the top and bottom edges, finished to match the architect’s sample. The table
corners are square with an overlap joint.
3.
Bevel – 3/4” x 1-1/4” solid hardwood on all table edges that would be exposed after installation, with a
3/8” x 45 degree bevel detail along the top edge, finished to match the architect’s sample. The table
corners are mitered.
4.
Chamfer – 3/4” x 1-1/4” solid hardwood on all table edges that would be exposed after installation, with
a 1/4” radius on the top edge blending into a 60 degree backcut chamfer edge detail, finished to match
the architect’s sample. The table corners are mitered.
5.
Bullnose – 3/4” x 1-1/4” solid hardwood on all table edges that would be exposed after installation, with
a full 5/8” radius bullnose edge detail, finished to match the architect’s sample. The table corners are
mitered.
PART 3 – OPTIONS
3.1 WORKSURFACES
A. Tables are to be a 3-ply warp resistant construction with a core of 1-1/8” thick 45-50 lb. density particle
board, a 0.020” Kraft backer sheet, and a face material of veneer. The grain is to run the length of the
worksurface.
3.2 MODESTY
PANELS
A. Straight modesty panels are to be a 3-ply warp resistant construction with a core of 5/8” thick 45-50 lb.
density particle board. The face surfaces are to be 0.030” high-pressure laminate. On laminates with a
wood grain, the grain is to run horizontally.
B.
Straight modesty panels are to be a 3-ply warp resistant construction with a core of 3/4” thick 45-50 lb.
density particle board. The face surfaces are to be veneer; the grain is to run horizontally.
C.
Curved modesty panels are to be 3/8” thick medium density fiberboard with a 1/2” thick x 1” wide birch
plywood strip affixed to the bottom edge. The face surfaces are to be 0.030” high pressure laminate. On
laminates with a wood grain, the grain is to run horizontally.
D.
Curved modesty panels are to be 3/8” thick medium density fiberboard with a 1/2” thick x 1” wide birch
plywood strip affixed to the bottom edge. The face surfaces are to be veneer; the grain is to run
horizontally.
3.3 END
PANELS
A. End panels are to be a 3-ply warp resistant construction with a core of 1-1/8” thick 45-50 lb. density particle
board. The face surfaces are to be 0.030” high-pressure laminate.
B. The vertical edges are to be self-edged.
3.4 ARMS
A. Arms shall be capable of being added or removed on-site. Arms shall have a T-style armpad support of
die-cast aluminum. Armpad shall be blow-molded, textured, low durometer polyvinyl chloride (PVC)
injected with polyurethane foam.
3.5 ELECTRICAL SYSTEM/DATA WIRE MANAGEMENT
A. Provide manufacturers standard modular electrical system for power distribution. All electrical modules
shall be manufactured from BX cable or liquid-tight BX cable, and shall have molded end connectors. The