Planar a1 specifications – theatre seating – Theatre Solution Planar A1 User Manual
Page 3
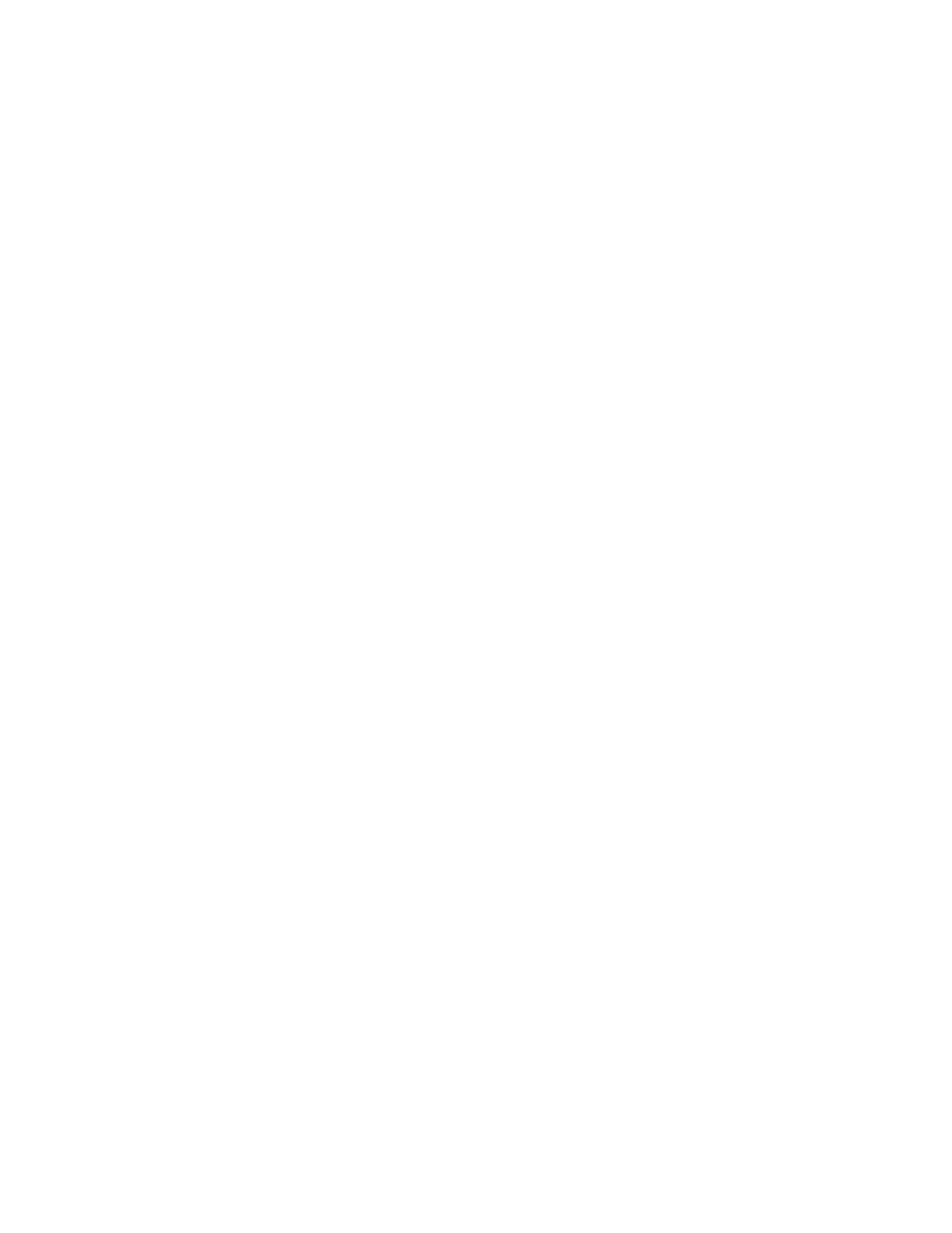
Planar A1 Specifications – Theatre Seating
Page 3 of 3
B.
Seat Construction: Solid seat bottom construction comprised of a plywood veneer outer panel fastened
solidly and without voids to an inner structural plywood panel. The outer panel shall be 15mm thick, faced
one side with Grade A veneer, and exposed plywood laminations along all edges. The inner panel shall be
3/4” thick. Both shall be electronically glued hardwood plywood and shall be fastened together with
bayonet hanging brackets at the top and two steel angles at the bottom, resulting in a rigid connection with
no visible fasteners. The veneer face and edges of the outer panel shall be stained to match the architect’s
sample. The padding shall be a fabricated assembly of urethane foam components, shall be glued to the
inner panel, and shall conform to the California Bureau of Home Furnishings Technical Bulletin 117. The
complete seat assembly shall be supported by two 7 gauge formed steel mounting brackets which will
attach the seat assembly to the hinges on the standards. The seat shall have a built-in counterweight to
insure automatic self-rising without the aid of springs. Arch-spring seat construction will not be acceptable.
C.
Back Construction: Solid back construction comprised of a plywood veneer outer panel fastened solidly and
without voids to an inner structural plywood panel. The outer panel shall be 15mm thick, faced one side
with Grade A veneer, and exposed plywood laminations along all edges. The inner panel shall be 1/2”
thick. Both shall be electronically glued hardwood plywood and shall be fastened together with bayonet
hanging brackets at the top and two 1/4-20 x 1-1/8” Allen-drive low-profile bolts at the bottom, resulting in a
rigid connection with no visible fasteners on the outer wood panel. The veneer face and edges of the outer
panel shall be stained to match the architect’s sample. The padding shall be a fabricated assembly of
urethane foam components, shall be glued to the inner panel, and shall conform to the California Bureau of
Home Furnishings Technical Bulletin 117. The complete back assembly shall be supported by two 13
gauge formed steel brackets and two 3/8-16 hex head bolts which will attach the back assembly to the
standards.
D.
Armrests: Shall be kiln-dried solid hardwood, nominally 13/16” thick x 2-1/4” wide x 11-3/4” long, stained to
match the outer seat and back panels. The armrest will be fastened to the steel frame with four #8 x 5/8”
pan head sheet metal screws. Chairs equipped with tablet arms shall have armrests nominally 13/16” thick
x 2-1/4” wide x 17-5/8” long and shall be attached to the steel frame arm support with four #8 x 5/8” pan
head sheet metal screws.
E.
Hinge: The seat hinge shall be a weldment consisting of a 7 gauge hot-rolled pickled-in-oil steel component
and shall be formed and punched to receive a 0.56” id x 0.75” od x 0.5” long steel bushing. A self-
lubricating nylon sleeve shall be fitted between the seat hinge and the standard seat hinge pin. The hinge
shall be machined to provide a positive stop location for the seat in both occupied and unoccupied
positions. The hinge shall be fitted with a plastic cover to eliminate all pinch points and shall include a
3/16” thick urethane rubber pad to dampen noise upon the seat return to the vertical position.
PART 3 – OPTIONS
3.1 END
PANEL
A. Provide manufacturer’s standard end panel at the end of the row. The configuration of the panel shall
follow the angle of the frame and back at the rear, and shall be vertical at the front end. The panel shall be
constructed of 3/4” thick plywood with veneer on both sides and 1/8” thick solid wood on the vertical edges.
The end panel shall be stained to match the outer wood seat, back, and armrests.
3.2 AISLE LIGHT
A. Aisle lights shall be provided in accordance to the locations shown on the architectural drawings. The units
shall be of low voltage (24v) type and the light tube shall fit into a routed area on the underside of the
armrest. The chair frame shall be prepared to accept the power wire. The necessary access holes and
blank cover plates shall be provided. The chair manufacturer shall also provide the necessary
transformers. All wiring and electrical connections shall be conducted at the job site and shall be the
responsibility of others.
3.3 HARDWOOD EDGES, OUTER SEAT AND BACK
A. Outer plywood panels shall be trimmed in 1/8” thick hardwood on the top and vertical edges. The
hardwood shall match the face veneer species and be stained to match.
3.4 INSET UPHOLSTERY, BACK
A. Back upholstery shall be inset to expose the veneer face on the inside of the outer back panel. The veneer
on the inside face on the back panel shall match the veneer species on the outside face and be stained to
match.