Tier specifications – loose seating – Theatre Solution Tier Specifications User Manual
Page 2
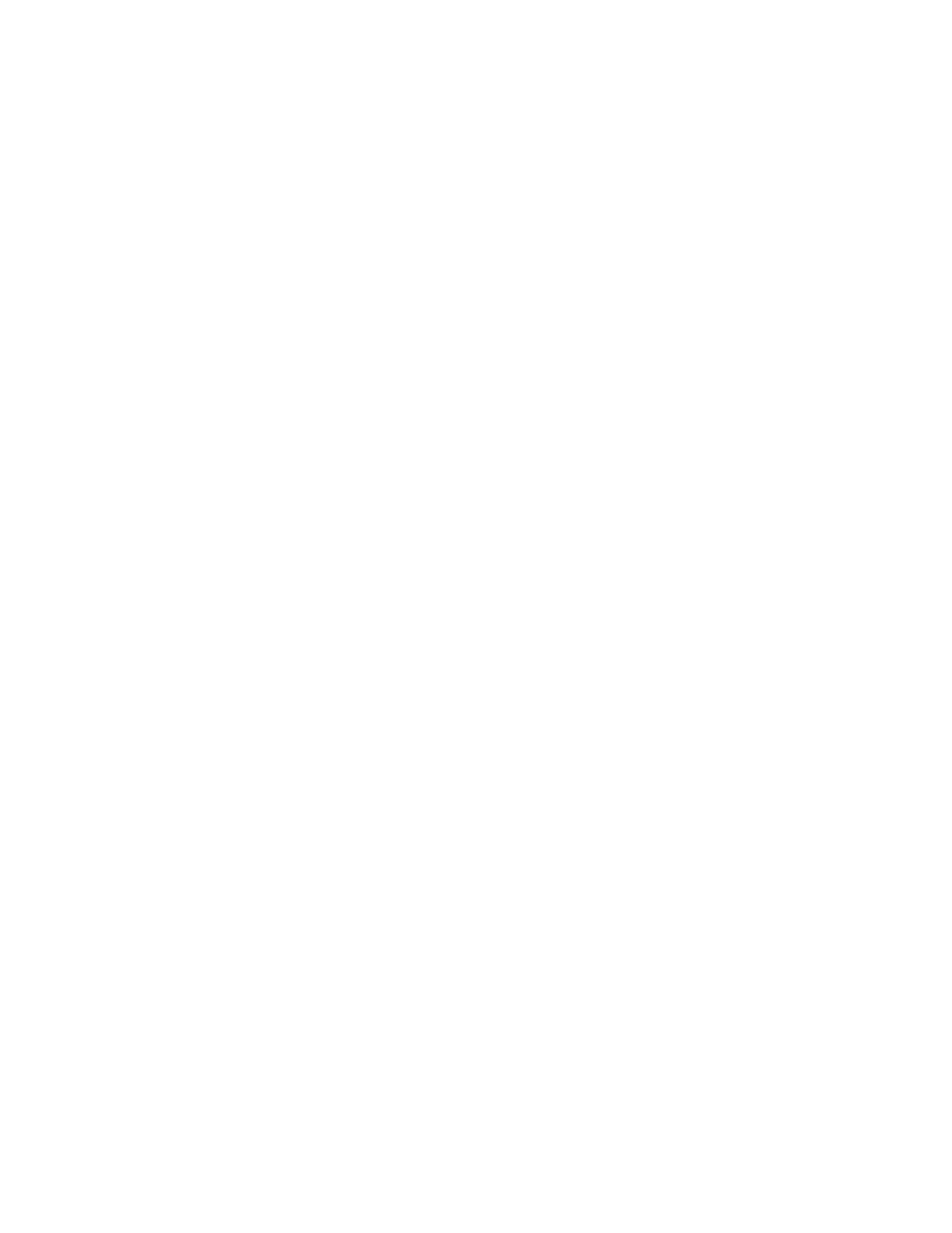
Tier Specifications – Loose Seating
Page 2 of 3
2.2 MATERIALS
A. Padding material shall be high resiliency polyurethane foam, which conforms to the standards of the
California Bureau of Home Furnishings 117-75. The back shall be 3/4” thick. The seat shall be 1-1/2”
thick.
B.
Seating fabric shall be _______________________________________________ with the color to be
selected from the standard choice of colors. All upholstery shall be first quality without creases, stretch
lines, or wrinkles.
C. The frame shall be solid wood. All wood shall be stained in any of the manufacturer’s standard finishes.
2.3 FABRICATION,
GENERAL
A. General: Fabricate the loose seating in contoured form for maximum comfort using materials which are
carefully selected to be free from defects, objectionable projections, or irregularities. Smooth round corner
and edges to present the least possible snagging and pinching hazards.
B.
Construction
1. All frame joints are mortise and tenon construction, assembled with glue, and clamped for a
minimum of 4 hours.
2. The front legs are 1-1/16” x 1-5/8” and are joined to the seat rails with a mortise and tenon joint.
3. The rear legs are 1-1/16” x 1-5/8” and are joined to the seat rails with a mortise and tenon joint.
4. The side seat rails are 7/8” x 2-1/4”. The front seat rail is 7/8” x 2-1/2” and shall be profiled to
include a 46” radius along the bottom edge. The rear seat rail is 1-1/2” x 2-1/4” and is shaped to
conform to a 24” back radius. All seat rails are machined to receive blocking for support of the
webbed seat panel.
5. Arms are 1-1/8” x 1-7/8” and are shaped to notch around the rear frame legs. The arms shall
include a 3” R.O.C. shaped top surface and shall be attached to the front and rear legs with a
mortise and tenon joint.
6. The back top rail is 1-1/16” x 1-7/16” and is shaped in a compound curve and joined to the rear
legs with a mortise and tenon joint.
7. Corner blocks are grooved to fit into the grooves in the side rails and are counter-bored to allow
for the attachment of the seat panel to the frame.
8. The upholstered seat is 3/4” MDF and is machined to match the shape of the chair frame. The
seat panel is double webbed with 2” pre-stressed webbing. The seat padding is 1-1/2” thick fire
retardant polyurethane foam.
9. The upholstered back consists of two pieces of 3/8” thick 7 ply electronically glued hardwood
plywood. The inside back padding is 3/4” thick fire retardant polyurethane foam. The outside
back padding is 1/4” thick fire retardant polyurethane foam. The outside back panel is attached to
the frame with four 16 gauge steel angles. The inside back panel is attached to the outer back
panel with two bayonet hanging brackets.
C.
Assembly: The chair frame is assembled with aliphatic resin glue and clamped to allow total curing of the
joints. All excess glue residue is to be removed prior to hardening. Corner blocks are to be glued in place
during assembly to insure a square and plumb assembly.
D.
Finishing: All surfaces are to be sanded with a series of sandpaper starting at 120 grit and finishing with a
white wood sanding at 220 grit. All sharp edges shall be smoothed, all machining and tool marks are to be
removed, and the affected areas blended into the surrounding areas. All surfaces are to be stained and
sealed. Prior to the final topcoat, a light sanding with 320 grit sandpaper to remove foreign particles from
the sealer coat is to be performed. A final topcoat of catalyzed lacquer is to be applied to all exposed
surfaces.
PART 3 – WARRANTY
3.1 The loose seating manufacturer must provide a one-year warranty to the original purchaser of the seating as
follows:
A. The seating manufacturer shall warrant its products against failures and manufacturing defects for one
year. This warranty applies to the original purchaser and is non-transferable. The seating manufacturer
will provide parts and labor to replace defective parts for one year after the date of shipment.