3B Scientific Stirling Engine G User Manual
Page 6
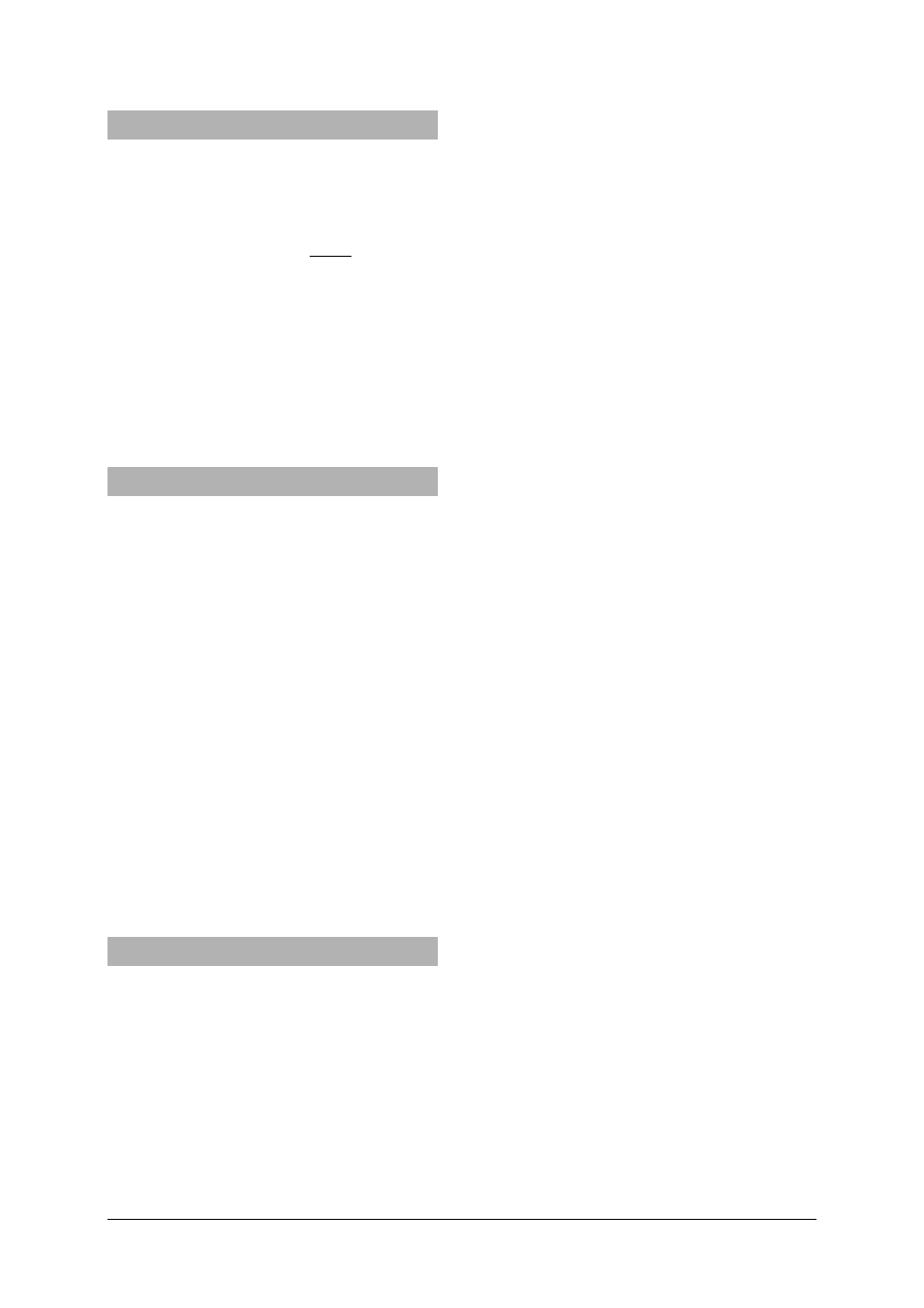
2
3. Technical data
Motor-generator unit:
max. 12 V DC
2-stage pulley:
30 mm dia., 19 mm dia.
Working piston:
25 mm dia.
Path of working piston:
24 mm
Volumetric change: 24 mm
3
12
2
25
cm
mm
=
π
⋅
⎟
⎠
⎞
⎜
⎝
⎛
Minimum volume:
32 cm³
Maximum volume:
44 cm³
Power of the
Stirling motor:
1 W approx.
Dimensions: 300x220x160
mm³
ap-
prox.
Weight:
1.65 kg approx.
4. Functioning principle
An ideal Stirling cycle has 4 phases (refer to Fig. 1):
Phase 1: Isothermal change of state, during which
the air expands at constant temperature.
Phase 2: Isochoric change of state, during which
the air cools at constant volume in the re-
generator.
Phase 3: Isothermal change of state, during which
the air is compressed at constant tempera-
ture.
Phase 4: Isochoric change of state, during which
the air in the regenerator is heated back to
its initial temperature.
However, the Stirling motor is not capable of
achieving this ideal behaviour. The phase shifts
between the working piston and displacement
piston only allow an approximation of the ideal
process, the 4 different phases exhibiting a certain
degree of overlap: Already during expansion, the
gas temperature changes from hot to cold, and
when compression begins, some of the air has not
yet reached the cold part of the motor.
5. Operation
5.1 The Stirling Engine as a heat engine
•
Fill the methylated-spirit burner, place it in the
recess in the base-plate, twist out about 1-2
mm of the wick, and ignite it.
•
Move the displacer piston to its farthest-back
position, and after a short heating-up time
(about 1-2 minutes) push the flywheel gently in
the clockwise direction (as seen from the mo-
tor-generator unit) to set it turning (see Fig. 2).
•
If necessary, adjust the tension of the drive belt
by moving the motor-generator unit.
•
Turn on the filament lamp by moving the
switch to the “up” position.
•
Alternatively, connect an external load through
the 4 mm sockets and drive it by moving the
switch to the “down” position.
Speed without a load:
1000 rpm approx.
Speed with a generator
as the load:
650 rpm approx.
Generator voltage:
6 V DC approx.
Pressure difference:
+250 hPa / -150 hPa
5.2 The Stirling motor as a heat pump or refrig-
erator
Additional instruments needed:
DC Power supply 15 V, 1.5 A
U8521121-115
or
DC Power supply 15 V, 1.5 A
U8521121-115
Digital thermometer
U11818
•
Insert temperature sensors into the thermome-
ter sockets and connect them to a measuring
instrument (see fig. 3).
•
Connect a DC voltage source through the 4 mm
sockets.
•
Adjust the voltage (maximum 12 V) and oper-
ate the Stirling engine with the switch in the
“down” position.
•
Observe the increase or reduction in tempera-
ture.
In the refrigerator mode of operation, the flywheeI
rotates in the clockwise direction (as seen from the
motor-generator unit), whereas in the heat pump
mode it rotates in the anticlockwise direction.
•
To switch between the two modes of operation,
reverse the polarity of the connections.
Pressure difference:
+250 hPa / -150 hPa
Motor voltage:
9 V
Speed: 600
rpm
Temperature difference (with respect to 21° C):
Refrigerator:
-4 K (reservoir: +6 K)
Heat pump:
+13 K (reservoir: -1 K)
5.3 Recording the operating pressure on the
work piston
Additional instruments needed:
3B NETlog
TM
U11300
3B NETlab
TM
U11310
Relative pressure sensor, ±1000 hPa
U11322
•
Connect a pressure hoses between the “posi-
tive” hose connector of the sensor box and the
hose connector on the work cylinder (see fig.
4).
•
Connect the pressure sensor to the 3B NETlog
TM
.
•
Start the program software and carry out the
measurements.