Applications information – Rainbow Electronics MAX15023 User Manual
Page 23
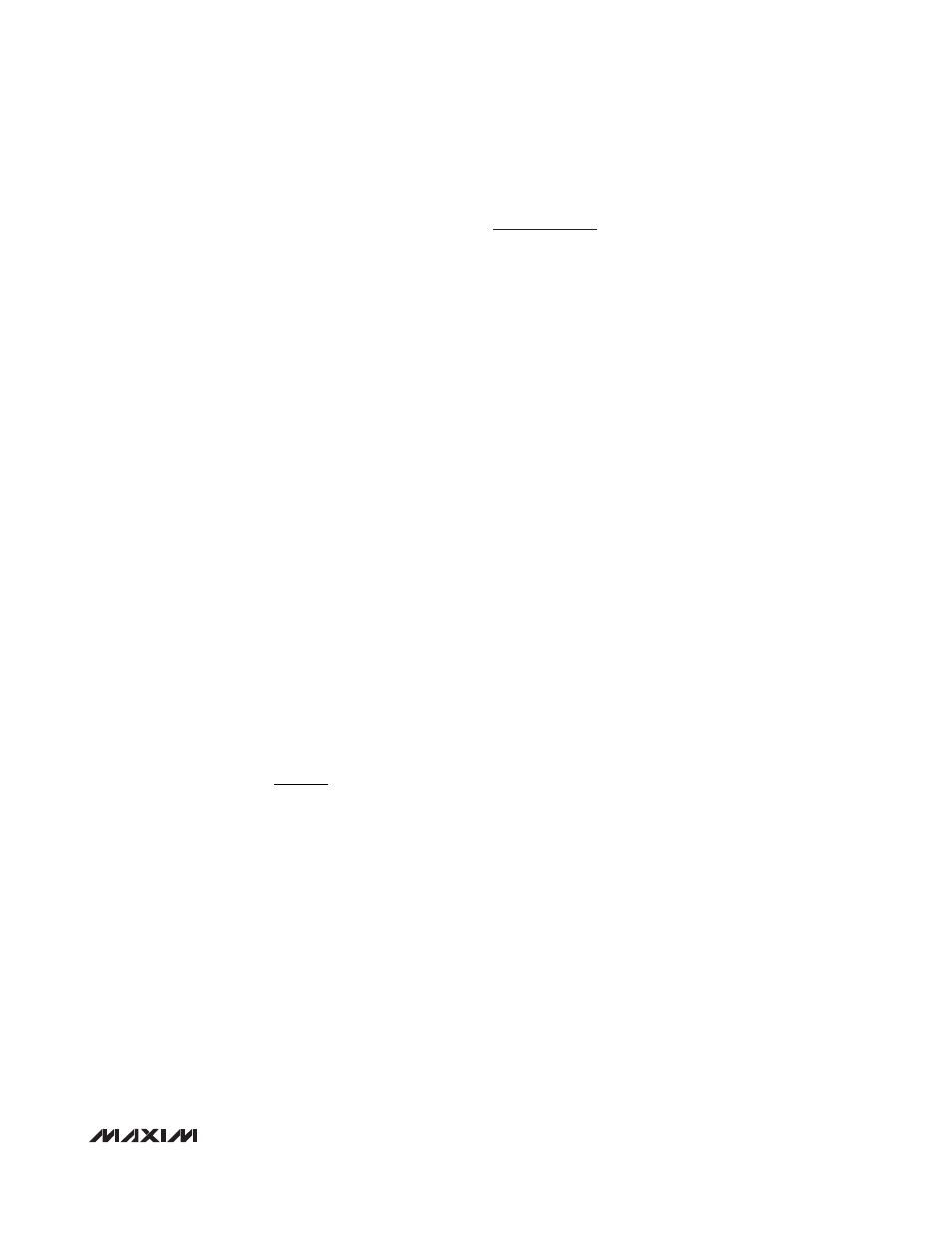
MAX15023
To estimate the temperature rise of the die, use the fol-
lowing equation:
T
J
= T
A
+ (P
T
x
θ
JA
)
where
θ
JA
is the junction-to-ambient thermal resistance
of the package, P
T
is power dissipated in the device,
and T
A
is the ambient temperature. The
θ
JA
is 36°C/W
for the 24-pin TQFN package on multilayer boards, with
the conditions specified by the respective JEDEC stan-
dards (JESD51-5, JESD51-7). If actual operating condi-
tions significantly deviate from those described in the
JEDEC standards, then an accurate estimation of the
junction temperature requires a direct measurement of
the case temperature (T
C
). Then, the junction tempera-
ture can be calculated using the following equation:
T
J
= T
C
+ (P
T
x
θ
JC
)
Use 3°C/W as
θ
JC
thermal resistance for the 24-pin
TQFN package. The case-to-ambient thermal resis-
tance (
θ
CA
) is dependent on how well the heat is trans-
ferred from the PCB to the ambient. Therefore, solder
the exposed pad of the TQFN package to a large cop-
per area to spread heat through the board surface,
minimizing the case-to-ambient thermal resistance. Use
large copper areas to keep the PCB temperature low.
Boost Flying-Capacitor Selection
The MAX15023 uses a bootstrap circuit to generate the
necessary gate-to-source voltage to turn on the high-
side MOSFET. The selected n-channel high-side MOS-
FET determines the appropriate boost capacitance
values (C
BST_
in
Typical Application Circuits
) according
to the following equation:
where Qg is the total gate charge of the high-side
MOSFET and
∆V
BST_
is the voltage variation allowed on
the high-side MOSFET driver after turn-on. Choose
∆V
BST_
such that the available gate drive voltage is not
significantly degraded (e.g.,
∆V
BST_
= 100mV to
300mV) when determining C
BST_
. The boost flying-
capacitor should be a low-ESR ceramic capacitor. A
minimum value of 100nF is recommended.
Applications Information
PCB Layout Guidelines
Make the controller ground connections as follows: cre-
ate a small analog ground plane near the IC or use a
dedicated internal plane. Connect this plane to SGND
and use this plane for the ground connection for the IN
bypass capacitor, compensation components, feed-
back dividers, RT resistor, and LIM_ resistors.
If possible, place all power components on the top side
of the board, and run the power stage currents (espe-
cially the one having large high-frequency components)
using traces or copper fills on the top side only, without
adding vias.
On the top side, lay out a large PGND copper area for
the output of channels 1 and 2, and connect the bottom
terminals of the high-frequency input capacitors, output
capacitors, and the source terminals of the low-side
MOSFETs to that area.
Then, make a star connection of the SGND plane to the
top copper PGND area with few vias in the vicinity of
the source terminal sensing. Do not connect PGND and
SGND anywhere else. Refer to the MAX15023
Evaluation Kit data sheet for guidance.
Keep the power traces and load connections short,
especially at the ground terminals. This practice is
essential for high efficiency and jitter-free operation. Use
thick copper PCBs (2oz vs. 1oz) to enhance efficiency.
Place the controller IC adjacent to the synchronous rec-
tifier MOSFETs (NL _) and keep the connections for
LX_, PGND_, DH_, and DL_ short and wide. Use multi-
ple small vias to route these signals from the top to the
bottom side. The gate current traces must be short and
wide, measuring 50 mils to 100 mils wide if the low-side
MOSFET is 1in from the controller IC. Connect each
PGND trace from the IC close to the source terminal of
the respective low-side MOSFET.
Route high-speed switching nodes (BST_, LX_, DH_,
and DL_) away from the sensitive analog areas (RT,
COMP_, LIM_, and FB_). Group all SGND-referred and
feedback components close to the IC. Keep the FB_
and compensation network nets as small as possible to
prevent noise pickup.
C
Qg
V
BST
BST
_
_
=
∆
Wide 4.5V to 28V Input, Dual-Output
Synchronous Buck Controller
______________________________________________________________________________________
23