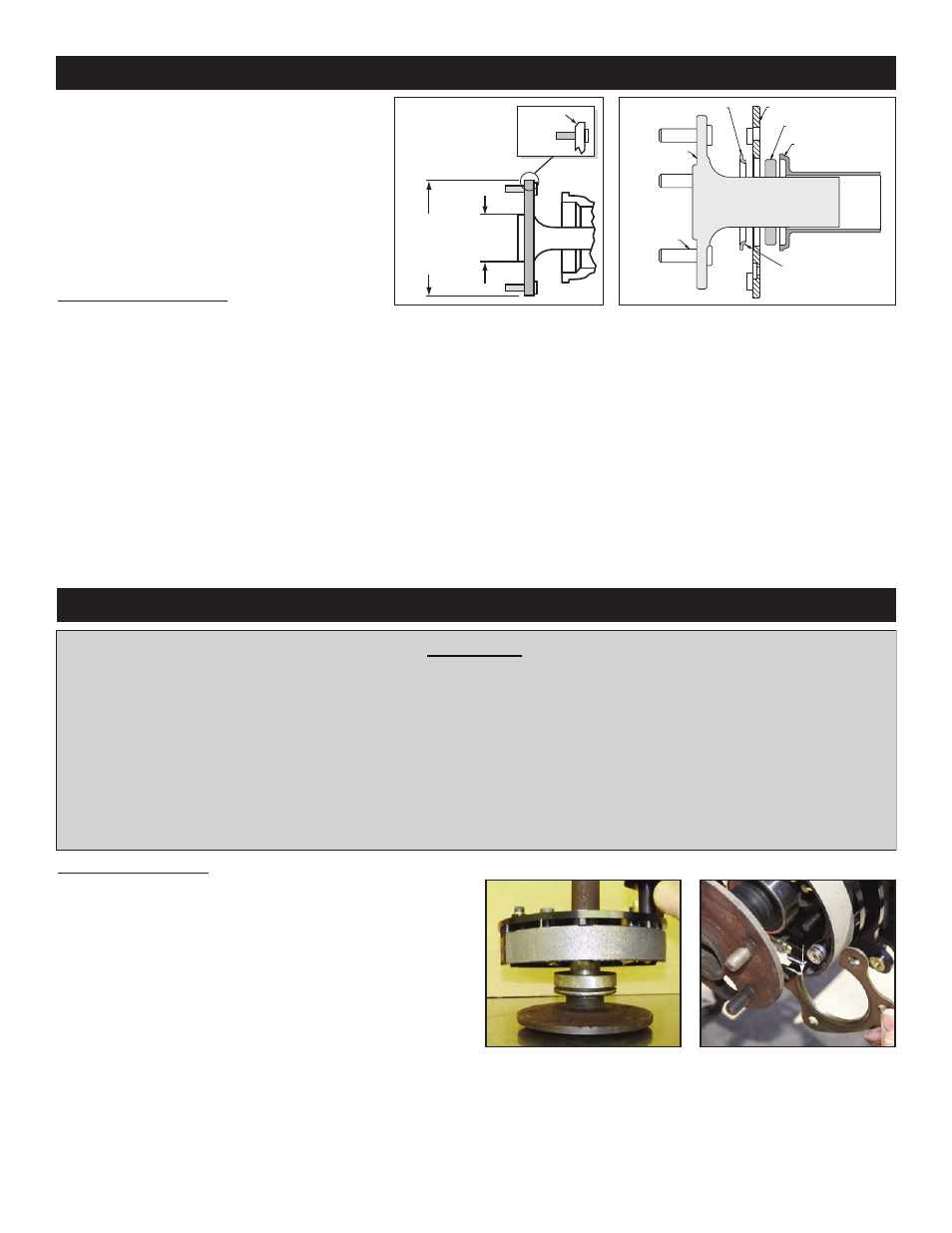
NOTE: Some OEM axles have 7/16” (0.44”)
wheel axle studs. It is recommended that you
upgrade to 1/2” studs. Dependent on the type
of axle, this may be a simple stud change, or
may require the services of a machine shop to
perform.
• Maximum axle flange diameter must be no larger
than 6.61” w/.050” x 45° chamfer, Figure 3.
Disassembly Instructions:
•Disassemble the original equipment rear brakes:
Raise the rear wheels off the ground and
support the rear suspension according to the
vehicle manufacturer’s instructions.
Remove the rear wheels and disassemble the drum brake assembly down to the bare axle.
Remove the stock bearing retainers from the axles.
• Remove any nicks or burrs on the axle housing flange, as well as the axle flange, that may interfere with the installation of the new
brake components.
• Clean and de-grease the axle and axle housing flange.
Assembly Instructions (numbers in parenthesis refer to the parts list, and Figure 1 on the preceding pages): CAUTION: All mounting
bolts must fully engage clinch nuts. Be sure to check that all bolts
are either flush or protruding through flanged side of clinch nut
after shimming, Figure 5.
•Orient the bracket assembly (1) as shown in Figure 1 and Photo
1 and slide it onto the axle. Insert the axle and bracket into the
axle housing. Ensure that the bracket assembly backing plate
fits flush against the axle housing flange.
•Install the bearing retainer (2) with the opening pointing upward
and the lip facing inward (toward the bearing), as shown in
Figures 1 and 4, and Photo 2. Secure retainer and bracket assembly to the axle housing flange using the Original Equipment
Manufacturer (OEM) bolts and nuts, Figure 1. Apply red Loctite® 271 to the OEM bolt threads and torque to OEM specifications.
Page 4
Assembly Instructions
IMPORTANT:
• To ensure maximum performance from your parking brake system, the cables must be routed as straight as
possible. Bends in the cable can significantly reduce efficiency and thus reduce pull force at the brake. Tight
bends must be avoided with a minimum recommended bend radius of 6" to 8".
• Cables should be properly restrained to prevent "straightening" of bends when tension is applied. Restrain
movement of cable by affixing the cable sheath to body or chassis by fitting cable clamps at various points
over the length of cable or by using original equipment cable attachments points. The clamping method
chosen will require that cable sheath be held tightly without movement, crushing or causing interference to the
internal cable.
• Cables must be initially pre-stretched by multiple applications of the brake handle, then re-adjusted to correct
tension.
General Information (Continued) and Disassembly Instructions
Figure 3. Axle Flange
Maximum Dimension
MAXIMUM
DIA 6.61"
TO FIT
WILWOOD
HAT
2.80”
REGISTER
.050 X 45°
CHAMFER
Figure 4. Retainer / Axle Diagram
BEARING RETAINER
WILWOOD BACKING PLATE
BEARING
AXLE FLANGE
LUG STUDS
WILWOOD BEARING
RETAINER LIP FACES
TOWARDS THE
BEARING
AXLE FLANGE TUBE
Photo 1
Photo 2
Lip
toward
bearing