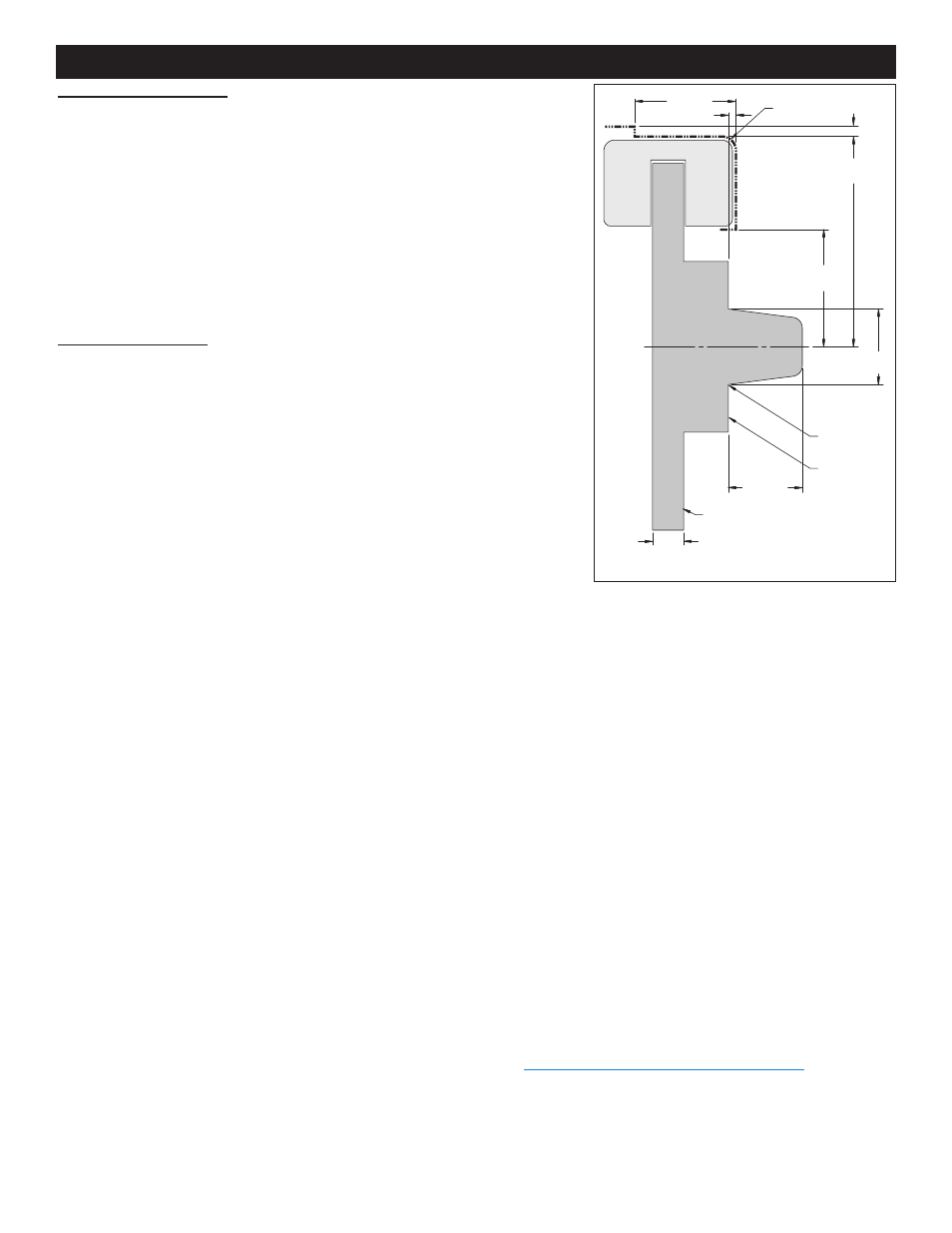
Disassembly and Assembly Instructions
Disassembly Instructions:
•Disassemble the original equipment front brakes: Raise the front wheels off the
ground and support the front suspension according to the vehicle
manufacturer’s instructions.
•Remove the wheel. Remove the bolts from the backside of the spindle that hold the
stock caliper mounting bracket and lift off the bracket and stock caliper as one unit.
If space is a problem, you may have to unbolt the stock caliper from the caliper
bracket before removal.
•Clean and de-grease the spindles. Remove all nicks or burrs on the spindle snout
and threads.
Assembly Instructions (numbers in parenthesis refer to the part list/diagram on the
preceding pages): CAUTION: All mounting bolts must fully engage insert nuts. Be
sure to check that all bolts are either flush or protruding through flanged side of insert
nut after shimming.
•The flat caliper mounting bracket (1) should be installed first with clean, dry threads
on the mounting bolts. Install the bracket by sliding bolt (2) through washer (3)
through the top hole of the mounting bracket (1) and into the upper hole on the
spindle. Slide bolt (4) through the small hole on the spindle from the backside and
through the corresponding hole on the bracket (1). Slip flat washer (5) onto the bolt
and secure with nut (7). Finger tighten only at this time. The bracket must tighten
squarely against the outboard side of the spindle body. Inspect for interference from
casting irregularities, machining ridges, burrs, etc. Later, after the caliper, pad, and
rotor alignment has been checked, and any necessary shims have been put in
place, the threads of the mounting bolts should be coated with red Loctite
®
271 and
bolt (2) torqued to 120 ft-lbs. and bolt (4) torqued to 77 ft-lbs.
•Install wheel studs (8) into the hub (9). Torque to 77 ft-lb. NOTE: There are two five lug patterns in the hub (5 x 4.50 and 5 x 4.75).
Make sure of the correct hole pattern for the correct wheel application before installing studs into hub.
•Pack the large inner bearing cone (10) with high temperature disc brake bearing grease (available from your local auto parts store) and
install into the backside of the hub (9).
•Install the grease seal (11) by pressing into the backside of the hub (9).
•Pack the small outer bearing cone (17) with high temperature disc brake bearing grease and install into front of hub (9). Slide the hub
assembly (8, 9 ,10, 11 and 17) onto the spindle. Secure using spindle washer (18), stock adjusting nut and nut locking device. Adjust
bearing using a 12” wrench to tighten the adjusting nut while turning the rotor. When the rotor binds slightly, all the bearing parts are
seated properly. Back of the nut 1/6” to 1/4” of a turn or enough to allow 0.001” to 0.007” end play. Lock the nut with a new cotter pin.
WARNING: Failure to back off the adjusting nut may cause the bearing to run hot and be damaged, which could cause the wheel to
lock or come off during operation, creating a risk of serious bodily harm.
•Install the o-ring (19) on the dust cap (20), and screw dust cap assembly onto the hub (9). Friction created by the o-ring (19) on the
dust cap (20) keeps it from unscrewing.
•With the larger I.D. side of the rotor (12) facing away from the hat (13), bolt rotor (12) to hat (13) through the backside of the rotor using
washers (14) and bolts (15). Using an alternating sequence, apply red Loctite® 271 to the threads and torque bolts to 155 in-lb. For
an added measure of security, the bolts may be safety wired using standard 0.032 inch diameter stainless steel safety wire as shown
in Figure 3. Please refer to Wilwood’s data sheet DS-386 (available at
www.wilwood.com/Pdf/DataSheets/ds386.pdf
) for complete
safety wire installation instructions.
•Slide the rotor/hat assembly over the studs (8) in the hub (9) taking care to align the small countersunk holes in the hat (13) with the
small threaded holes in the hub (9). Install three flat head socket head screws (16) through the small holes in the hat (13) and torque
to 85 in-lb.
CENTER
LINE OF
WHEEL
.50 (12,7)
RADIUS
.48 (12,2)
3.60 (91,4)
4.69
(119,1)
2.50
(63,5)
7.92
(201,2)
.29 (7,4)
CALIPER
WILWOOD ROTOR
WHEEL MOUNT
SURFACE
.28 (7,1) RADIUS
NOTE: A MINIMUM OF .080” CLEARANCE MUST BE MAINTAINED
BETWEEN THE WHEEL AND CALIPER IN ALL AREAS
1.10 (27,9) ROTOR THICKNESS
2.32 (58,9)
Figure 2. Wheel Clearance Diagram
Page 4