Application note - 95043, Mounting instructions for add-a-pak generation vii, Modules – C&H Technology VSKDS408-060 User Manual
Page 8: Applic ation n o te
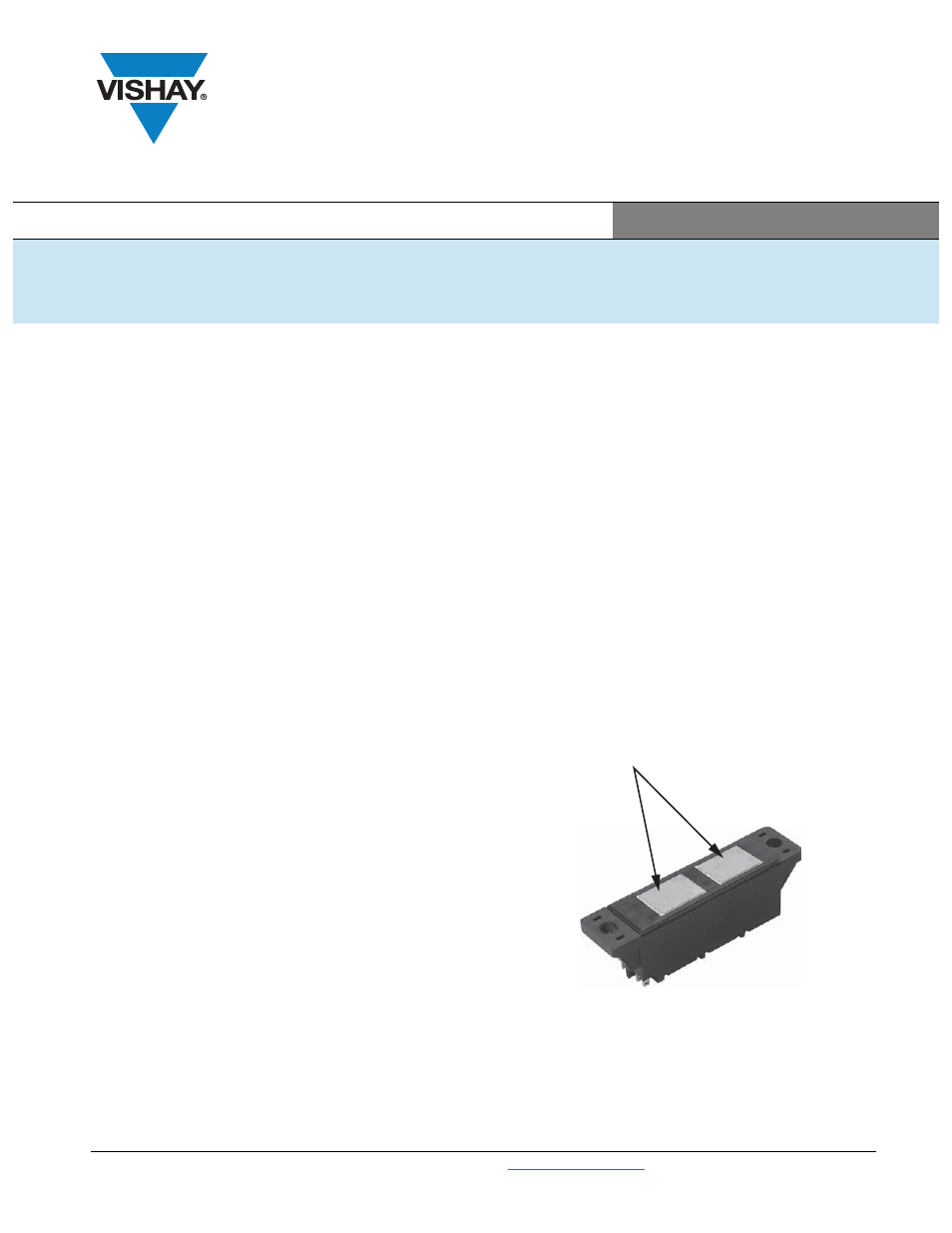
Document Number: 95043
For technical questions, contact:
www.vishay.com
Revision: 17-Dec-08
1
V I S H A Y S E M I C O N D U C T O R S
Modules
Application Note
Mounting Instructions for
ADD-A-PAK Generation VII
APPLIC
ATION N
O
TE
Generation VII ADD-A-PAK (AAP) power modules combine
the excellent thermal performance enabled by a direct
bonded copper (Al
2
O
3
) substrate, superior mechanical
ruggedness, and an environmentally friendly manufacturing
process that eliminates the use of hard molds, thus reducing
direct stresses on the leads. To prevent axial pull-out, the
electrical terminals are co-molded to the module housing.
The VSK series of AAP modules uses glass passivated and
Schottky power diodes and thyristors in circuit
configurations including common anode, common cathode,
half-bridge, and single switch. The semiconductors are
internally connected through wire-bonding and electrically
isolated from the bottom baseplate, allowing the use of a
common heatsink and enabling a more compact overall
assembly.
INTRODUCTION
Major AAP Generation VII module features
• High blocking voltage up to 1600 V
• Industrial standard package style, fully compatible with
TO-240AA
• High isolation capability up to V
RMS
= 3500 V
• High surge capability with I
FSM
up to 3000 A
• No toxic material: Completely lead (Pb)-free, RoHS and
UL compliant
• Elimination of copper base plate reduces weight to 75 g
• Elimination of process steps requiring usage of chemicals
and related waste treatment promotes a cleaner and more
environmentally friendly manufacturing process
These features allow AAP Generation VII modules to fit into
existing standardized assembly processes. Important
factors in the assembly process include
• Heatsink design
• PCB, busbar, and cable design
• Power leads size/area
• Distance from adjacent heat-generating parts
The implications of these items and the requirements for
assembly of AAP Generation VII modules are discussed
over the following pages.
SPECIFYING THE HEATSINK
The heat generated by the module has to be dissipated with
a heatsink. Typically natural or forced air cooling is used.
To optimize the device performance, the contact surface of
the heatsink must be flat, with a recommended flatness of
0.03 mm ( 1.18 mils) and a levelling depth of less than
0.02 mm (
0.79 mils), according to DIN/ISO 1302. A milled
or machined surface is generally satisfactory if prepared
with tools in good working condition. The heatsink mounting
surface must be clean, with no dirt, corrosion, or surface
oxide. It is very important to keep the mounting surface free
from particles exceeding 0.05 mm (2 mils) in thickness,
provided a thermal compound is used.
MOUNTING OPERATIONS
The AAP Generation VII modules are designed with an
exposed DBC Al
2
O
3
substrate.
This is used to optimize the thermal behavior of the module.
To reduce the risk of damage during mounting, the ceramic
has been given additional mechanical ruggedness in the
form of two separate 15.8 mm by 21.1 mm (0.62" by 0.83")
pieces of DBC substrate, which can be seen in the photo
below.
Before mounting, inspect the module to insure that the
contact surface of the bottom substrate is clean and free of
any lumps or bulges that could damage the device or
impede heat transfer across its surface.