Locke TR-30 User Manual
Page 32
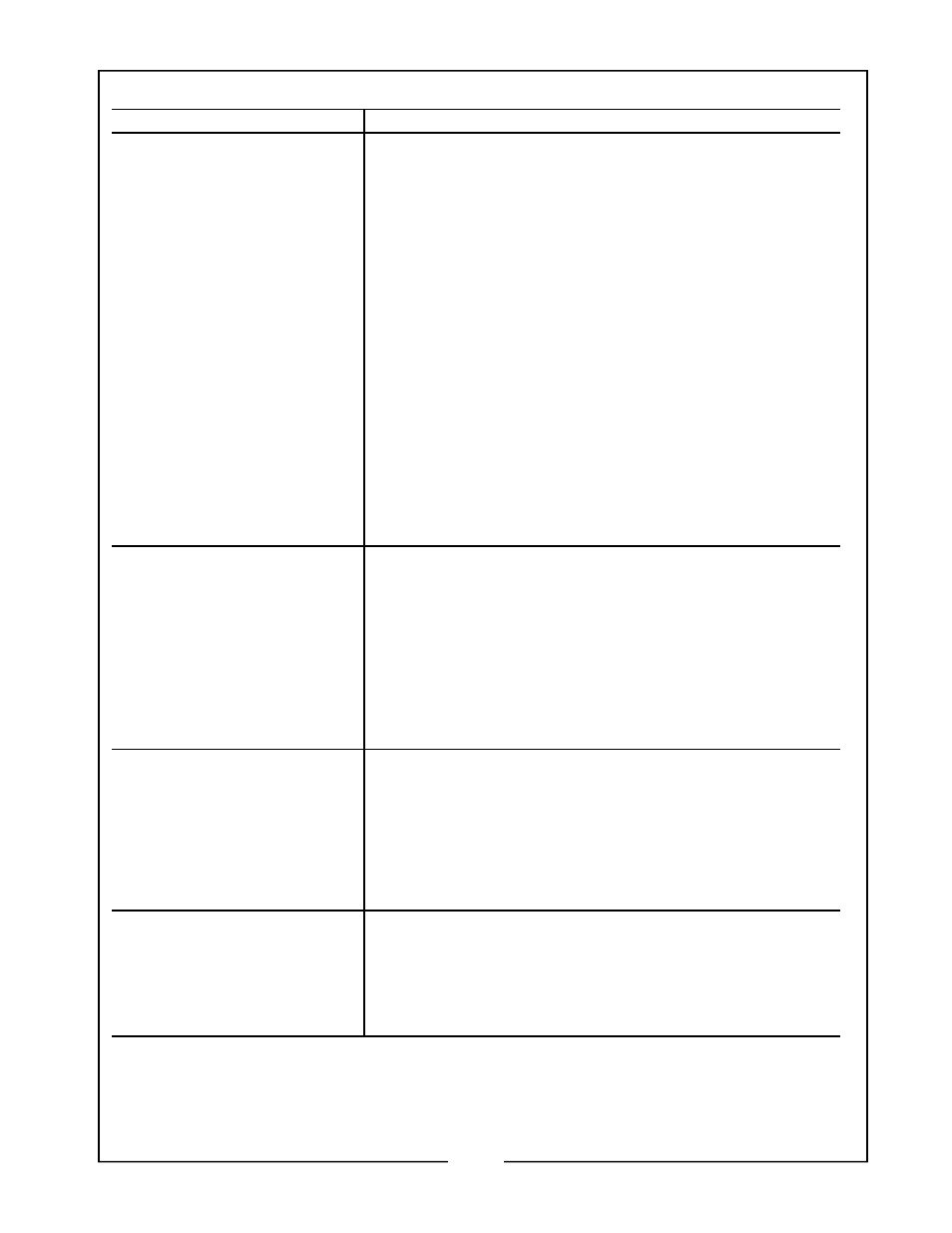
Solution
a. Recheck calibration.
b. Ground speed is faster than calibrated speed. Recheck speed
using method in application guide.
c. Nozzle size smaller than size used for calibration.
d. If the pressure at the manifolds and nozzles is less than pres-
sure at the control box gauge (#3), feed lines to booms may
need to be cleaned.
e. Check for worn nozzles. Nozzles should be within 10% of
specs. Replace if necessary.
f. Check the travel pattern. Not enough overlap during spraying
may result in under-application by leaving areas unsprayed.
g. Check control box gauge. IF actual rate is less than gauge indi-
cates, suspect a faulty gauge.
h. Check levels in tank. IF tank level was more than amount cal-
culated, a false underapplication condition occurs.
I. Check for filter screen blockage.
j. Check for loose pump impeller bolt.
k. Check for clogged impeller channels. (Requires pump diassem-
bly; try all other options first.)
a. Check nozzles for obstructions in feed holes. Clean nozzles
with toothbrush or suitable brush. Steel picks, nails, etc. will
damage the nozzle.
b. Inspect the check valve in front of each nozzle. Clean and in-
spect rubber diaphragms. The correct rubber viton diaphragm is
marked with a “v”. EPDM rubber diaphragms will become swol-
len and will not work.
c. Check hose barbs screwed into the metered manifolds. If hose
barbs are screwed too far into the manifold, flow can be re-
stricted.
a. Disassemble diaphragm cap from body and check that the cap
spring moves freely.
b. Inspect the diaphragm. Clean or replace if necessary.
c. Increase spraying pressure. About 15 psi is required at the
check valve to hold it open.
d. Check the control box gauge for faulty reading.
a. Clean diaphragm in check valve at nozzle. Look for debris or
nicks which would allow leakage.
b. If problem still appears, check solenoid valve for that section for
proper adjustment of foreign matter on the seat washers in the
valve. Replace washers and seals with valve repair kit if neces-
sary.
Problem
13. Not enougn material is be-
ing applied; rate is not as
calibrated.
14. Nozzle flows across boom
are inconsistent and vary
several ounces high or low.
15. Diaphragm check valves at
nozzles will not stay open
while spraying.
16. Nozzles continue to spray or
dribble after boom is turned
off.
31