Locke TR-30 User Manual
Page 31
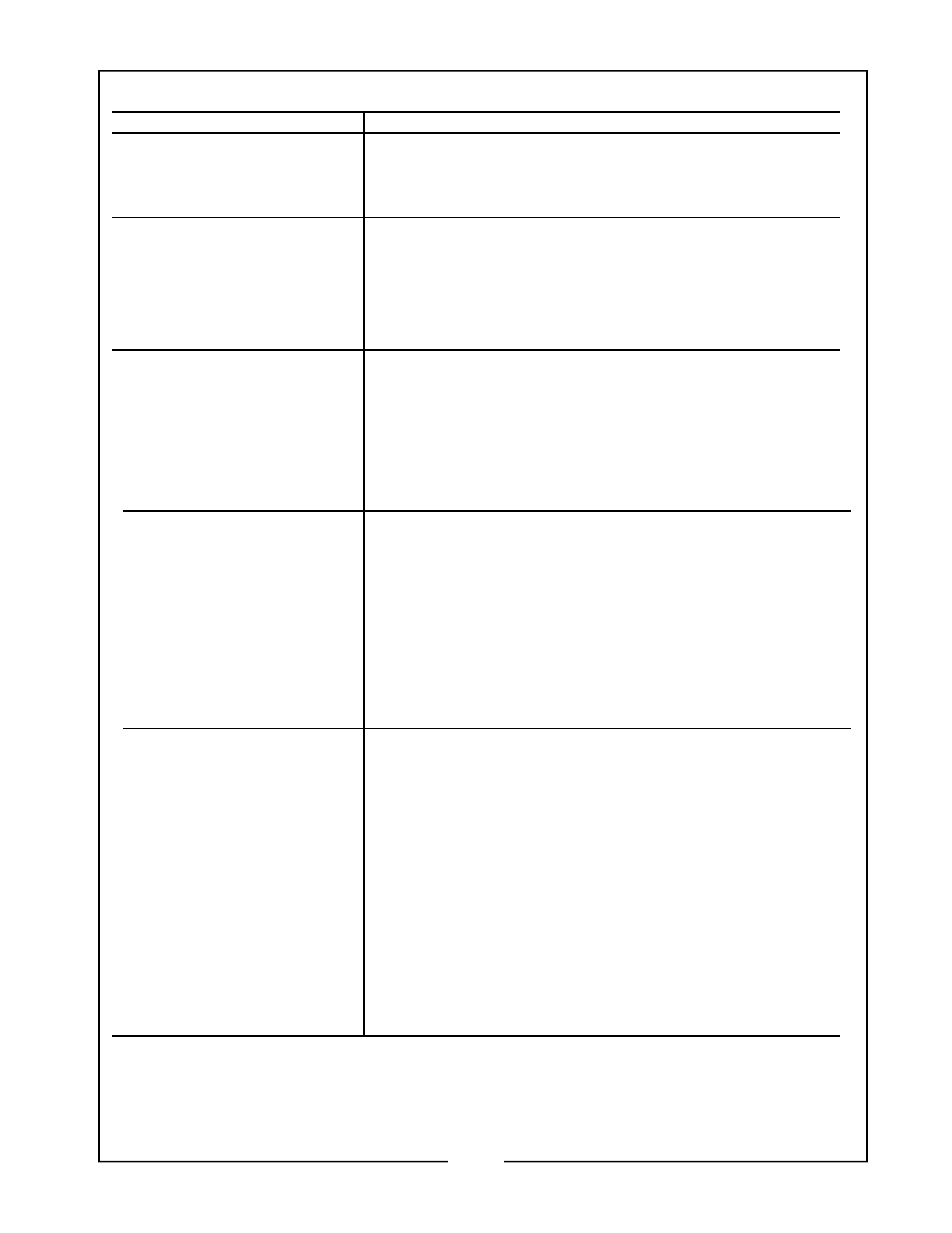
Solution
a. Throttling valves are becoming plugged. Open gray throttling
valve with nozzles turned off and allow flow to flush out valves
for about 15 seconds per valve. Reset throttling valves.
a. Throttling valves are becoming plugged. Unscrew gray knob on
throttling valve with boom sections turned off and allow to flow to
flush out valves for at least 15 seconds per valve. Reset the
throttling valves when finished.
b. Look for a restriction in the bypass line between the throttling
valves and the tank. If nozzle pressure returns to normal when
one or more boom sections are turned on, spraying accuracy is
unaffected.
a. Check GPM flow to be sure that pump has the capacity to spray
the desired volume.
b. Change to smaller size nozzles.
c. Reduce flow to agitation by partially closing agitation valve Make
sure that there is still adequate agitation after adjusting.
d. Check to be sure that manual pressure control vavle is open.
e. Increase engine RPM to increase pump output.
a. Low Flow: Check the boom feed line for that boom section for
blockage or kinks. Inspect check valves, nozzles, metered
manifold and electric solenoid valves for obstructions and chemi-
cal buildup. Remember, low voltage or a weak battery will result
in valves not opening completely. Check hose length leading to
manifold. If hose length is considerably longer than other sec-
tions, cut hose length to match length of other boom sections.
b. High flow: Check the boom feed line for that boom section for
length. If feed line is much shorter than other boom sections,
replace with longer line. Check to see that all nozzles are the
same size.
a. Recheck calibration.
b. Ground speed is slower than calibrated speed. Recheck speed
using method in application guide.
c. Check to make sure all nozzles are correct and the same size.
One oversized nozzle will result in over-application.
d. Check nozzle spacing.
e. Check control box gauge.
f. Overlap of rows may be too great causing double application in
some area.
g. Check levels in tank. Less than calculated amount would falsely
indicate over application.
h. Check for worn nozzles. Nozzles should be within 10% of
specs. Replace if necessary.
i. Check for possible wheel slippage.
Problem
8. Suspect faulty control box
gauge because pressure
changes when turning off
boom sections.
9. After correctly setting the
throttling valves, boom pres-
sure will not stay constant
when a section of the boom is
turned off.
10. Cannot increase boom pres-
sure to desired setting al-
though pump and plumbing
systems are set and operat-
ing correctly
Plumbing Problems
11. Flow to one boom section is
different than flow to other
boom sections (as con-
firmed by catching flows of
each nozzle).
12. Too much material is being
applied; rate is not as cali-
brated.
30