Periodic inspection – Siemens JFR Distribution Step Voltage Regulator 21-115532-001 User Manual
Page 16
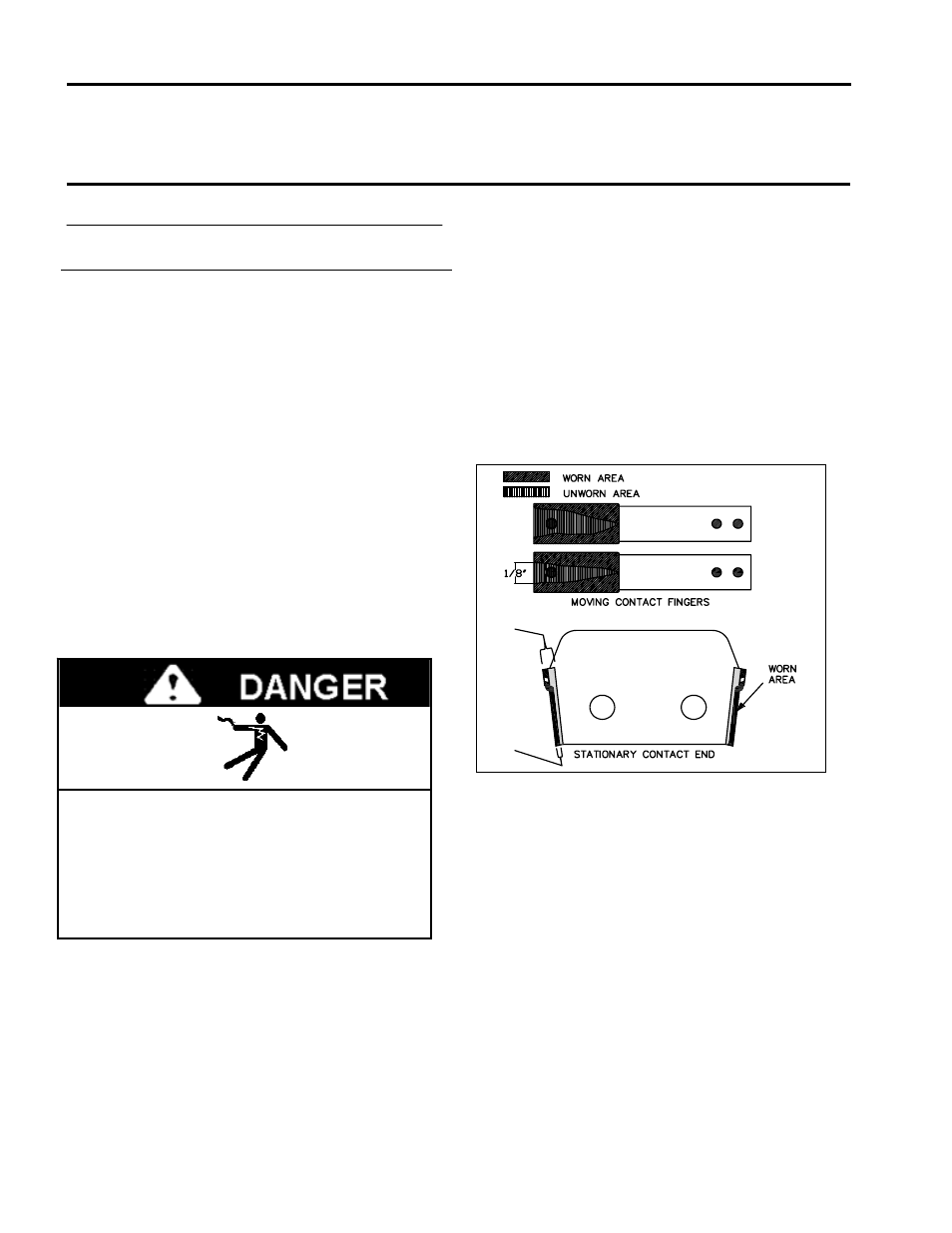
M A I N T E N A N C E
Page 12
PERIODIC INSPECTION
A sample of oil from the regulator should be subjected to
dielectric breakdown test, per ASTM D-877. If found below
25kV, the oil should be changed or reconditioned. Refer to
ANSI C57.106-2002. Other tests, especially Neutralization
Number, Interfacial Tension and Power Factor are also useful
and may be preferred by particular users.
The oxidation inhibitor in the oil will be depleted over a period
of a few years and should be replaced. The inhibitor is 2, 6-
ditertiary-butyl-para-cresol (DBPC) at a concentration level of
0.2 to 0.3%.
The time interval between internal inspections will depend
upon frequency of tapchanger operation and the load on the
regulator. Regulators subjected to numerous overloads and a
high load factor may require more frequent inspections than
those carrying normal loads. While internal inspection is not a
necessity, preventive maintenance inspections will help assure
the continuity of service.
To untank a JFR regulator, proceed as folllows:
1. Remove the regulator from service as described on
Page10.
2. Place the regulator in a position where energized
overhead lines will not interfere.
3. Operate pressure relief valve to vent regulator before un-
tanking
4. Remove the mounting bolts holding the control box onto
the main tank.
5. Remove all cover bolts.
6. The regulator can now be pulled from the main tank by the
cover lifting eyes.
When inspecting, check to be certain all hardware and con-
nections are tight. The principal point of the internal inspection will
be the condition of the arcing contacts on the tapchanger. Since
numerous factors influence the rate of contact tip wear, no one
criteria can be stated to recommend when a contact should be
changed.
The following figure shows the possible condition of contact wear
after a period of operation. If the contact surface is less than 1/8
inch wide, the contact should be replaced. (See the Figure below)
Contacts, both movable and stationary, show normal burning and wear
once placed in service. If for any reason A1 dimensions exceed 4/5 of
A, the stationary contact should be replaced. (See the Figure below)
•
UPPER FILTER PRESS SEALING
If cover top cap is removed, make certain the cap is properly
sealed when replaced on cover. Siemens recommends applying
pipe sealant (Loctite PST or equivalent) around the threads of the
adapter. Furthermore, it is recommended that the seal be tested by
applying 5 psig pressure through the pressure relief valve fitting for
5 minutes, with no loss in pressure. Failure to assure seal may
allow moisture to be pulled into the unit during a cool-down cycle.
•
FAN MAINTENANCE
Cooling fans (if equipped), require minimum attention. Fans with
plain sleeve bearings or
Oil-Lite
sleeve bearings should be oiled at
least once a year with SAE 10-W engine oil which does not thicken
in cold weather. Oil must be added to sleeve bearings before
starting motor for the first time after installation.
Fans equipped with ball bearing motors are packed with grease
before shipment and should be greased at least once a year with a
soda-soap, ball-bearing grease of medium consistency furnished
by a reliable supplier.
A
A1
Hazardous voltages. Will cause serious injury, death, or
equipment damage.
To prevent:
Always de-energize and ground the equipment before
maintenance requiring access to high voltage parts.