Technical reprint tr-002 – Sierra Monitor Corporation TR-002 User Manual
Page 4
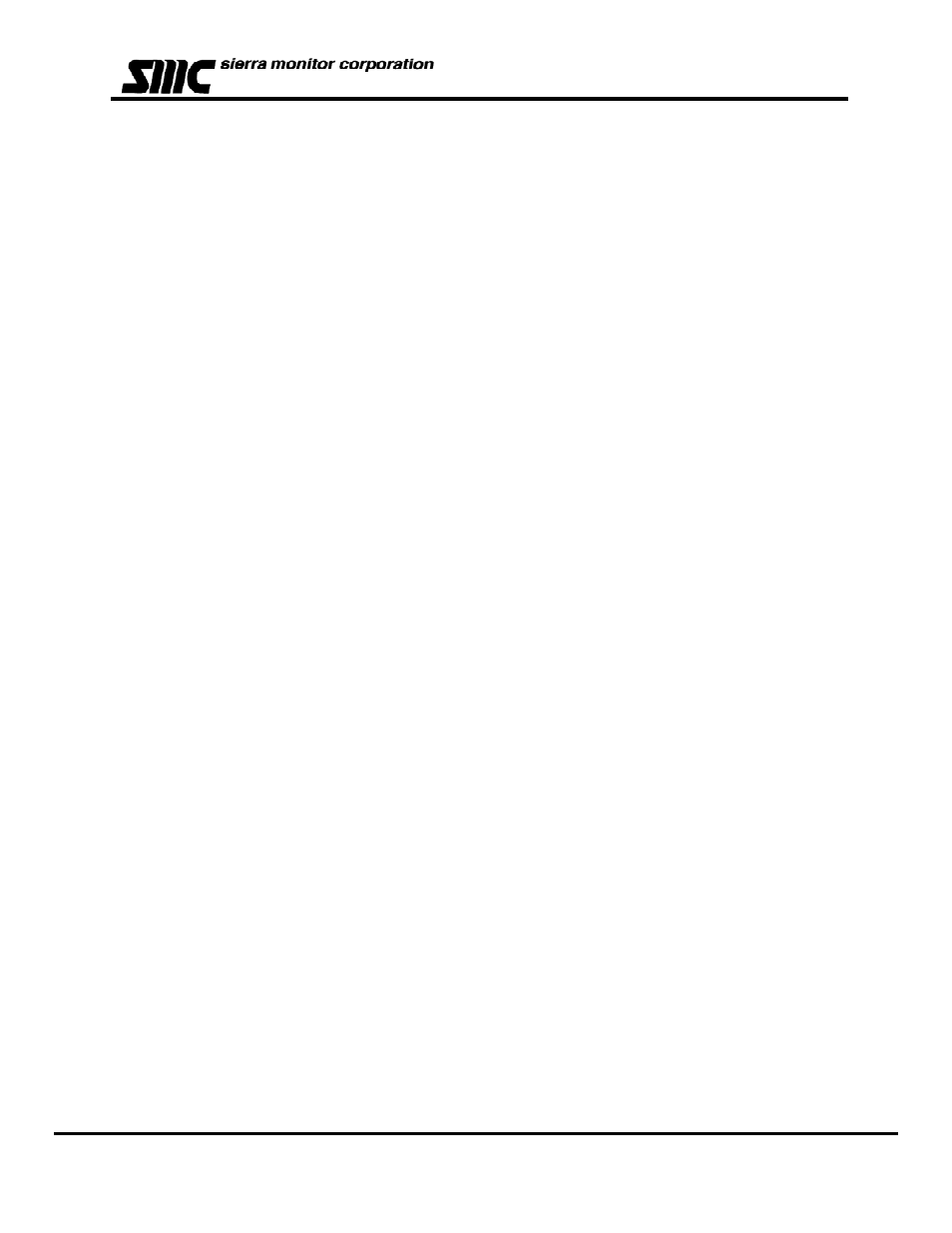
Technical Reprint TR-002
Sierra Monitor Corp. 1991 Tarob Ct., Milpitas, California 95035 USA 408-262-6611, 800-727-4377 FAX: 408-262-9042
Visit our Web Site at: http://www.sierramonitor.com E-Mail:
Rev. A1
Typical Hydrogen gas sensor locations in a semiconductor manufacturing facility include:
•
Hydrogen storage areas
• Valves
in
Hydrogen
pipelines
•
Furnace area – inlet, outlet, internal tubing
•
Off gas ducts
•
Return room air ducts
•
Cavity between dropped ceiling and the roof (or floor above)
In this plant there are sixteen sensors located within four rooms. Sensors are a catalytic bead type. There are two
beads in each sensor element, one of which is activated by a catalyst in the presence of a combustible gas and the
other is not. These beads are inserted in a wheatstone bridge circuit and the relative resistance of the beads affects the
bridge output in the presence of gas. Changes in temperature and relative humidity have no effect on the output of the
circuit since the catalyzed bead and the reference bead are similarly affected and the relative difference in output does
not change.
Sensor output is digitalized at the sensor module and transmitted to the controller. Transmitting a digital signal give
great tolerance to RFI and EMI effects. In addition it enables diagnostics to be performed at the sensor and be
transmitted to the controller along with the concentration measurements. Also, sensor modules are given an address
which permits multiplexing multiple sensors on a single wire.
Benefits of Controller Capability. The controller is designed to provide high reliability, ease of operation and data
management capability. It is the data management capability that separates the SENTRY controller from other gas
monitoring systems. Conventional controllers simply react to events (as a thermostat reacts to temperature reaching a
setpoint). To manage a risk it is necessary to use information to formulate a response to leak rather than reacting to an
event after an alarm has occurred.
It has already been mentioned that the system configuration is user programmable. This includes alarm levels,
calibration procedures, report scheduling and display mode. The low alarm level is set at 10 percent of the LEL and the
high alarm level is set at 60 percent of the LEL. A single controller can handle up to eight sensors and four controllers
can be mounted in a standard 19 inch instrumentation rack. The controller displays the sensor concentration, the gas
type, concentration units, and alphanumeric messages.
Reports to Help Decision-Making and Document Due Diligence. The Sentry can provide data to a distributed
control system (DCS) via MODBUS or provide reports via a printer. The reports are also available at the display and
include status reports, history reports, calibration reports and system configuration reports. This particular customer
only needed the printer reports. When the concentration exceeds a user definable limit. The controller prints each key
event when it occurs.
This history reports are also very useful in determining if there is any regularity to gas leaks. For example, history
reports show the date and time the highest concentration occurred in the period. The frequency for the period can be
programmed on an hourly, shift, or daily basis. As one semiconductor facility one sensor recorded its highest
concentration at the time every day. After investigation it was found that a purging of a Hydrogen furnace was releasing
Hydrogen into the room. The purging procedure was changed and release of Hydrogen into the room stopped. Daily
history reports also provide good documentation to confirm the facility’s safe operating procedure if legal action was
brought against the company. In today’s legal environment, such documentation is essential to minimize liability. In
addition to the alarm indication at the controller, the facility has an annunciator panel located near a security area. The
panel displays each combustible and toxic gas sensor in alarm.
Summary
Gas risk management requires a comprehensive look at the hazards of gas leaks. Properly designed gas monitoring
systems provide suitable hardware in combination with data management and diagnostics capability to custom-fit a
solution for managing, rather than reacting to, gas leaks.