New wafer processing laboratory – Sierra Monitor Corporation TR-002 User Manual
Page 3
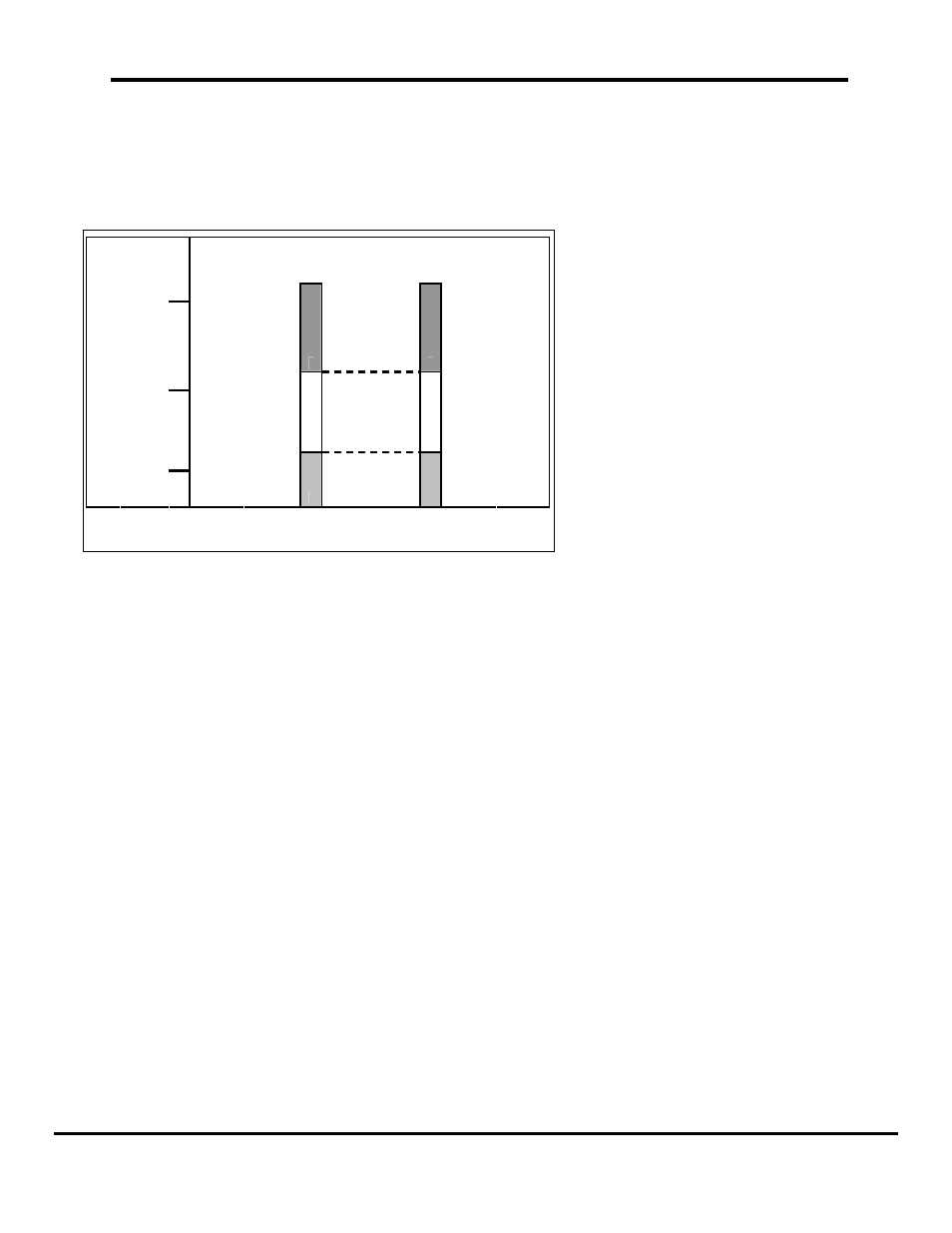
Gas Risk Management – A Safer Approach to Monitoring for Hazardous Gases
Sierra Monitor Corp. 1991 Tarob Ct., Milpitas, California 95035 USA 408-262-6611, 800-727-4377 FAX: 408-262-9042
Visit our Web Site at: http://www.sierramonitor.com E-Mail:
Rev. A1
METHANE
HYDROGEN
PPM in
air
% Gas
in air
PPM in
air
% Gas
in air
100%
50,000 5.0
Typical HIGH
Alarm Setpoint
40,000 4.0
EMERGENCY
60%
30,000 3.0
Typical LOW
Alarm Setpoint
24,000 2.4
Lower
Exp
losi
v
e
Li
mi
t (%LEL)
20%
10,000 1.0
WARNING
8,000 0.8
Fig. 3 Alarm Setpoints for Methane and Hydrogen
numbers of sensors, it may be economical to apply the calibration gas automatically. A method to check sensor span
voltage versus acceptable tolerance should be available either through calculation or as a system report. Advanced
systems can prompt “calibration due” according to a user configured calibration frequency.
Response To Alarms. Response to alarms begins with preplanning – in plant and outside the plant perimeter. Next,
training is essential to insure all plant
personnel understand their function and
have internalized their responsibilities. Part
of this training includes identifying false
alarms.
Relay action usually involves a low alarm
(warning light and siren and ventilation to
reduce the gas concentration) and high alarm
(emergency light and siren and a process
action). Process action involves turning off,
or isolation of, the source of the gas and
shutdown of process equipment. A high-high
alarm can be used as an indication that the
concentration is very dangerous. “Zone
voting,” where two or more sensors must be
in alarm before activating a zone relay, can
be used as a way to neutralize a faulty
sensor and to take action specific to the area
that the gas hazard exists.
The final element of responding to alarms concerns evacuation procedures, both in plan in the local vicinity, and
requesting outside assistance such as the fire department. Events that trigger these actions are based on the hazard
assessment. Recent catastrophes and near catastrophes more than demonstrate the need for this requirement.
Record-Keeping. Record-keeping becomes an important element of response to alarms. Sensor status reports
provide a valuable reference to assess the severity and breadth of the gas hazard. Real-time and post-event analysis
can be generated. Calibration reports give data for monitoring sensor performance over time. Sensor history reports
are useful for satisfying regulatory requirements and providing data on gas exposure. It is the transfer of information
provided from the system to plant personnel that enables gas risk management to be effective.
New Wafer Processing Laboratory
A new wafer processing laboratory located in California had extensive Hydrogen and toxic gas piping and equipment
utilizing those gases. The facility was designed to minimize the possibility of a gas leak and further measures were
taken to contain rather than expel any gas that might accidentally leak. For example, all gas piping was run through a
NEMA duct to prevent gas from being uncontrollably dispersed into the room.
The facility installed both a Hydrogen and toxic gas monitoring system. It was necessary for the Hydrogen and toxic
gas monitoring system to be independent due to the capabilities of the sensors. The remainder of this discussion will
focus on the Hydrogen monitoring system; however, much of the discussion also applies to the toxic gas monitoring
system.
The hazardous gas monitoring system used was the Sierra Monitor SENTRY Gas Monitoring System. The system
uses a sophisticated microprocessor-based controller. System configuration is user programmable to allow the system
to be customized to the specific application requirements. SENTRY has extensive data management and internal
diagnostics that provide information required to help manage gas leak problems.
Sensor Locations. One of the first questions to be addressed as part of the system specification is how many sensors
are required and where should they be located? There are no rules or formulas to answer these questions. In general,
it is important to locate sensors close to the likely sources of leaks and in areas where a leaked gas might lighter than
air, thus dictating whether sensors be located below or above the leak. With Hydrogen being lighter than air, sensors
are always located in the ceiling as a backup to sensors located near the source of the leak.