Kiflyc\j_ffk`e, J Page 37
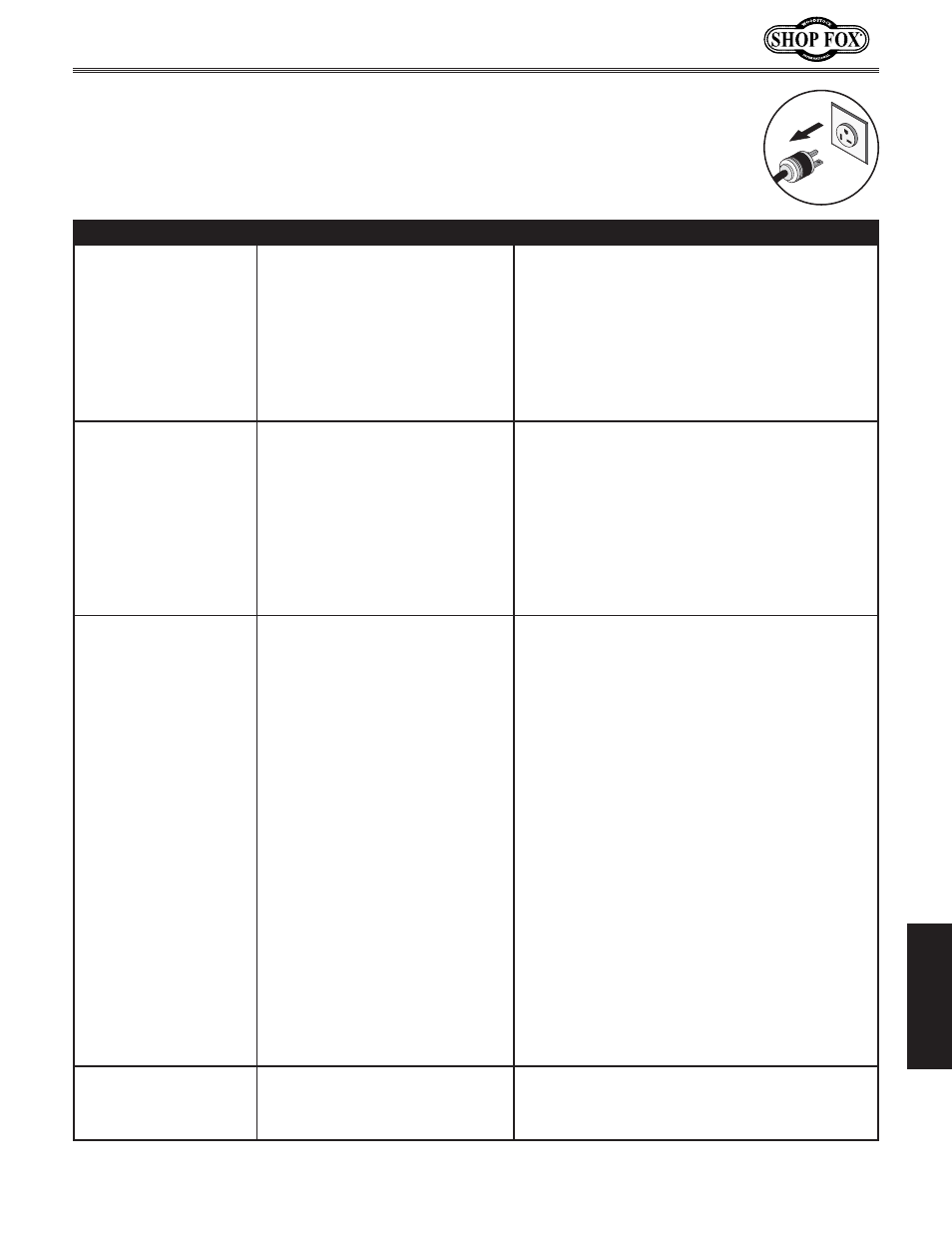
-35-
Df[\cN(-/.=fiDXZ_`e\jD]^%J`eZ\0&((
J
M
@:<
KiflYc\j_ffk`e^
This section covers the most common problems and corrections with this type of
machine.
N8IE@E>;FEFKdXb\XepX[aljkd\ekjlek`cgfn\i`j[`jZfee\Zk\[Xe[
dfm`e^gXikj_Xm\Zfd\kfXZfdgc\k\jkfg
GIF9C
GFJJ@9C<:8LJ<
:FII<:K@M<8:K@FE
Machine does not start or
a breaker trips.
1. Switch disabling key removed.
2. Power supply switched OFF or is at
fault.
3. Wall fuse/circuit breaker is blown/
tripped.
4. Wiring is open/has high resistance.
5. Motor ON button or ON/OFF switch
is at fault.
6. Motor is at fault.
1. Install switch disabling key.
2. Ensure power supply is switched on; ensure power
supply has the correct voltage.
3. Ensure circuit size is suitable for this
machine; replace weak breaker.
4. Check for broken wires or disconnected/corroded
connections, and repair/replace as necessary.
5. Replace faulty ON button or ON/OFF switch.
6. Test/repair/replace.
Machine has vibration or
noisy operation.
1. Motor, motor mount, or other
mounting component is loose or
broken.
2. Motor fan is rubbing on fan cover.
3. Impeller is loose or damaged and
unbalanced.
4. Motor bearings are at fault.
1. Retighten. Use thread locking fluid if necessary.
Replace stripped fasteners or damaged components
if necessary.
2. Replace dented fan cover; replace loose/damaged
fan.
3. Disconnect dust collector from power, and inspect
the impeller for dents, bends, loose fins. Replace
the motor and impeller as a set if the motor shaft
and the impeller hub are damaged.
4. Test by rotating shaft; rotational grinding/loose
shaft requires bearing replacement.
Dust collector does not
adequately collect dust or
chips; poor performance.
1. Dust collection bags are full.
2. Filter is dirty.
3. Restriction in duct line.
4. Dust collector is too far away, or
there are too many sharp bends in
the ducting.
5. Lumber is wet and dust not
flowing through ducting smoothly.
6. Leaks in ducting or too many open
ports.
7. Not enough open branch lines,
causing a velocity drop in the main
line.
8. Ducting or machine dust ports are
incorrectly sized.
9. The machine dust collection
design is inadequate.
10. The dust collector is too small
for the dust collection system, or
ducting layout design inadequate.
1. Empty collection bags.
2. Clean filter.
3. Remove restriction in the duct line. A plumbing
snake may be necessary.
4. Relocate the dust collector closer to the point of
suction, and rework ducting without sharp bends.
Refer to System Design, beginning on Page 22.
5. Process lumber with less than 20% moisture
content.
6. Rework the ducting to eliminate all leaks. Close
dust ports for lines not being used.
7. Open 1 or 2 more blast gates to different branch
lines to allow the velocity in the main line to
increase.
8. Re-install correctly sized ducts and fittings. Refer
to System Design beginning on Page 22 for more
solutions.
9. Use a dust collection nozzle on a stand.
10. Install a larger dust collector to power your dust
collection system.
Sawdust being blown into
the air from the dust
collector.
1. Duct clamps or dust collection
bags are not properly clamped and
secured.
2. Bag clamps are loose or damaged.
1. Re-secure ducts and dust collection bag, making
sure duct and bag clamps are tight and completely
over the ducts and bags.
2. Retighten bag clamps.