MITSUBISHI ELECTRIC T-60 User Manual
Page 88
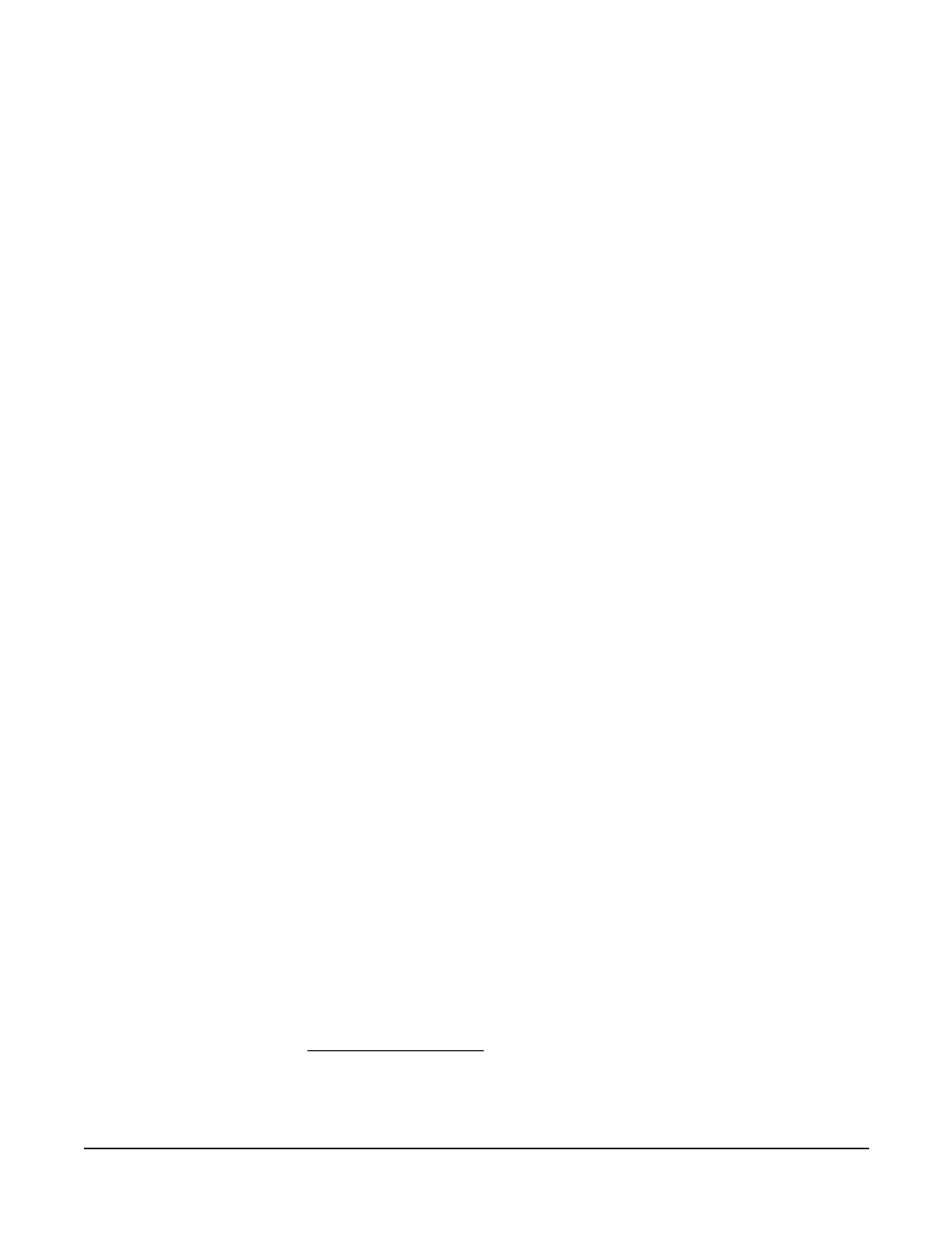
Follow the setup guidelines for the 1747-KE module exactly. If possible, use
your Allen-Bradley programming software to communicate to the SLC-500
once you perform all of the setup operations. In general you can use the
default settings as long as you change the DF1 Port Setup Parameters, select
the correct node address, and select FULL DUPLEX operation. If you want
to check all of the parameters using a terminal connected to the setup port,
use the following parameters:
DF1 Port Setup Parameters:
19.2K baud (this is not critical, the -SL5 option will auto-baud and find
yourbaud rate)
8 data bits
No parity
1 stop bit.
DH-485 Port Setup Parameters:
Node Address - 2 Set the PLC to node address 1 (this is performed
with the Allen-Bradley setup software for the PLC). The -SL5
interface will reside at node address 0.
Max Node Address - 31
Message Time-out - 1000ms
Pass Through - Enabled
Baud Rate - 19200
DF1 Protocol Menu:
Full Duplex
DF1 Protocol Full Duplex Setup Menu:
Duplicate Packet Detection - Disabled
Checksum - BCC
Constant Carrier Detect - Disabled
Modem Init String - (blank)
Embedded Response Detect - Embedded Response
ACK Time-out - 1.0 Seconds
ENQuriy Retries - 2
NAK Received Retries - 2
Be sure to return the 1747-KE module to the Run mode (jumper settings),
and jumper the 1747-KE for RS-232. Connect the DF1 port to COM1 on the
T-60 Series product, and you should be able to communicate. Try sending a
CALL PLCINIT(1,1) to see if you get a Ready response. If you do, start
programming! If not, try checking that you are using COM1 on the T-60
Series product. Make sure you are plugged into the DF1 port, not the
configuration port on the 1747-KE. Make sure you are no longer in setup
mode for the 1747-KE, and that the jumpers are set to RS-232.
Command Variations:
The CALL PLCREAD and CALL PLCWRITE commands for the SLC-500 are
significantly different from the other PLC’s described here. The following
descriptions apply to the -SL5 Option only:
T-60 Operator's Manual
80