Kfz series, General pump – General Pump KFZ Owner Manual User Manual
Page 12
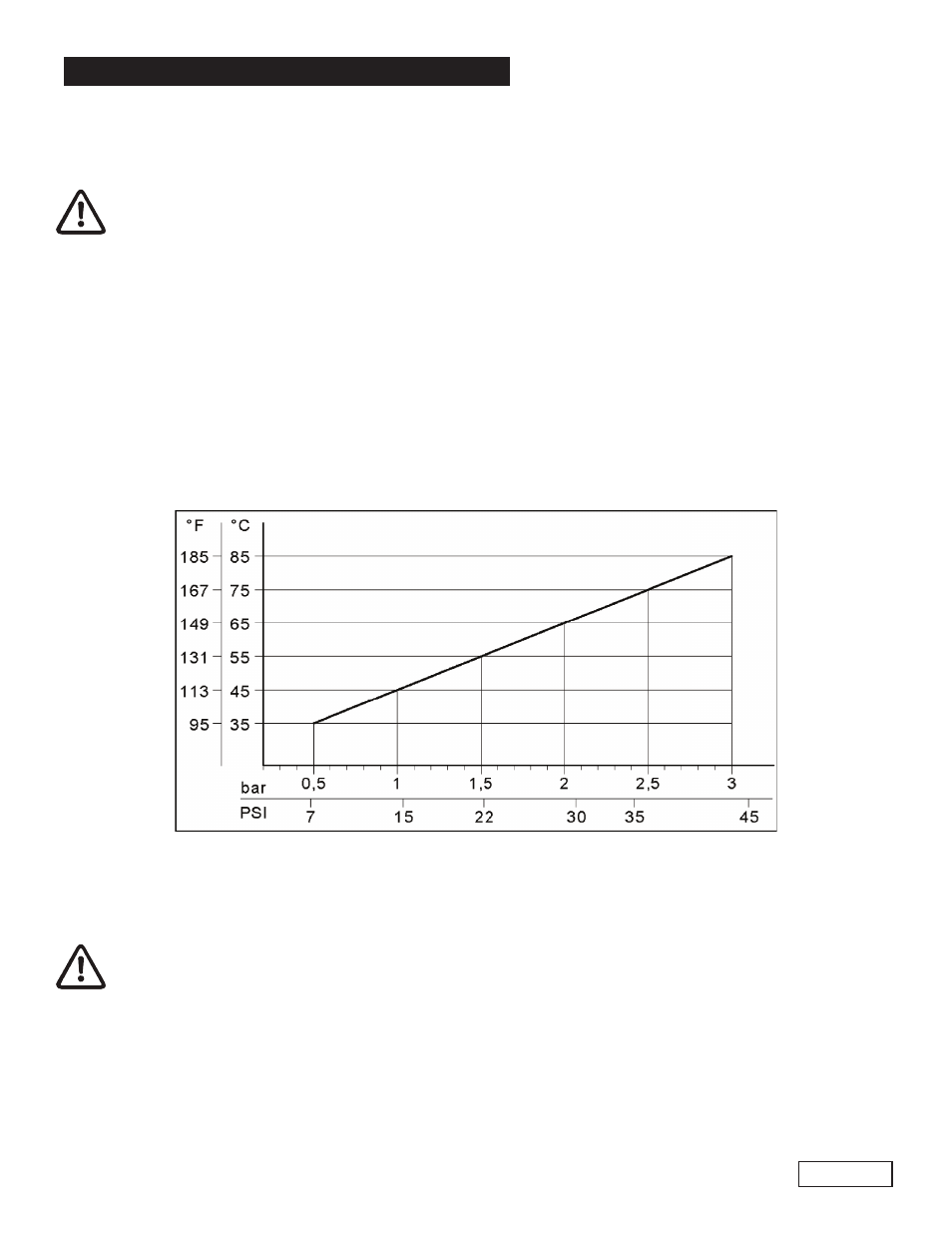
GENERAL PUMP
A member of the Interpump Group
KFZ SERIES
Page 12
2. Rotate the mechanical part by 180o, and reposition the rear crankcase cover so that the oil dipstick is facing
upwards; reposition the lifting bracket and the related closing caps in the upper part of the crankcase; finally,
correctly reposition the identification plate in its appropriate seat on the crankcase.
Be sure that the lower draining holes on the crankcase near the plungers are open, and not closed by
the plastic caps as required for the previous version.
3. Join the hydraulic part with the mechanical part as indicated in Chapter 2, paragraph 2.2.5 of the
repair manual.
9.4 Hydraulic Connections
In order to isolate the system from the vibrations produced by the pump, we advise to build the first section of the duct near
the pump (both for intake and delivery) with flexible hose. The consistency of the intake section must allow to avoid
deformation caused by the depressurization produced by the pump.
9.5 Pump Feeding
To obtain the best volumetric efficiency, a minimum positive head of 0.20 meters is required. In case of fluid
temperatures ranging from 95
0
F (35
0
C) up to 185
0
F (85
0
C) the correct inlet pressures are specified in the graph of
fig. 6.
9.6 Suction Line
For the pump’s correct operation, the suction line must have the following characteristics:
1. Minimum internal diameter as indicated in the diagram in paragraph 9.9, and in any case equal or greater than
the pump head’s value.
Along the duct, avoid localized diameter reductions that may cause pressure drops with subsequent cavitation.
Absolutely avoid 90
0
elbows, connections with other hoses, bottlenecks, counter-slopes, upside down “U” shaped
curves, “T” connections.
2. The selected lay-out must allow to avoid cavitation.
3. It should be perfectly airtight, and built in a way that guarantees perfect sealing over time.
4. Avoid pump emptying when stopping (even partial emptying).
5. Do not use hydraulic-type fittings, 3 or 4 way fittings, adapters, etc., since they may hinder the pump’s
performance.
6. Do not install Venturi tubes or injectors for detergent intake.
7. Avoid the use of standing valves, check valves, or any other type of one-way valves.