7 stepper motor inlet control, 8 capacity control system – Ingersoll-Rand 100-200 HP/75-160 KW User Manual
Page 44
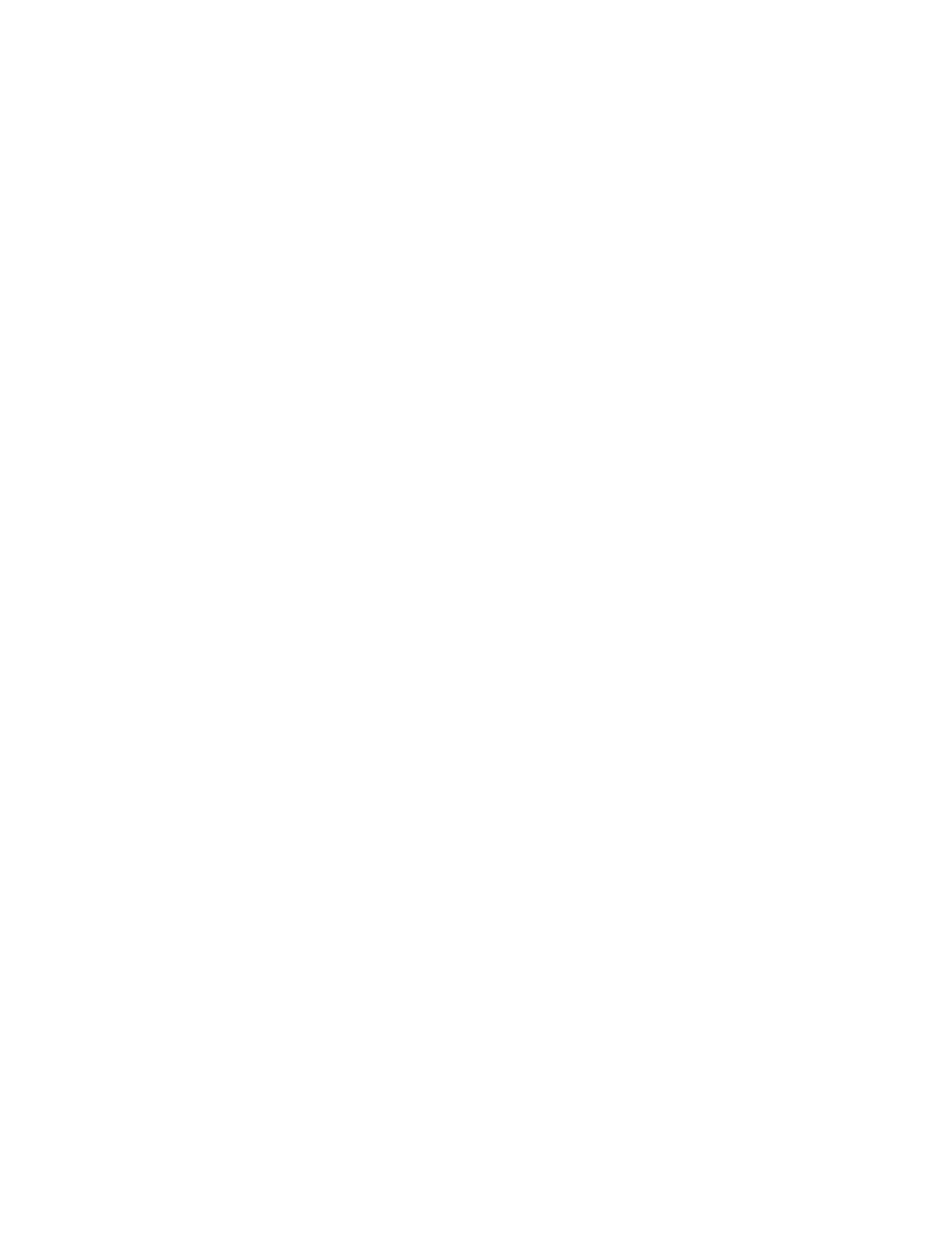
5.6 ELECTRICAL SYSTEM (Continued)
STAR-DELTA TYPE STARTER
By use of the Star-Delta type starter, the compressor
motor can be started and accelerated using a greatly
reduced “inrush” electric current. The starter is completely
automatic and controlled by the Intellisys controller. Refer
to the Electrical Schematic 8.1 in Section 8.0.
5.7 STEPPER MOTOR INLET CONTROL
The inlet valve is opened and closed by a stepper motor
mounted on the inlet valve. The Intellisys controller
regulates the stepper motor to precisely position the inlet
valve based upon the demand of the plant air system
(See Section 5.8).
The stepper motor is maintenance free. Bearings are
lubricated at the factory and sealed for life.
No adjustment of the stepper motor/inlet valve system is
required.
5.8 CAPACITY CONTROL
The SSR compressor is supplied, as standard
equipment, with three operator selectable capacity
control systems, each designed for different plant air
requirements:
— MOD/ACS (Modulation/Automatic
Control Selector)
— On-Off Line
— Modulation Only
The desired control is selected at the Intellisys control
panel (See Section 3.0).
AUTOMATIC UNLOADED START
The compressor will always start in the unload mode.
When unloaded, the inlet valve is nearly closed, the
blowdown solenoid valve is open (tank vented), and the
compressor is operating at minimum power. The Intellisys
will open the inlet valve slightly to maintain the proper
sump pressure to ensure positive coolant flow and
smooth, quiet operation. When the injected coolant
temperature is less than 120°F (49°C), a separator
(sump) pressure of 45-50 psig (3.1 - 3.4 bar) will be
maintained. When the injected coolant temperature is
above 120°F (49°C), a receiver pressure of 24-33 psig
(1.7 - 2.3 bar) will be maintained. The minimum pressure
check valve will prevent any backflow of air from the plant
air system during unloaded operation.
ON-OFF LINE CONTROL
For those plants which have a widely varying air demand,
on-off line control will deliver air at full capacity
(compressor maximum efficiency condition) or will
operate at zero capacity (compressor minimum power
condition). The compressor is controlled by the Intellisys,
responding to changes in plant air pressure. The
Intellisys/stepper motor opens the inlet valve and closes
the blowdown valve (3SV) whenever plant air pressure
drops below the on-line pressure set point. The
compressor will then operate to deliver full capacity air to
the plant system. If the plant air system pressure rises to
the off-line set point of the Intellisys, the inlet valve closes
and the blowdown solenoid valve opens the separator
vent line, allowing separator pressure to drop. The
compressor will continue to run with minimum power
draw.
MODULATION/ACS CONTROL
For those plants which have relatively high, constant
air-demand relative to the compressor capacity, the
recommended control mode is modulation.
The modulation control system retains the features of
on-off line control, but provides for throttling of the inlet
flow up to the modulation off line air pressure set point.
The throttling position of the inlet valve is controlled by
the Intellisys, allowing the stepper motor to “trim” the inlet
valve position as dictated by the line pressure.
The modulating pressure range is 10 psig (.7 bar).
Modulation begins when the line pressure reaches the
maximum modulation pressure setting minus 10 psig (.7
bar) and continues as/if the line pressure rises.
Modulation becomes stable when the compressor output
equals the plant air demand. When the modulation is at
the maximum modulation pressure setting the maximum
capacity reduction will be down to approximately 60
percent of the compressor rated capacity. If the air
demand has decreased to a level below the 60 percent
modulated output, the line pressure will increase slightly
to actuate the Intellisys, unloading the compressor and
venting the separator.
42