Hafler DH-200 User Manual
Page 5
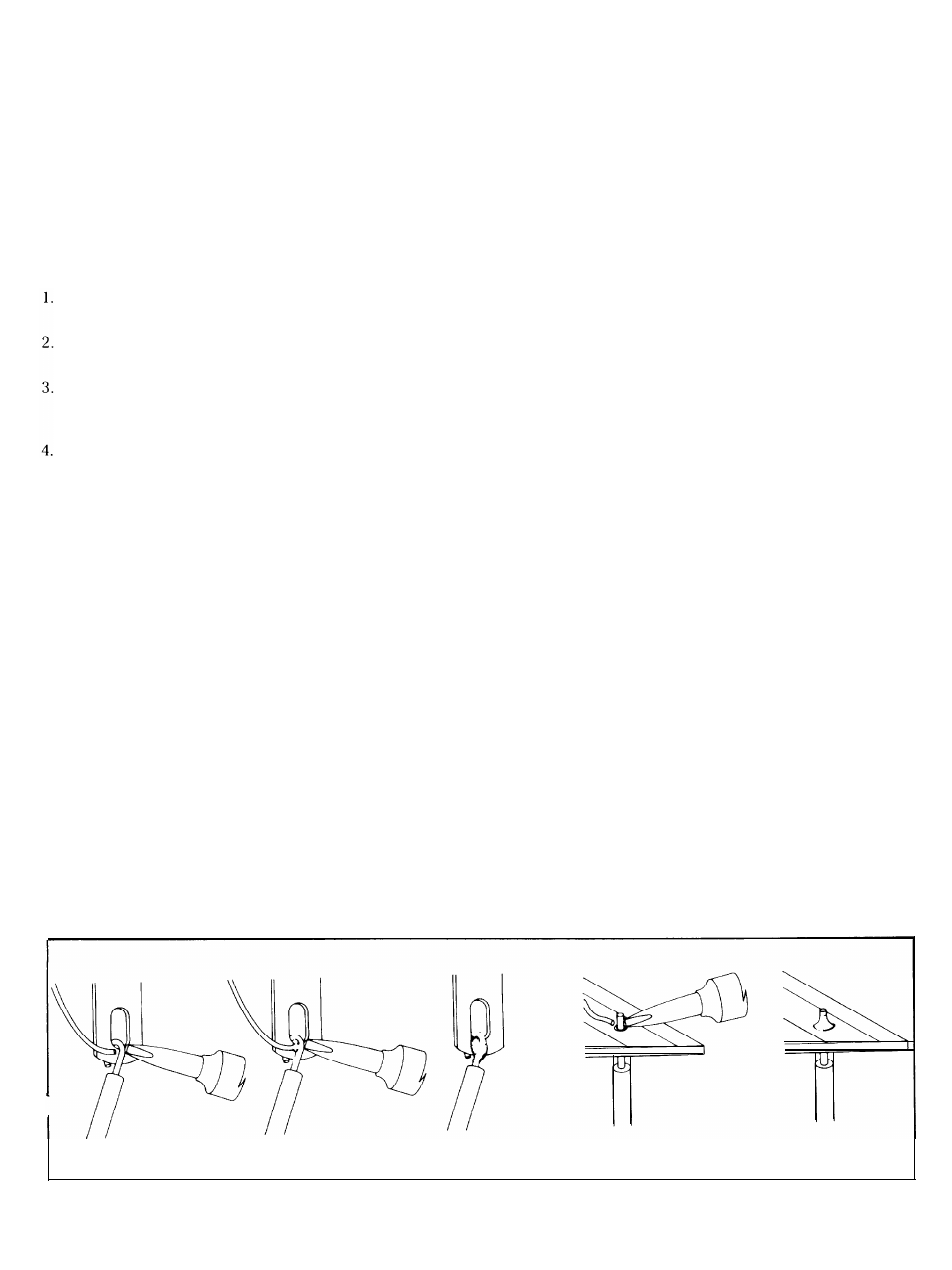
A soldering “gun” is not recommended. The unfamiliar user is
more likely to damage the etched circuit boards with its higher
heat potential and unbalanced weight. Also, because he may
not wait long enough for it to reach operating temperature each
time it is switched on, poor solder connections are more likely.
Pencil irons are much lighter and easier to use, and there is no
waiting time when solder connections follow in sequence, as in
kit building. Make sure you have a holder for it, though, and
always unplug it when you take a break.
Proper Soldering
There are four steps to making a good solder connection:
Make a good mechanical connection to hold the wire in posi-
tion while heat and solder is applied.
Heat thejunction of the wire and lug, or hole, with the bright,
shiny top of the iron.
After heating for a couple seconds, apply solder to the junc-
tion. It should melt immediately and flow smoothly around
both surfaces.
Allow the connection to cool undisturbed.
Remember that the connection is made by the solder, not by
mechanically attaching the wire to the terminal. Usually the
wire is looped through the lug and crimped in place, but some
prefer to just place it through the hole and rely on the stiffness of
the wire to hold it while soldering. Connections to numbered
holes on the circuit board are handled this way.
Good solder connections are essential for trouble-free noise-
free operation. A good solder joint does not require much solder
around the conductors. Never “butter” partially melted solder
on the joint, as it is useless. A good connection looks smooth and
bright because the solder flows into every crevice when the
parts are hot enough. The iron must have a bright, shiny tip to
transfer heat easily to the junction. That’s why the damp sponge
should be used frequently to wipe the tip, and occasionally you
must add a small amount of solder to the tip, too. If a connection
is difficult to heat, “wet” the tip with a small blob of solder to pro-
vide a bigger contact surface to the joint. Once the solder flows
around the conductors, any movement must be avoided for a
few seconds to allow a good bond. When cool, check the con-
nection by wiggling the wire. If in doubt, or if the connection is
not shiny, re-heat the joint. Excess solder may be removed from
a connection by heating it and allowing the solder to flow onto
the iron, which is then wiped on the sponge.
ALL SOLDER USED MUST BE ROSIN CORE.
Never use acid core solder or any separate flux in electronic
work. Silver solder is also not suitable. If in doubt about unmark-
ed solder, always obtain a fresh supply of rosin core solder. We
recommend 60/40 for easiest use. Do not confuse it with 40/60,
which is harder to melt.
The general procedure is to use a hot iron for a short time to
heat a connection, then add solder with the iron still in contact.
Remove the solder once it flows, and then remove the iron. A
cooler iron applied for a longer time is more likely to damage
components, or lift the copper circuit pattern from the boards. A
break in the etched circuit can be mended by simply soldering a
small piece of wire across it. Do not allow much build-up of
solder on the tip of the iron, or it may fall into adjacent circuitry.
When soldering to a numbered hole on the board, insert the
wire from the components side, and apply the iron, leaving
some bare wire exposed so that you can see that the hole is then
filled with solder for a secure bond. A round wooden toothpick
is suggested so that you can heat and clear the hole of solder if it
hinders your inserting the wire. Some builders prefer to clear
every hole first with a touch of the iron and toothpick. If the wire
has first been “tinned,” no additional solder may be necessary if
solder fills the hole, but it is good practice to push the wire
through, and then back it up a bit, to be sure solder fills the hole
from both sides. Make certain a bright, shiny flow is evident
from the wire, across the hole, onto the circuit pattern on the
board.
“Tinning” refers to the process of applying a light coating of
solder to the bared wire end. This keeps all the strands secured,
and also makes a good connection easier. Simply touch the wire
with the iron for a couple of seconds, and apply solder. Allow the
excess to flow away onto the iron. When properly done, the
wire is uniformly bright, and no larger than before. The hookup
wire supplied with this kit does not normally need tinning, for it
is pre-tinned.
5