Purge fittings, Removing a purge plug, Case purging procedure – Emerson CMF200A User Manual
Page 23
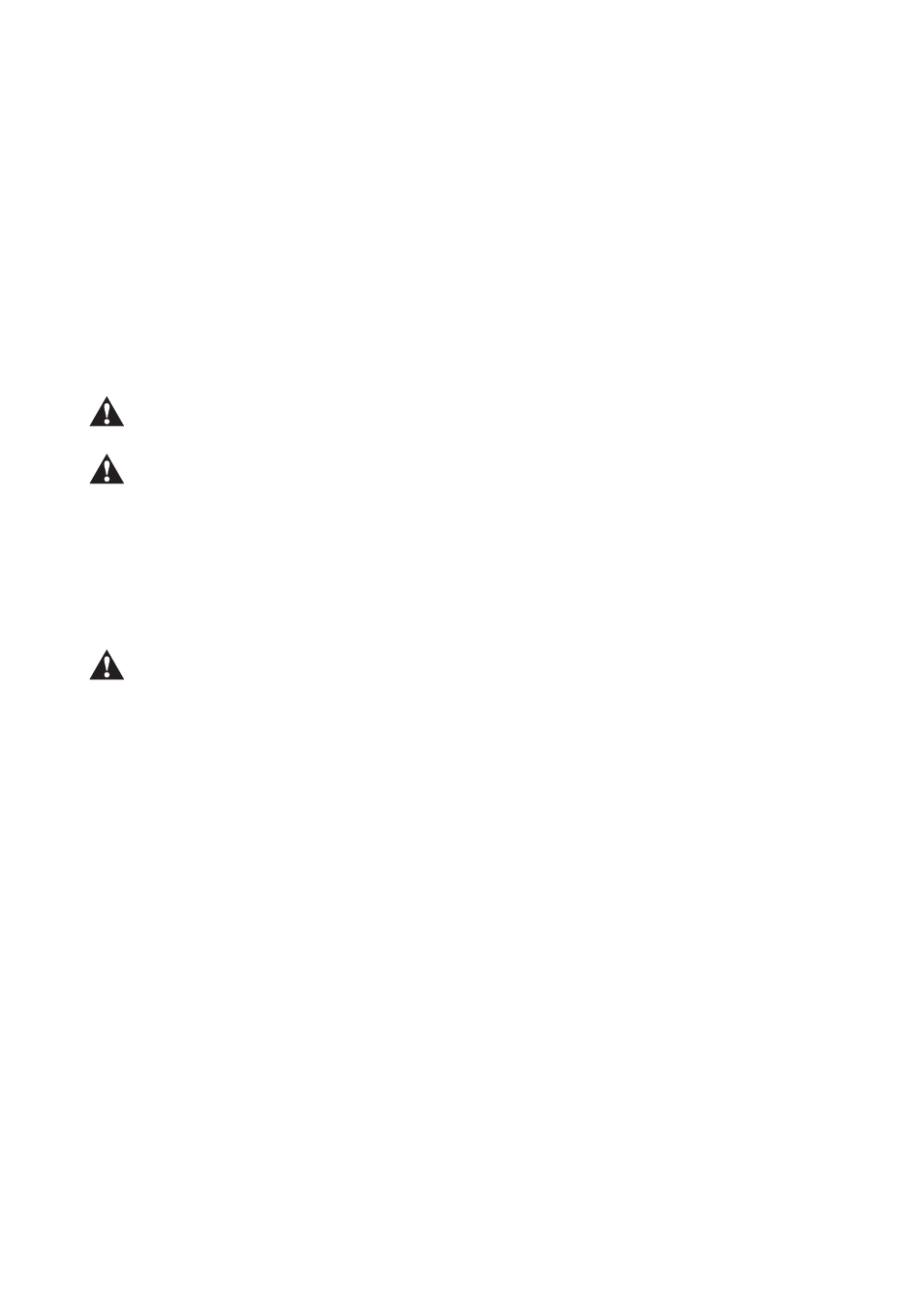
Installation Manual
21
Purge Fittings
Purge Fittings
If the sensor has purge fittings, they should remain sealed at all times. After a purge plug has been removed,
the sensor case should be purged with argon or nitrogen and resealed.
Purging the case protects internal components. The sensor is purged of all oxygen and sealed at the factory. If
the purge plugs are never removed, it is not necessary to purge or re-seal the sensor. For more information,
contact Micro Motion Customer Service.
Removing a purge plug
If a purge plug is removed from the sensor case, it will be necessary to repurge the case.
Removing a purge plug compromises the secondary containment of the sensor and could expose the
user to process fluid. Take all necessary precautions when removing purge plugs.
Improper pressurization of the sensor case could result in personal injury. Removing a purge plug will
require the sensor case to be repurged with a dry inert gas. Follow all instructions provided in the case
purging procedure.
Case purging procedure
Read all instructions before performing the case purging procedure. It is not necessary to perform this
procedure unless a purge plug has been removed.
1. Shut down the process, or set control devices for manual operation.
Performing the purge procedure while the flowmeter is operating could affect measurement accuracy,
resulting in inaccurate flow signals. Before performing the case purging procedure, shut down the
process, or set control devices for manual operation.
2. Remove both purge plugs from the sensor case. If purge lines are being used, open the valve in the
purge lines.
3. Prepare the purge plugs for reinstallation by wrapping them with 3–5 turns of Teflon
®
tape.
4. Connect the supply of nitrogen or argon gas to the inlet purge connection or open inlet purge line.
Leave the outlet connection open.
• Exercise caution to avoid introducing dirt, moisture, rust, or other contaminants into the
sensor case.
• If the purge gas is heavier than air (such as argon), locate the inlet lower than the outlet, so the
purge gas will displace air from bottom to top.
• If the purge gas is lighter than air (such as nitrogen), locate the inlet higher than the outlet, so the
purge gas will displace air from top to bottom.
5. Make sure there is a tight seal between the inlet connection and sensor case, so air cannot be drawn by
suction into the case or purge line during the purging process.
6. The purge time is the amount of time required for full exchange of atmosphere to inert gas. For each
sensor size, the purge time is different. Refer to Table 5. If purge lines are being used, increase the
purge time to fill the additional volume of the purge line.
7. Avoid pressurizing the sensor case. At the appropriate time, shut off the gas supply, then immediately
seal the purge outlet and inlet connections with the purge plugs. If pressure inside the case elevates
above atmospheric pressure during operation, the flowmeter density calibration will be inaccurate.
8. Make sure the purge fitting seals are tight so air cannot be drawn by suction into the sensor case.