LowFlow 8000 Series Control Valve User Manual
Page 3
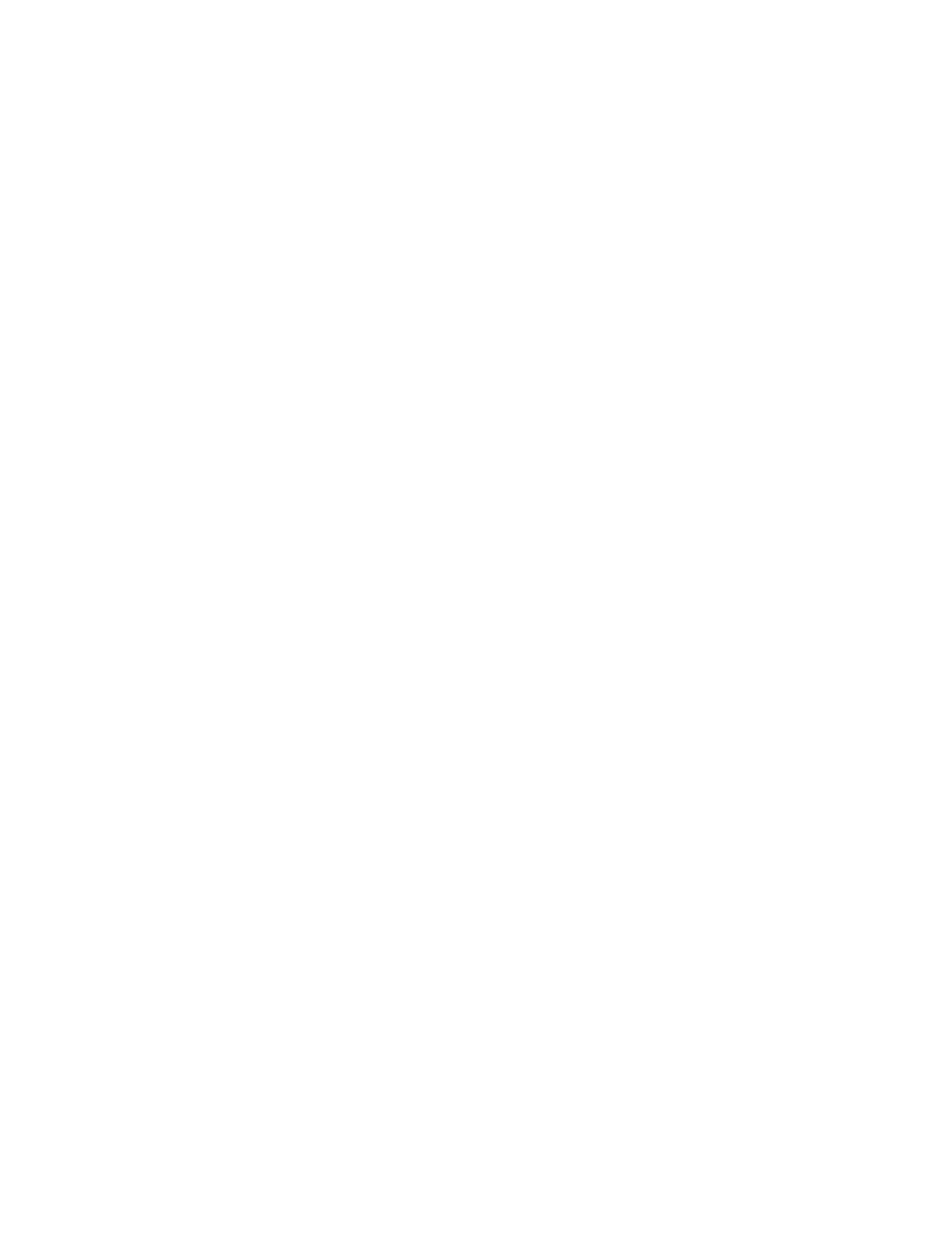
-3-
each ring down firmly into place with a tube.
4.
After the packing is installed, assemble the packing
adapter (7), and packing nut (11). Tighten the nuts
hand-tight.
5.
The final packing adjustment should be made with
the valve pressurized and the packing tightened
just enough to stop any leakage, while stroking the
valve. Excessive tightening could cause the stem to
stick and result in improper valve operation due to
high friction forces.
Section 2: Actuator to Valve Disassembly
Direct Acting Actuator: ATC (Air-to-Close)
1.
Shut off pressure to actuator, and remove the supply
tubing from the actuator case.
Reverse Action Actuator: ATO (Air-to-Open)
1.
Apply approximately 6 psig air pressure to the ac-
tuator to lift the plug off the seat.
2.
Remove the actuator from the valve as follows: loos-
en the two stem nuts (36) and move them down the
stem (33). Lock these nuts together. Remove the two
nuts (31) that secure the support legs (16B) to the
actuator mounting flange (9). Using a wrench on the
nuts and on the flats of the stem adapter (46), turn
the valve stem (while holding the stem adapter in
place) until the stem disengages. The actuator will
now be free from the valve. Caution: Do not lose
the spacers (38) – they will disconnect from the
support legs when the actuator is removed from
the mounting flange
.
BODY & BONNET DISASSEMBLY
1.
Remove packing nut (11) and bonnet nut (8).
2.
Remove stem nuts (36) from stem (33) and pull up on
stem before unthreading bonnet (2) from body (4).
3.
Remove the stem (33) from the bonnet (2).
4.
With a socket wrench, remove the seat (35) from the
body.
5.
Soft seats are disassembled by removing the soft
seat assembly (48) from the body.
6.
Clean all parts with an approved, non-residue form-
ing solvent. Remove encrusted material with a very
fine Crocus or aluminum oxide cloth. However, do
not use these abrasives on the seating surface or
the trim surface (that portion of the plug that enters
the seat bore). The machining tolerances on these
surfaces are so closely controlled that you might
change the valve's flow characteristics.
7.
Inspect all parts and replace any badly worn or
damaged parts.
Do not attempt to resurface seating surfaces of the
plug or seat. Seat and plugs are only sold in factory
matched sets. It is always advisable to replace seals and
gaskets.
Section 3: Valve Reassembly: Body
1.
Lubricate the hard seat (35) or soft seat (48) threads
with a suitable lubricant such as NO-LOK and thread
the seat into the body (4). Torque to 20 ft-lbs (240 in-
lbs).
2.
Guided Trim: coat the guided portion of the plug
(34) with Molykote G-Rapid Spray lubricant or an
equivalent light lubricant suitable for your service.
Assemble the plug to the stem.
3.
Insert the stem (33) and plug (34) into the bonnet (2)
and install the packing as described in Section 1.
4.
Plastic Valves Only: place the o-ring (49) around the
base of the bonnet.
5.
Pull the stem up in the bonnet before threading the
bonnet (2) into the body (4).
6.
Push down on the stem to allow the plug (34) to cen-
ter itself in the seat (35).
7.
Reassemble the two set nuts (36) onto the stem (33)
threads and lock the two nuts together.
8.
If the actuator is reverse acting (ATO), apply ap-
proximately 6 psig air pressure to the actuator.
9.
Install the spacers (38) onto the support legs (16B)
and insert the support legs into the actuator mount-
ing flange (9). Thread the stem (33) into the stem
adapter (46) at least four complete turns, holding
the stem adapter with a wrench to prevent it from
turning. If the support legs are still not in full contact
with the actuator mounting flange, thread the stems
together until full contact is achieved and install nuts
(31) onto the support legs and tighten.
10. Thread both stem nuts (36) up and tighten them
against the stem adapter (46).
Section 4: Actuator Spring Pre-Load Adjustment
(Bench Setting)
1.
The two stem nuts (47) should be loosened and
threaded down the stem and then locked together.
2.
A regulated air supply must be provided to the ac-
tuator. Connect the air to the lower actuator case
(16A) for reverse action or to the upper actuator
case (17A) for direct action actuators.
3.
Standard actuators have ranges of either 3-15 psig or
6-30 psig. The range is stamped on the valve name-
plate. These instructions will assume that the range is
3-15. If yours differs, substitute the appropriate pres-
sure where these instructions refer to 3 psig.
Direct Acting Actuator: ATC (Air-to-Close)
1.
The spring preload adjustment may be made with or
without pressure in the valve body.
2.
Spring preload is adjusted by threading the stem
adapter (46) into the actuator stem (22). Keep the
actuator stem from turning with a wrench and turn
the stem adapter. Threading the stem adapter into
the actuator stem increases preload while threading
out decreases preload.
3.
Slowly increase the air pressure up to 3 psig while
observing the stem for movement. Correct spring
preload is when the valve stem starts to move when