Start-up procedure, Maintenance – LowFlow 8000 Series Control Valve User Manual
Page 2
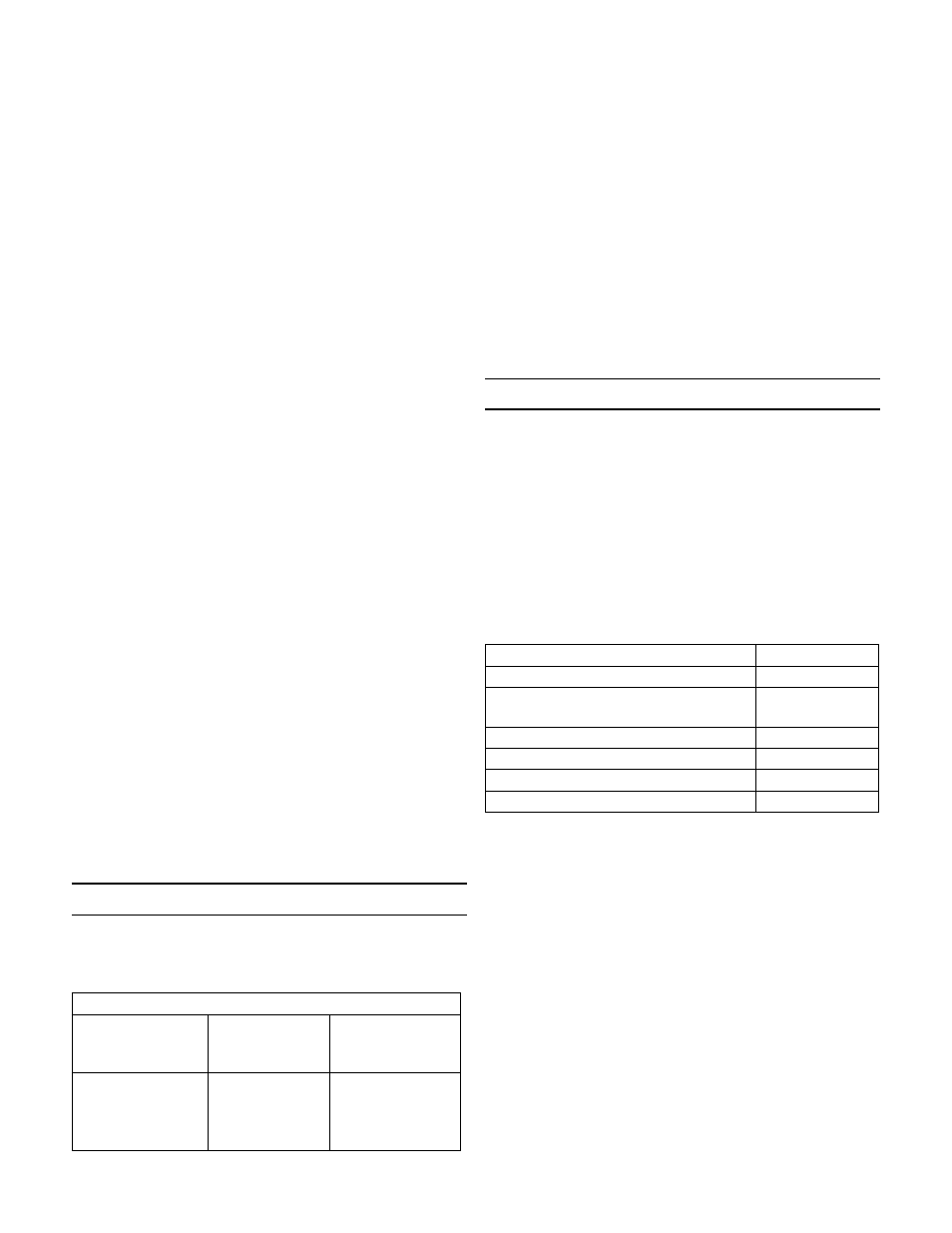
•
Safety relief valves may be leaking
•
Valve stroke may be out of adjustment or there may
be foreign matter in the valve preventing full plug
movement
•
Slowly open the inlet shutoff valve.
•
Slowly open and close the outlet shutoff valve sev-
eral times. This fully strokes the valve to insure sat-
isfactory operation.
If You Experience Insufficient Flow:
•
Check shutoff valves to be sure they are fully open
•
Inlet pressure to the valve may be insufficient to pro-
vide the needed flow - check the inlet pressure with
a pressure gauge
•
Strainers should be checked for clogging - blow-
down if needed
•
Steam traps may need reconditioning
•
Dirt in the trim may prevent the valve from passing
its full capacity
•
Diaphragm failure in reverse acting (air-to-open)
actuators would prevent the valve from properly
stroking open
•
Insufficient air pressure to reverse acting (air-to-
open) actuators would prevent the valve from prop-
erly stroking open.
If You Experience Overpressure (Outlet):
•
Dirt in the trim may be preventing the valve from
shutting off
•
Diaphragm failure in direct acting (air-to-close) ac-
tuators would prevent the valve from properly strok-
ing closed
•
Insufficient air pressure to direct acting (air-to-close)
actuators would prevent the valve from properly
stroking closed
•
Incorrect actuator spring adjustment in direct acting
(air-to-close) actuators would prevent the valve from
properly stroking closed.
If You Experience Leakage:
•
Excessive pressure drop across the valve could
prevent the valve from shutting off properly. Check
the catalog ratings for the maximum allowable pres-
sure drop for your trim, action and actuator.
Start-Up Procedure
1.
Be sure that the action of the control valve and of
the controller are such as to give the desired results.
See part D to change the valve action if necessary.
Controller Action
If an increase in
pressure or
temperature must
And the action
of the valve is
And the action
of the controller
must be
close valve
close valve
open valve
open valve
air to close
air to open
air to close
air to open
direct
reverse
reverse
direct
2.
The control valve has been pre-set by Low Flow
Valve. However, finer adjustments may be required
to compensate for pressure drop conditions of the
application.
3.
With the inlet, outlet, and by-pass shutoff valves
closed, and no pressure in the downstream line,
fully open the shutoff valve. Slowly open the inlet
valve just enough to start flow through the control
valve. Increase flow gradually by slowly opening the
inlet shutoff valve. Do not fully open the inlet valve
until you are sure the controller and control valve
have control of the system. Usually, the handwheel
on the inlet valve will turn freely when this point is
reached.
4.
To shut off the line fluid, close the inlet shutoff valve
first, followed by the outlet shutoff valve.
Maintenance
Warning: Be sure that there is no pressure in the valve
before loosening any fittings or joints. The following
steps are recommended:
1.
Close inlet shutoff valve and by-pass valve.
2.
Allow pressure to bleed off downstream.
3.
When inlet pressure gauge shows that there is no
pressure in the valve, close the outlet shutoff valve.
TO REDUCE MAINTENANCE TIME, REFER TO PROPER
FIGURE AND FOLLOW STEPS INDICATED BELOW FOR
APPLICABLE MAINTENANCE OPERATION.
Proposed Maintenance
Follow Steps
Renewing Valve Stem Packing
Section 1
Valve Disassembly - Inspect Parts -
Replace Valve Plug or Seat Ring
Section 2
Valve Reassembly
Section 3
Actuator Spring Preload Adjustment
Section 4
Actuator Maintenance
Section 5
Changing Valve Action
Reversing Action
Section 1: Packing Replacement
Renew the stem packing whenever there is leakage that
cannot be stopped by a light adjustment to the packing
flange. Additional rings can be added to the packing set
to overcome minor packing leakage and provide for ad-
ditional adjustment space. This can be done without dis-
mantling the valve.
1.
Remove the actuator from the bonnet. (See VALVE
DISASSEMBLY, SECTION 2).
2.
Completely remove all of the old packing (6) and
discard. Clean the valve stem (33) and packing
box thoroughly. If necessary, the valve stem may be
dressed with a very fine Crocus cloth, but generally
it is best not to as the stem has a fine machined fin-
ish. Use an approved non-residue forming solvent
for cleaning. Wipe dry with a clean cloth.
3.
Insert a new packing set in the packing box. Press
-2-