Iqpump 7 ac drive, Simplex quick start procedure, Page 3 of 4 – Yaskawa iQpump 7 AC Drive User Manual
Page 3: Auto operation – power down storage
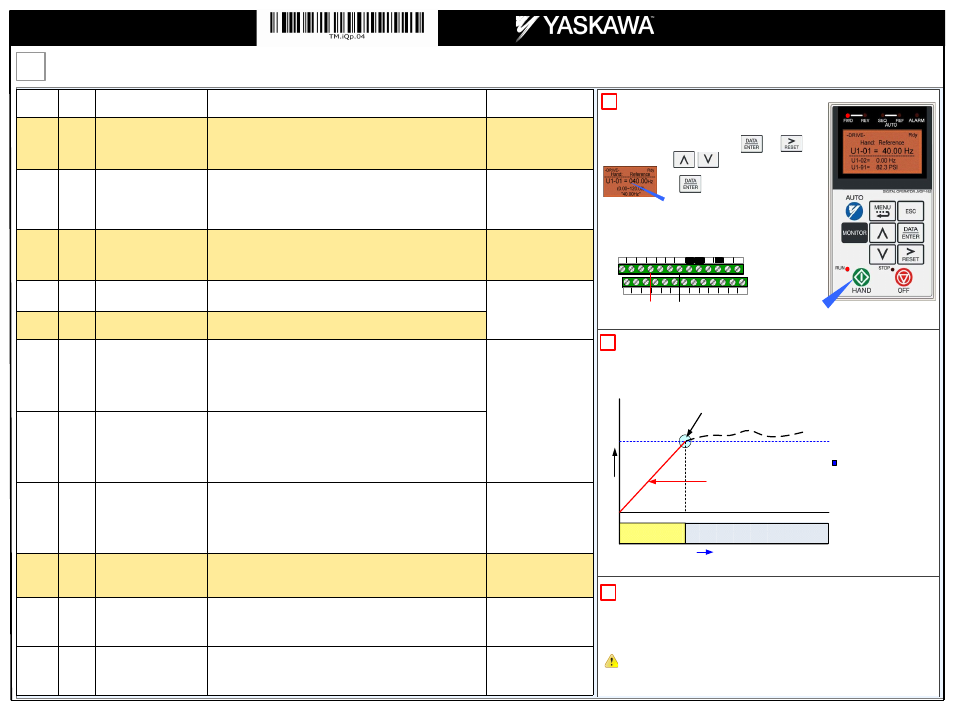
Parameter
Value
Description
Reference
Comments
b5-03
3.0 sec.
PI Integral Time
Decrease integral time to make iQpump more responsive.
Caution: can cause instability if
value is too low.
b5-12
2
(Fault)
PI Feedback Reference Missing
Detection Selection
Select what to do when the feedback device (transducer) fails or gets disconnected.
0: Disabled, continue running no message is displayed
1: Alarm, show warning on the keypad when the feedback device fails or is disconnected
2: Fault, stop pump system when the feedback fails or is disconnected
NOTE: Disable parameter b5-12
if no transducer is installed.
b5-14
2.0 sec.
PI Feedback Loss Detection Time
Delay time before iQpump shows alarm or fault when feedback device has failed or is
disconnected. Example: 2.0 sec., iQpump displays alarm or fault 2 sec. after the device has
failed or is disconnected.
C1-01
20.0 sec.
Acceleration Time 1
Time it takes to accelerate the pump motor from zero to maximum speed.
Adjusted depending on system
performance
C1-02
10.0 sec.
Deceleration Time 1
Time it takes to decelerate the pump motor from maximum speed to zero.
L5-01
5
Number of Restart Attempts
Determines the number of times iQpump will perform an automatic restart on the faults listed
in the comments column.
iQpump System Protection Faults that can be setup to restart are Low Level Feedback,
High Level Feedback, Transducer Loss, Not Maintaining Set-point, Loss of Prime,
Pump Over Cycle. Refer to parameters P4-07 and P4-08. The number of restart attempts is
set by L5-01.
x
Overcurrent
x
Ground Fault
x
Output Phase Loss
x
Input Phase Loss
x
iQpump Overload
x
Motor Overload
x
Overtorque
x
DC Bus Fuse Blown
x
DC Bus Undervoltage
x
DC Bus Overvoltage
x
Overheat
L5-03
20 sec.
Maximum Restart Time After Fault
If the restart fails (or is not attempted due to a continuing fault condition) iQpump waits the
Maximum Restart Time After Fault, before attempting another restart.
P1-06
40.0 Hz
Minimum Pump Frequency
Minimum speed (Hz) the pump motor has to operate at.
Example: Base pump motor speed is 3600 RPM, minimum speed is 2400 RPM. Set minimum
pump frequency to 40.0 Hz. (2400 ÷ 3600 x 60 Hz = 40 Hz)
P1-06 should be set to the level
where the pump can produce the
minimum pressure even at zero
flow.
P2-03
5 sec.
Sleep Delay Time
Time it takes before the pump system goes to sleep when the selected signal level (P2-01)
falls below the specified sleep level (P2-02)
Adjust according to system
requirements.
P4-05
30.0 Hz
Thrust Bearing Frequency
Sets the frequency reference used when the thrust bearing function is active. A value of 0
disables this function.
Primarily used for submersible
pumps. Program P4-05 = 0.0 Hz
to disable function when iQpump
is used with a centrifugal pump.
P4-11
0.2 Min
Utility Start Delay
When utility power is restored and P4-10 is enabled (1), iQpump waits the time specified in
P4-11 before auto operation becomes active.
Note: Only active when P4-10 is
enabled (1) and operation
(start/stop) is from the
digital operator.
Step
5
iQpump Factory Defaults Overview (only adjust settings based on your application)
THRUST BEARING - SUBMERSIBLE MOTORS (e.g. Franklin)
When using a submersible motor in combination with iQpump, it is recommended to use the Thrust Bearing
function to prevent excess motor wear. To enable this function, enter the minimum motor frequency in parameter
P4-05. Example: Minimum motor speed 1800 RPM, 1800 RPM ÷ 3600 RPM x 60.0 Hz = 30.0 Hz
Output Frequency
Output Frequency
Thrust Bearing Frequency P4-05
(Example 30.0 Hz)
Time
Thrust Bearing
Auto/Hand Operation
Turn Off Thrust Bearing Function
(Output Frequency Reached)
P
4-0
4
A
cc
el
. T
im
e
Thrust Acceleration Time P4-04
(Example 1.0 sec.)
C1-01 Acceleration Time
5
AUTO OPERATION – POWER DOWN STORAGE
6
Allows iQpump to automatically start after power failure when operated from keypad / digital operator. This function
is recommended for use when operating the iQpump in remote / unmanned areas.
When the iQpump is powered down while running, an internal run
command will automatically be initiated upon power-up.
HAND MODE OPERATION
4
Hand Mode speed can be adjusted by pressing , use
to move the cursor and to adjust the hand speed reference.
Press to save new active hand speed reference.
Hand Speed from the Keypad/Digital Operator (Default)
Set parameter P5-01 ‘Hand Mode Ref.’ to ‘0’ to adjust the hand mode
reference from an external 0 – 10V signal connected to terminal A1 and AC.
Hand Speed from Analog Input (0 – 10V)
S3
S5 S6 S7 FM AC AM IG
S2
S4
S1
S+ S-
SP
A2 +V AC
AC
SC
A1
SN
R+ R-
+
-
0 – 10V
Press the HAND KEY on the digital operator to run the system in Hand Mode.
‘0’ Blinking
HAND KEY
Note:
Hand Key can be disabled with parameter P5-04
Note: Thrust Bearing Function is Enabled by Default
Page 3 of 4
iQpump 7 AC Drive
(Software 0034)
Simplex Quick Start Procedure