Maintenance, 4 maintenance – Tecfluid TM Series User Manual
Page 8
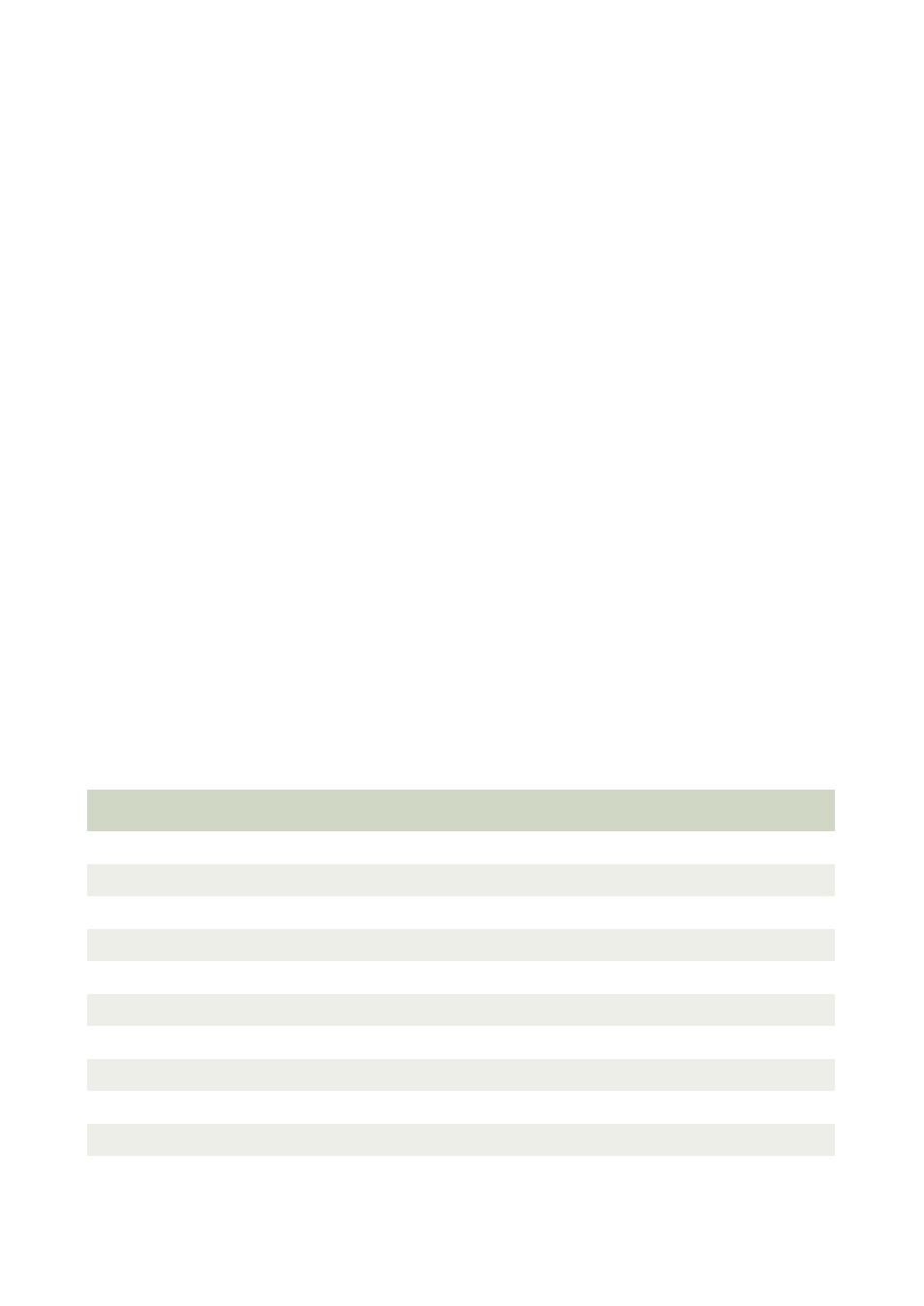
8
The terminals are numbered 1 to 3 and the connection is as follows:
Nº 1:
Ground
Nº 2:
Coil
Nº 3:
Coil
Before soldering the connections, unscrew the cable gland and feed it, together with the
electrical connection protector housing, over the cable.
The joint between the cable and the connector should always be soldered, and should be
tidy and without short circuits between terminals.
Peel the outside insulation to free the inner cables. It is recommended to tin the ends of
the wires to avoid loose ends.
Once the connections have been made, the housing should be mounted screwing it on
and then the cable gland should be tightened to avoid entry of any liquid or humidity.
Once assembled the half of the connector, the mounting in the base has only one position
defined by the keyway between the two parts.
Check that the rubber seal is in its position inside the connector base. If this is the case,
introduce the connector half in the base, positioning by the keyway, and screw on the nut
until the end of the thread is reached.
4 MAINTENANCE
The simple construction of the TM turbine results in a long life in normal working
conditions.
The life of the parts depends mainly on the abrasive characteristics of the product to be
measured and the maximum flow rate.
The combination of these two factors make it difficult to estimate the life of the
components in good working conditions.
If the maximum flow rates given for each DN in the following table are exceeded the life is
considerably reduced.
Flow ranges
DN
Minimum flow
rate (m³/h)
Maximum flow
rate (m³/h)
Pressure drop (mm H
2
0) at
maximum flow rate
Maximum intermittent
flow rate (m³/h)
15
0,3 3
7500
5
20
0,6
6,8
7500
8
25
0,9 13,5
7000
16
40
1,9
30
5600
40
50
5 50
2800
60
65
9
90
2400
115
80
15 150
3100
180
100
28
280
4500
340
125
45 450
2400
560
150
65
650
2500
820