Rotary encoder aligment, Installation instructions – MicroE 1200 Mercury User Manual
Page 9
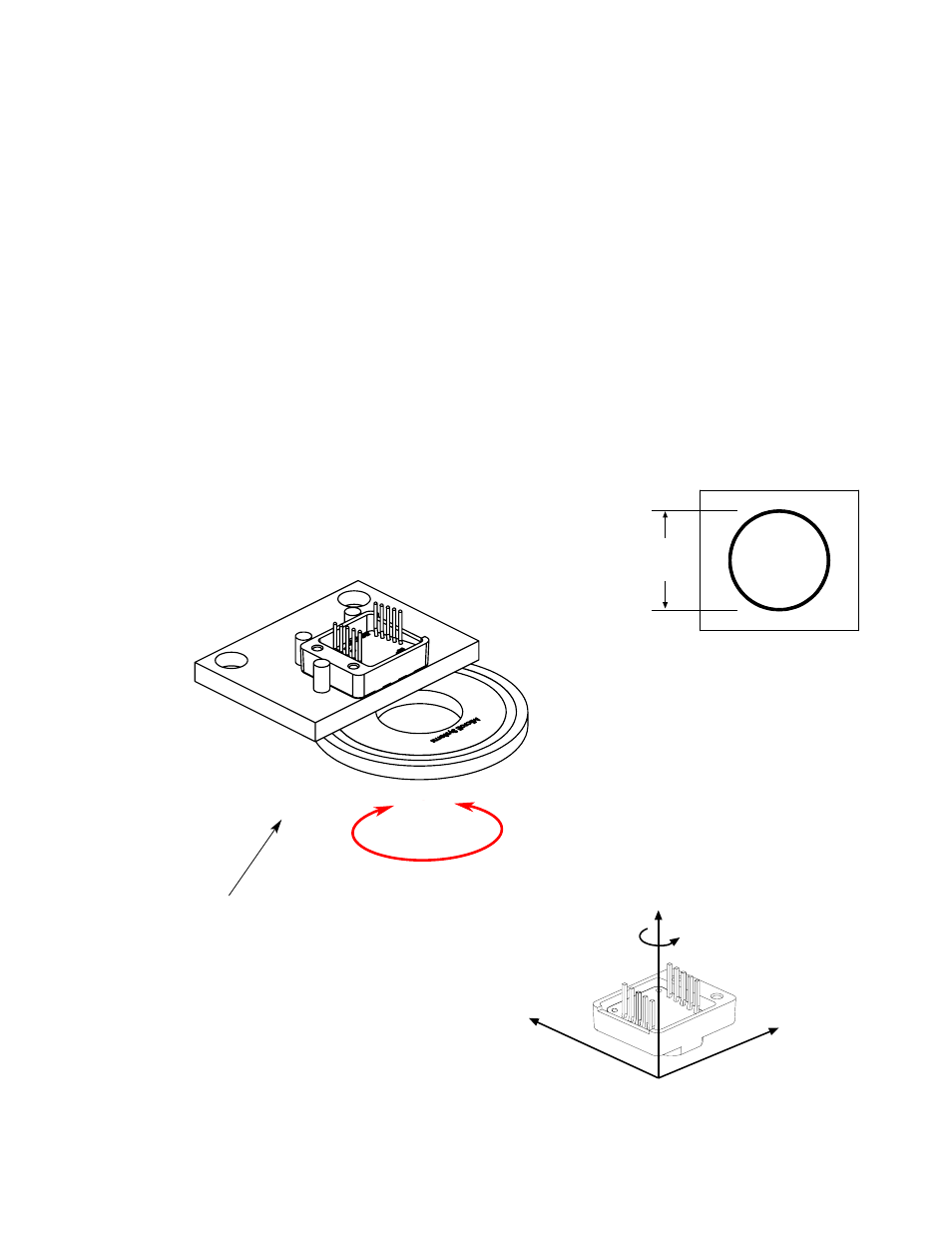
Installation Instructions
Rotary Encoders
Page 7
5
Confirm proper alignment over
the full range of motion.
If not aligned over the entire
range of motion, loosen the
sensor mounting screws and
repeat step 4.
4
MAIN TRACK ALIGNMENT
If benching dimensions cannot be provided, proper sensor alignment may require minor adjustments
to the sensor head position with respect to the scale. This can be performed by maximizing the
sin/cosine signals from the M1200 or M1500P.
Using an oscilloscope in the X/Y mode, monitor the sin/cosine signals (refer to the interface drawing
for pinouts) while moving the sensor head. Slowly move the sensor head by allowing it to slide on the
mounting surface until 0.80 volts peak-to-peak +/- 20% is obtained. Tighten the mounting bracket
screws.
INDEX TRACK ALIGNMENT
The M1200 or M1500P must be aligned for both the main and index tracks. When properly aligned,
the sensor will produce an index window as the sensor head passes over the index mark. The index
window is roughly one fringe wide (20µm). To verify proper index track alignment, use a digital
oscilloscope triggered on the index window. Refer to the interface drawing for the pinout.
To align the sensor head,
move it in the X, Y or
θ
z
directions.
0.80 v
Single Ended
Lissajous pattern as seen on a
scope
θ
z
Y
X