Groth 8860 User Manual
Page 7
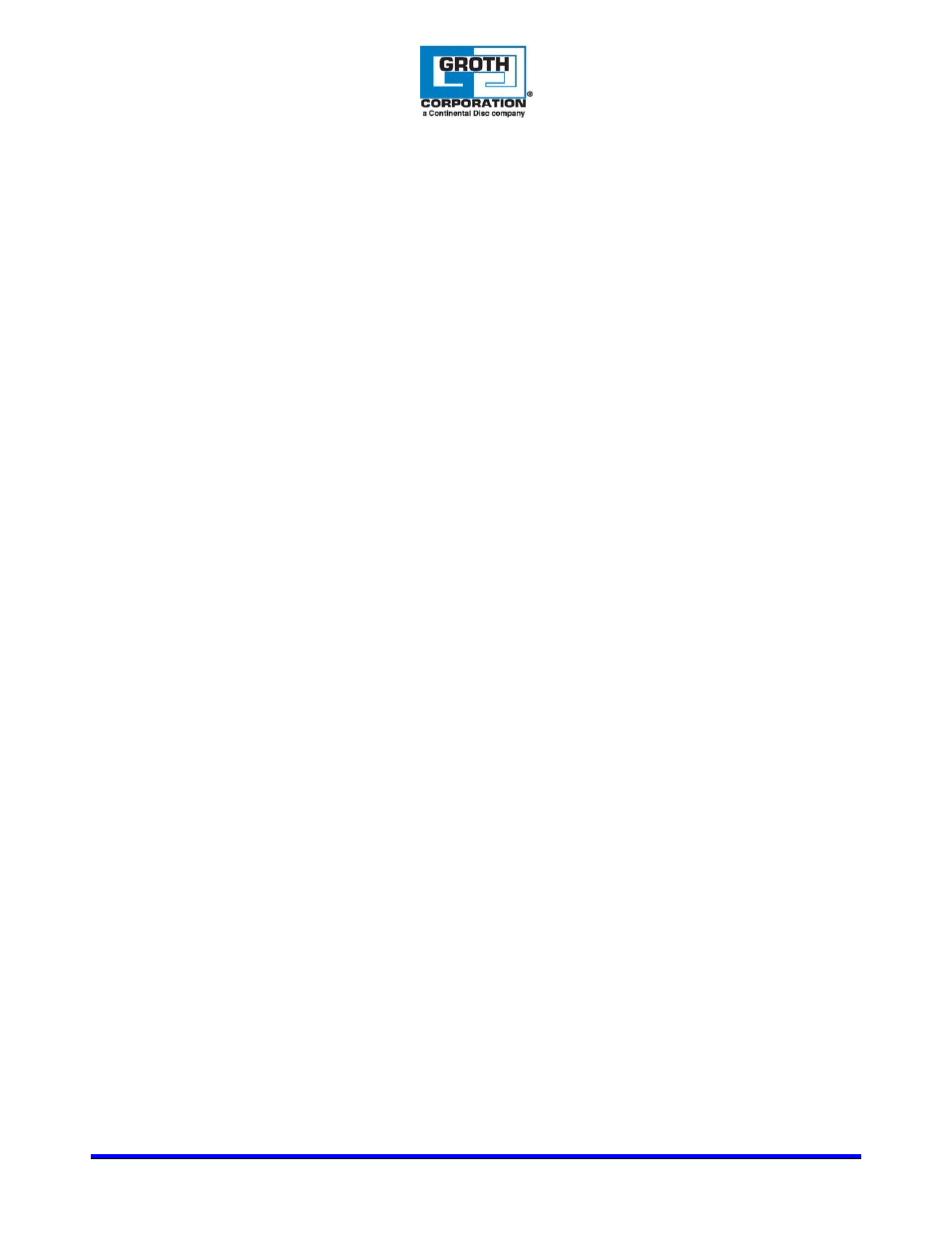
IOM -8860
Page 7 of 13
13650 N. Promenade Blvd. * Stafford, TX 77477
Office: (281) – 295-6800 * (800) – 354-7684 * Fax: (281) – 295-6999 * www.grothcorp.com
5. Lubricate all studs and nuts with an appropriate thread lubricant. If stainless steel fasteners are
used, use an anti-seize lubricant such as moly-disulfide.
6. Align flanges and gaskets. Make sure the flow path is not restricted by valve or gasket
misalignment.
7. Install nuts and lock washers and torque all fasteners to half the value listed in Table 2 below in a
staggered, alternating pattern.
8. Make sure that the flanges are not distorted and that the gasket is evenly compressed.
9. Make up the final torque and check that no further nut rotation occurs at the specified torque value.
Regulator flow capacity is based on a fully open regulator flowing air or a vapor with SG=0.7. Consult
factory for capacity under other conditions.
The regulator sense line is to be connected to the process line at a location at least ten feet upstream
with a minimum of .31" ID tubing. The sense port on the regulator is on the lower surface of the
actuator housing (see Figure 1). This line must be kept open and unobstructed to ensure that the
regulator "senses" the actual line pressure. Long sense lines may require a larger diameter and care
must be taken to assure that the line is self-draining. For some applications, a nitrogen purge may be
required to ensure that this line remains open. Consult the factory for recommendations for remote
installations or vapors that may cause line obstructions.
All system piping must be free of weld slag and other debris before installing the regulator.
V. OPERATION
The regulator is set at the factory. The pressure setting can be changed while installed in the process
piping system. The purpose of the regulator is to maintain set pressure at some point upstream in the
process, such as in the anaerobic digester tank. System pressure shall be monitored at this point.
Set pressure is set at the factory according to purchasing specifications. The range of set pressure for
standard springs are shown in Table 3. Other ranges are available with special springs. The factory
setting and spring range are shown on the nameplate. The regulator will not function properly if the
setting is outside this range. If higher or lower settings are required, the necessary components can be
obtained from Groth Corporation.
For in-line adjustment, a visible scale shows the approximate set pressure. From this setting, small
adjustments can be made while observing upstream system pressure. Remove the cap [1] and turn the
adjusting screw counter-clockwise to increase pressure or clockwise to decrease pressure. Replace
the cap when adjustment is complete.