Groth 1401E User Manual
Page 5
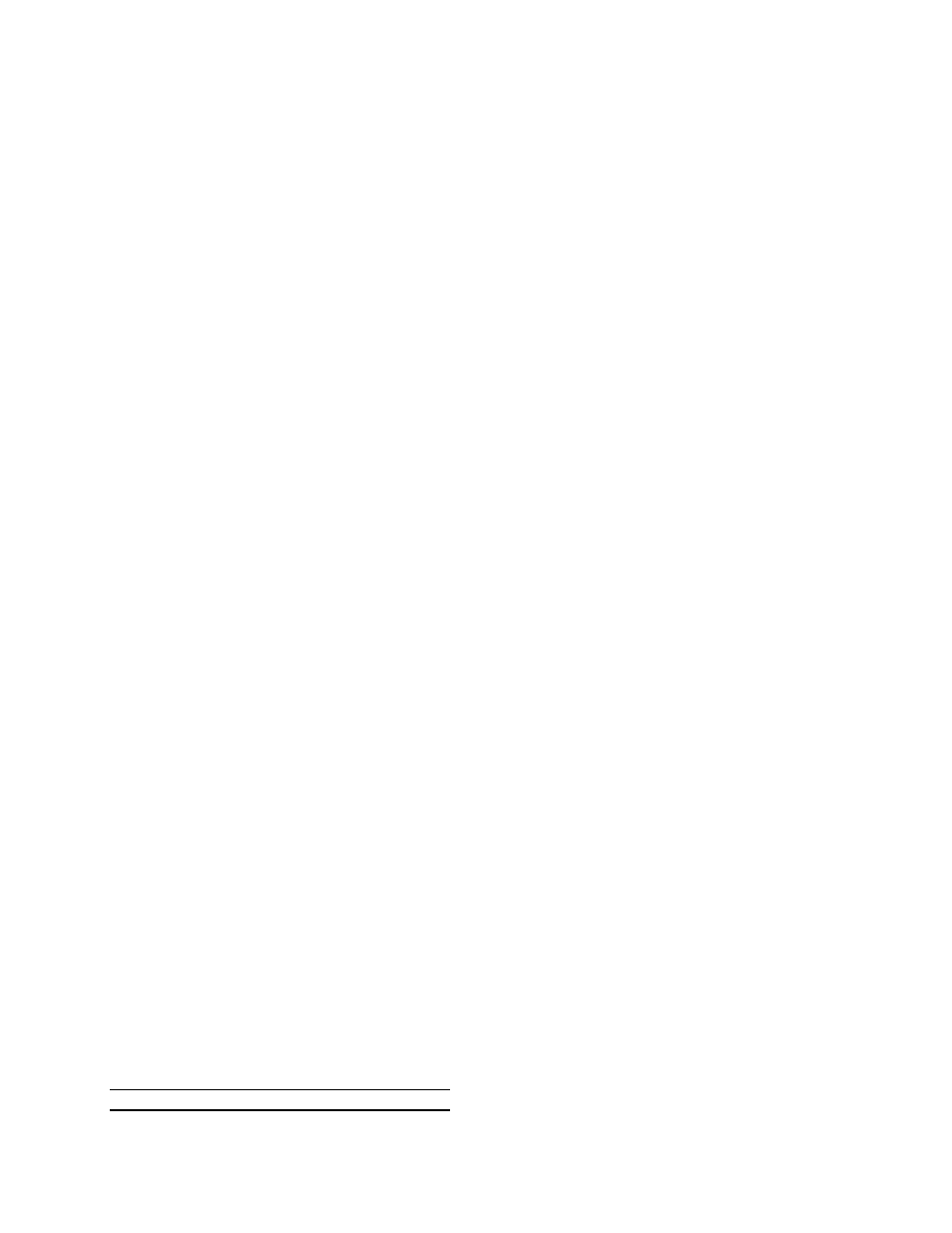
4
Pilot valve set pressure and blowdown are set at the
factory per purchase specifications. The set pressure
and range of adjustability are stamped on the
nameplate. DO NOT attempt to readjust the set
pressure beyond the limits specified on the nameplate
and in Table 2.
The pilot sense line is 3/8" OD SS tubing. It must be
kept open and unobstructed to ensure that the pilot
"senses" actual tank pressure. For applications
where tank vapors may condense or "polymerize" in
the sense tube or pilot valve, a nitrogen purge may
be required to prevent internal obstruction of the
tube. Consult Groth Corporation for
recommendations.
DO NOT attempt to remove the pilot valve from the
pressure relief valve without removing or isolating
the relief valve from the system. ALTERNATIVE
MEANS OF PRESSURE RELIEF MUST BE
PROVIDED WHEN THE VALVE IS OUT OF
SERVICE. After isolating the relief valve, bleed all
pressure from both relief and pilot valves before
removing the pilot valve.
Both pilot and pressure relief valve are exposed to
process vapors. Observe all plant procedures and
Material Safety Data Sheets for the products in the
system when inspecting, adjusting or servicing the
valves. Vents on the body and spring bonnet of the
pilot valve must be clean and unobstructed for
proper and safe operation of the valve. These vents
should be inspected periodically. Back out set
pressure adjusting screw to relieve all spring
pressure before removing the spring bonnet.
Blowdown needle chamber is exposed to system
pressure. The screw may be adjusted from nearly
contacting the seat (screw bottomed out) for snap
action to partially retracted for maximum
modulation. The screw is retained by the blowdown
bushing. DO NOT remove the blowdown bushing
while under pressure.
The tank pressure required to discharge the normal
or emergency venting requirements of the tank will
be increased by the amount of back pressure in the
discharge header. Maximum possible discharge
header pressure must be considered when sizing the
pressure relief valve.
INSPECTION AND INSTALLATION
The pilot valve or pilot operated pressure relief valve
is packaged and supported to prevent damage or
contamination during shipping. It should be
similarly protected during subsequent handling and
storage. Always keep all ports plugged to prevent
intrusion of foreign materials. Before installation,
inspect the unit visually. If there are indications of
physical damage or internal contamination, the valve
must be disassembled, cleaned and inspected before
installation. The spring adjustment cap and
blowdown screw locknut must be secure. Report any
shipping damage to your carrier.
The pilot valve is installed on the top port of the
relief valve actuator with a 1/2" Sch. 40 pipe nipple
of minimum length and material suitable for the tank
contents. There should be no block valve or other
restriction between the pilot valve and the actuator.
Wrap all pipe threads with fluoropolymer tape or
apply a suitable pipe thread sealant sparingly. Before
connecting sense line, backflow compressed air
through line and pick-up fitting in relief valve to
assure that no obstruction exists. Connect sense line
to relief valve and pilot valve with no in-line block
valve or other restriction. If a check valve is used in
the sense line for backflow prevention, make sure it
is unrestricted and installed with the correct flow
direction (Fig 8). The same procedures and
precautions apply if a remote sense line is used.
Field test connection, manual/remote blowdown and
pilot discharge connections, if applicable, must be
connected according to the Fig. 8, 9 and 10. Set
pressure and blowdown adjustment may be done on
the test bench (following the procedure on page 11)
or on the relief valve. The initial set pressure and
spring range can be found on the pilot valve
nameplate.
OPERATION
Both relief pressure and blowdown are set at the
factory to comply with the specification on the
purchase order. If blowdown is not specified, snap
action with 7-10% blowdown will be furnished. The
range of adjustment will depend on the spring
installed and will be stamped on the nameplate. The
pressure setting may be changed within the designed
range either while on line or in a service shop.
Observe the proper setting and testing procedure in
this manual.